製造現場での歩留まりの低下は、見過ごすと生産コストの増加や納期遅延を招く重大なリスクとなります。しかし、その根本となる原因を把握していなければ、解決は見込めません。
そのため、歩留まりの原因を把握し、的確に対処することで、劇的な改善が見込めます。原因がはっきりすれば、歩留まり低下を解決するためのアプローチ手法も明確になるはずです。
この記事では、歩留まりが低下する原因や改善方法、改善によって期待できる効果をご紹介します。現場の歩留まりに悩んでいる方は、ぜひ最後までご覧ください。
また、以下ではおすすめの組み合わせはかりメーカーについて紹介しているので、ぜひ参考にしてみてください。
歩留まりとは?
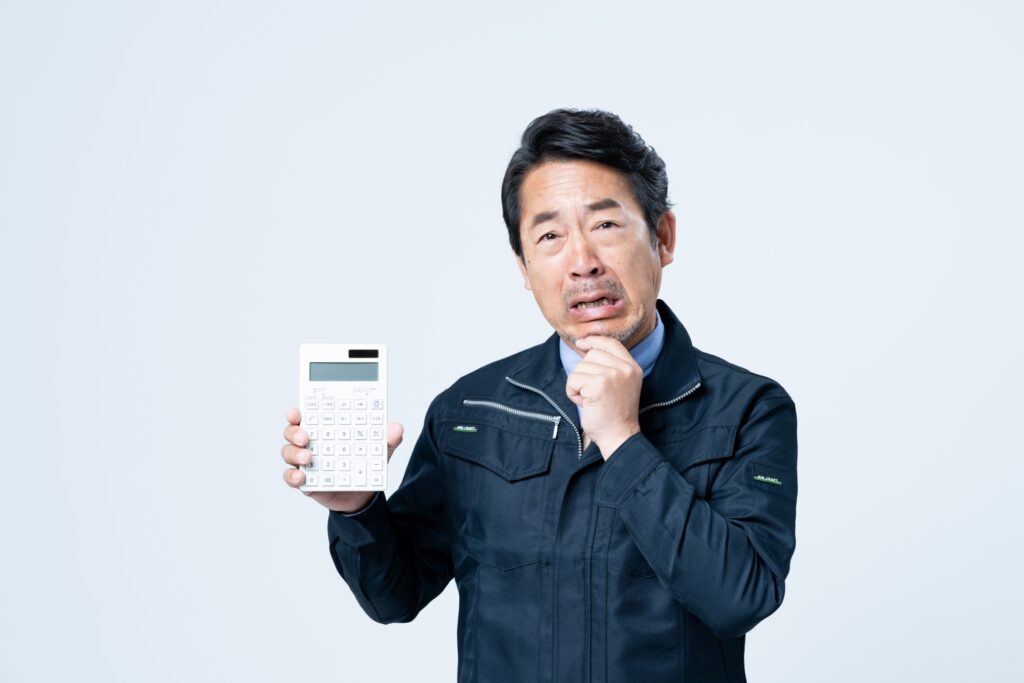
歩留まりとは、製造現場において投入した原材料のうち、実際に良品として出荷できる割合を示す指標です。例えば、100個の製品を製造する過程で、10個が不良品として廃棄された場合、歩留まりは90%となります。この数値が高いほど、無駄の少ない効率的な生産が行えていることを意味します。
製造業では、歩留まりの数値が収益や納期、品質に直結する重要な指標です。わずかな歩留まりの低下でも、長期的には大きな損失につながるため、定期的な確認と改善が欠かせません。
歩留まりを把握することで、どの工程で問題が発生しているかを可視化できるため、現場の改善活動においても重要な役割を果たします。
製造現場において歩留まりが重要な理由
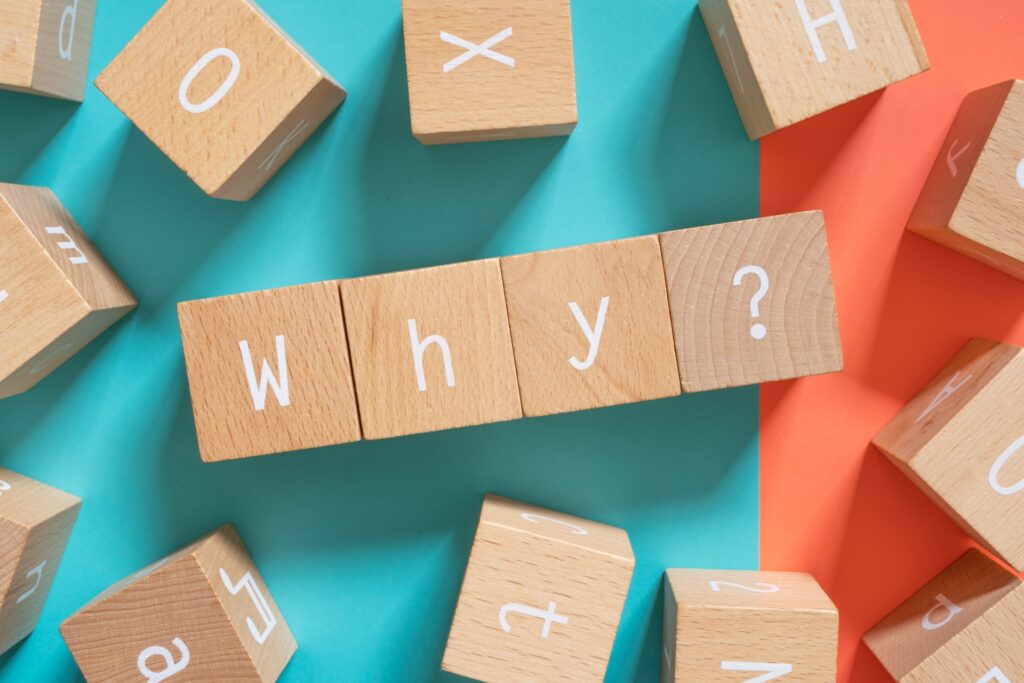
製造現場において歩留まりが重要視される理由は、主に以下の点にあります。
- コスト
- 品質
- 納期
まず、歩留まりが低下すると不良品の割合が増え、原材料や部品の無駄が増加します。これは直接的なコスト増につながるだけでなく、再製造や手直しによって人件費や機械稼働時間も余分にかかることになります。
また、品質面でも歩留まりの悪化は問題です。不良品が混入するリスクが高まることで、出荷後のクレームや返品、信頼の失墜を招く恐れがあります。特に医薬品や食品、電子機器など、高い品質が求められる業界では、歩留まりの低下は顧客離れを引き起こしかねません。
さらに、歩留まりが安定しないと納期の遅延にもつながります。製品が予定数生産できなければ、納入スケジュールが狂い、取引先との関係にも悪影響を及ぼします。
このように、歩留まりは単なる生産効率の指標ではなく、事業全体の信頼性と利益を左右する重要な要素となり得るのです。
歩留まり率の計算方法
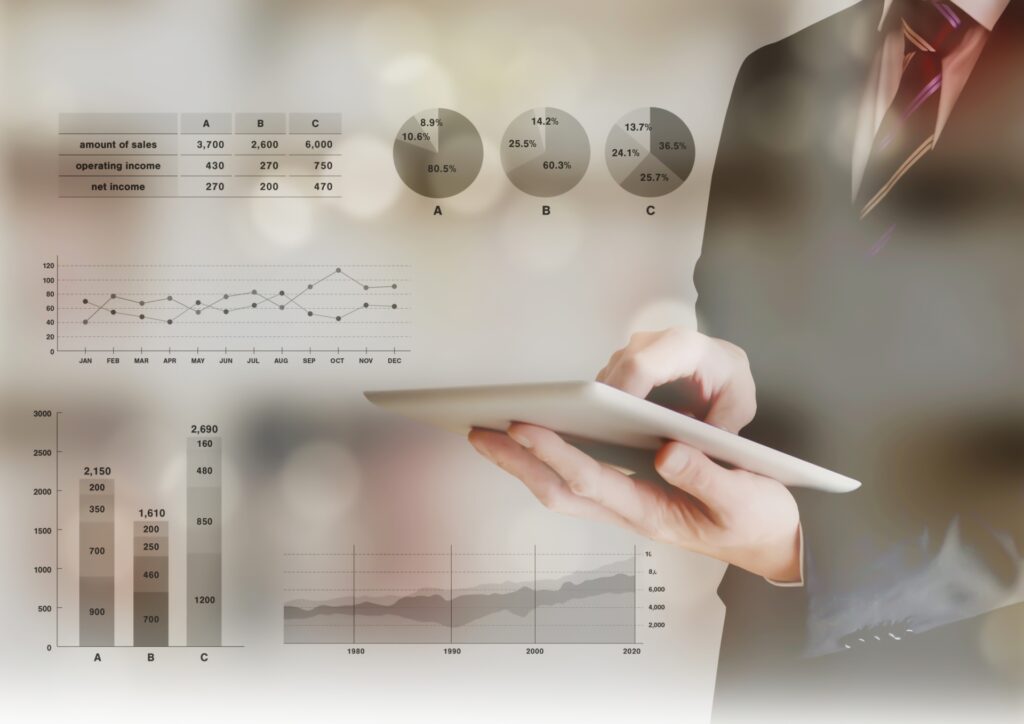
歩留まり率は、以下の計算式で求めることが可能です。
歩留まり率(%)=(良品数 ÷ 総生産数)× 100
例えば、ある製品を1,000個製造したうち、950個が出荷可能な良品であった場合、歩留まり率は次のように算出されます。
歩留まり率=(950 ÷ 1,000)× 100=95%
歩留まり率を継続的に追跡することで、工程ごとの改善状況を定量的に評価することが可能です。異常値が出た際には、どの工程で不良が発生したのかを特定する手がかりにもなります。
注意点としては、単に全体の良品数だけで判断せず、製品ごと・工程ごとに細かく管理することが求められます。特に多品種生産を行う現場では、製品ごとに歩留まり率を記録することで、隠れた問題の発見や改善の精度を高めることが可能です。
製造現場で歩留まりが低下する原因
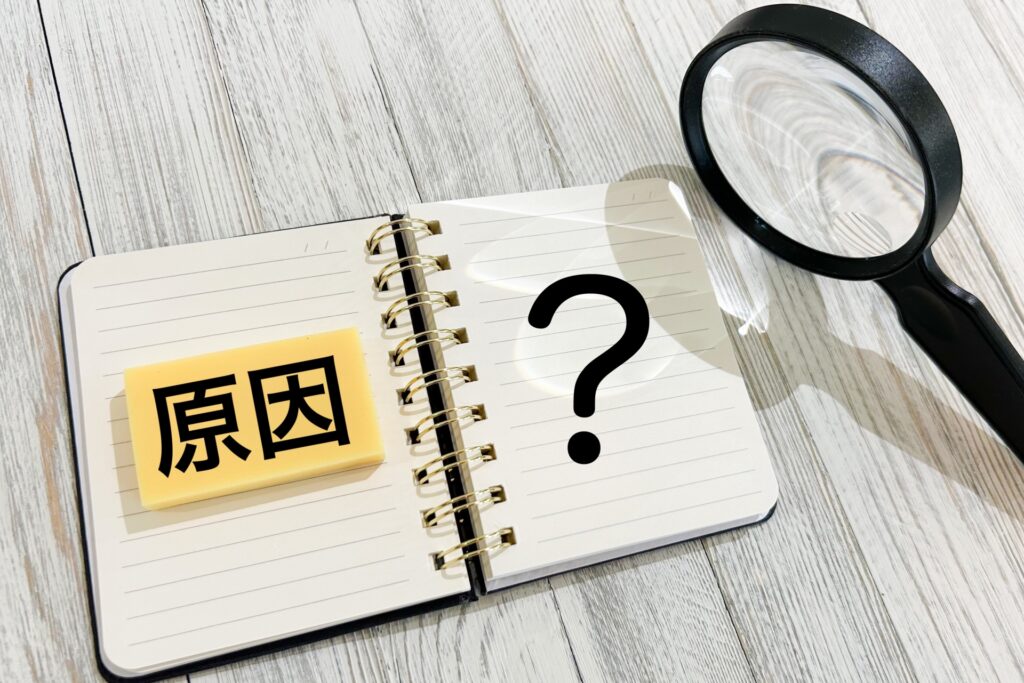
歩留まりの低下は、製造現場において重大な損失を招きます。その背景には、以下のような要因が複雑に絡んでいます。
以下では、歩留まりが下がる代表的な6つの原因について、それぞれ解説していきます。
設備・機械に起因する要因

歩留まり低下の原因として、設備や機械の不具合は多く見られます。老朽化した装置では、加工精度や供給速度にバラつきが生じやすく、不良品の発生率が高くなる直接の要因です。
また、定期的なメンテナンスが不十分だと、部品の摩耗やセンサーの誤作動によって、意図しない動作や停止が発生することもあります。さらに、生産設備と材料の相性が悪いのも、加工不良や詰まりなどの原因です。
新しいラインや機器を導入した際には、初期設定や調整不足により、歩留まりが一時的に下がることもあります。
材料・原料に起因する要因
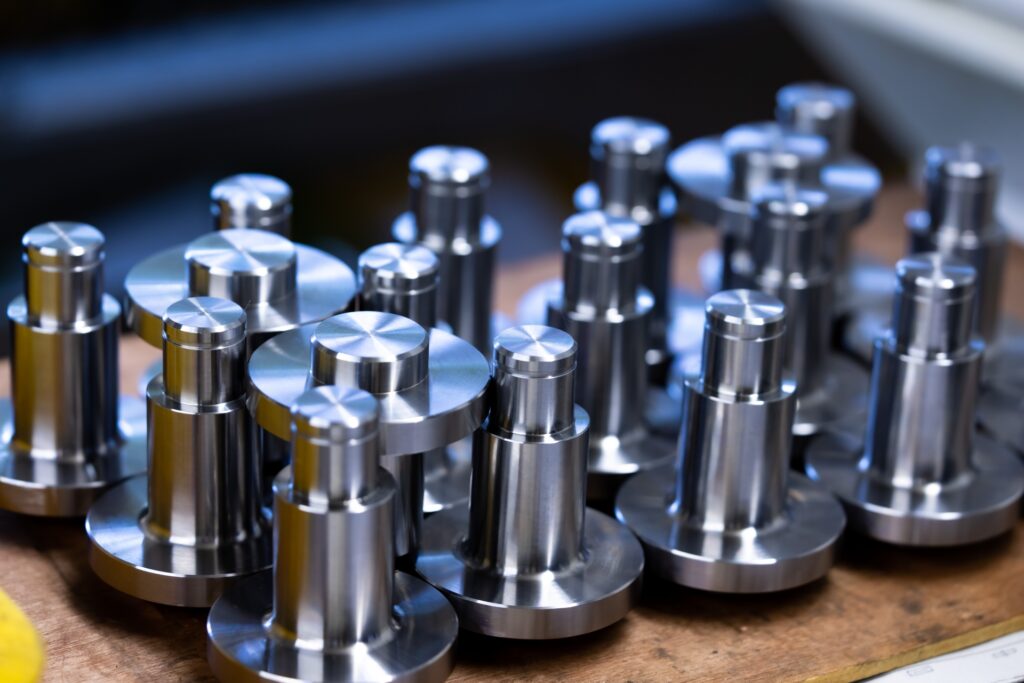
材料や原料の品質は、製品の完成度に直結するため、歩留まりに大きな影響を与えます。仕入れた原料に異物や不純物が含まれていた場合、製品に欠陥が生じる確率が高まります。原料の粒度や粘度、密度が安定していない場合も、加工精度が狂いやすく、不良率が高くなるでしょう。
また、同じ材料でもロットごとに性質が微妙に異なるケースがあり、それに気づかず使用を続けると、品質にムラが出て歩留まりが低下します。輸入原材料などでは、輸送中の温湿度管理が不十分なことが要因となることもあります。
対策としては、材料受け入れ時の検査を強化し、ロットごとの品質データを記録・分析する体制を整えることが有効です。
作業者に起因する要因
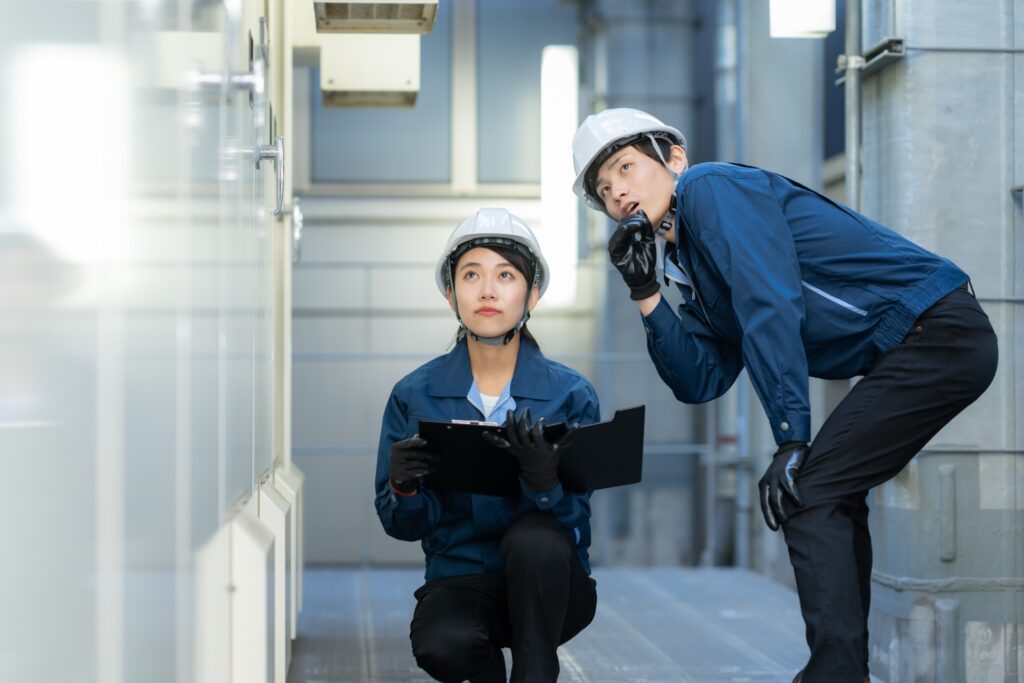
作業者のスキルや判断ミスも、歩留まり低下の原因です。特に手作業が多い工程では、作業手順のわずかな違いや集中力の欠如が、製品のばらつきにつながります。新人や慣れていない作業者による工程ミス、マニュアルの誤解も不良の原因となるでしょう。
また、教育訓練が不十分だったりすると、現場での判断に差が出てしまい、品質が安定しません。工程内での自己判断や経験による勘で作業が行われている現場では、再現性が確保されず、歩留まりの改善が難しくなります。
このような問題に対しては、標準作業書の整備と定期的な教育訓練が効果的です。さらに、作業ごとにチェックシートを設けることで、ミスの早期発見と作業品質の平準化が図れます。
製造工程の設計不備
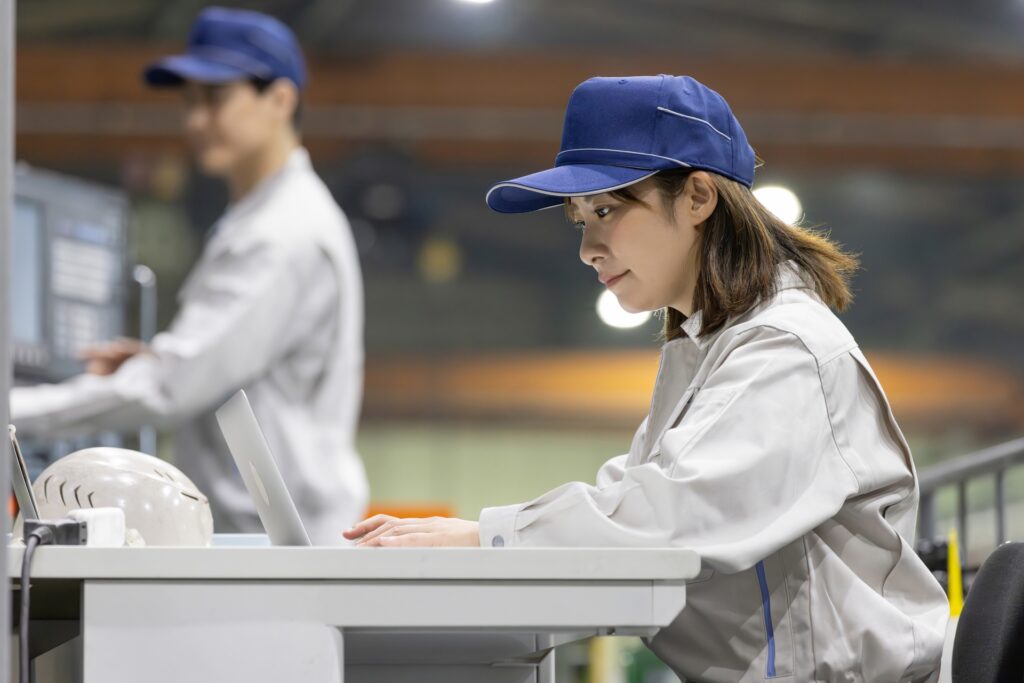
工程設計における不備も、歩留まりの悪化を招く大きな要因です。工程の順序が非効率である場合や、加工条件が適切に設定されていない場合、材料や設備のポテンシャルを十分に発揮できず、無駄が発生しやすくなります。
また、工程ごとの品質確認ポイントが不足していると、不良が後工程に持ち越される恐れがあります。製品仕様に対する製造条件の過不足や、搬送・段取りの不適切さも、歩留まりを下げる原因です。
こうした課題には、製造プロセスの見直しと工程FMEA(故障モード影響解析)などを用いたリスク評価が効果的です。
品質管理・検査体制の不備
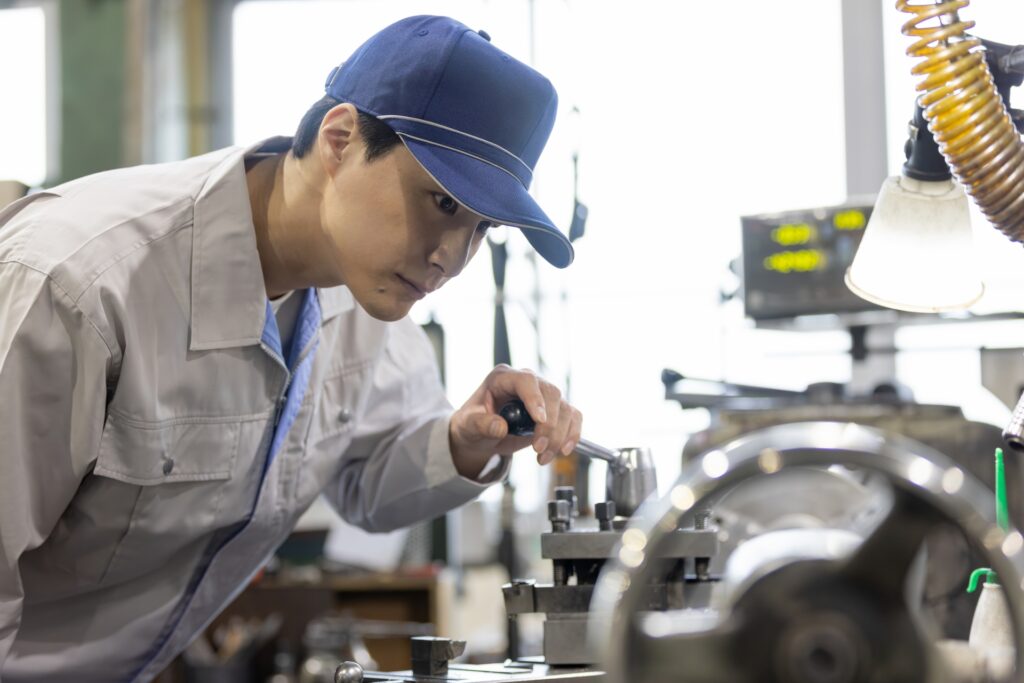
歩留まり低下の背景には、品質管理や検査体制の不備も多く見受けられます。検査基準が曖昧だったり、検査項目に漏れがあったりすると、不良品が見逃されやすくなります。目視検査に依存している現場では、作業者による判断のばらつきが顕著です。
また、検査結果を記録していない、もしくは活用していない場合、品質改善に向けた分析や再発防止策が立てにくくなります。工程内での抜き取り検査の頻度や方法に問題があると、製品全体の品質傾向を把握できません。
そのため、対策としては定量的な検査基準を整備し、誰が検査しても同じ結果となるようにすることが重要です。
外部環境・ロット変動の影響
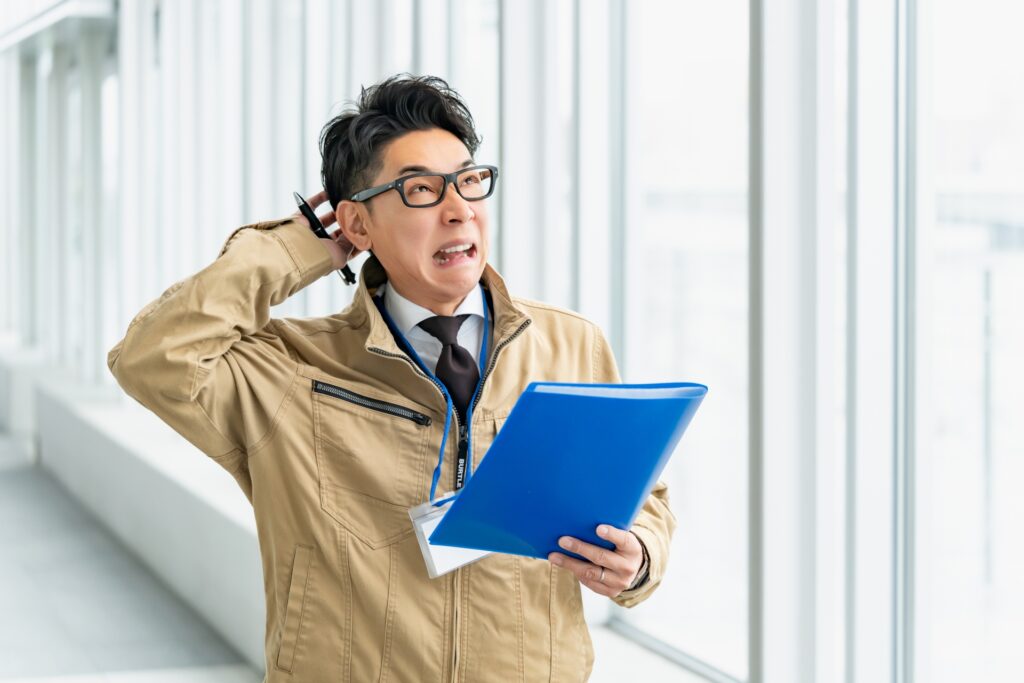
歩留まりは、現場内部の要因だけでなく、外部環境やロット変動の影響も受けます。例えば、気温や湿度が変化することで、原材料の性質や加工精度に影響が出ることがあります。
特に精密加工や化学反応を伴う製品では、環境の変動が不良発生に直結するケースが少なくありません。
また、原材料のロットごとの特性差や、仕入先の変更に伴う微細な品質変化なども、歩留まりに影響します。こうした変動が把握されていない場合、原因特定が難しく、対策も後手に回りがちです。
歩留まり低下を改善する方法
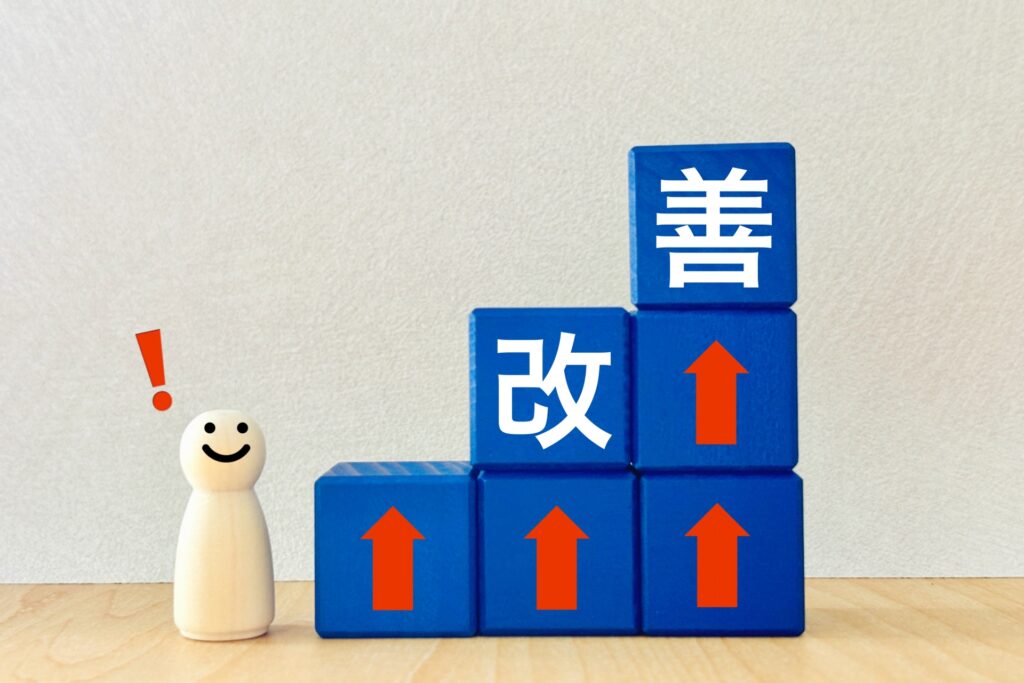
歩留まり低下の原因が多岐にわたる一方で、対策も多角的に講じることで、確実な改善が可能です。特定の要因に偏らず、工程・設備・人・材料・管理手法といった各側面から総合的に見直すことが重要です。
具体的には、以下のような改善方法があります。
それぞれの改善方法について解説していきます。
工程改善による対策
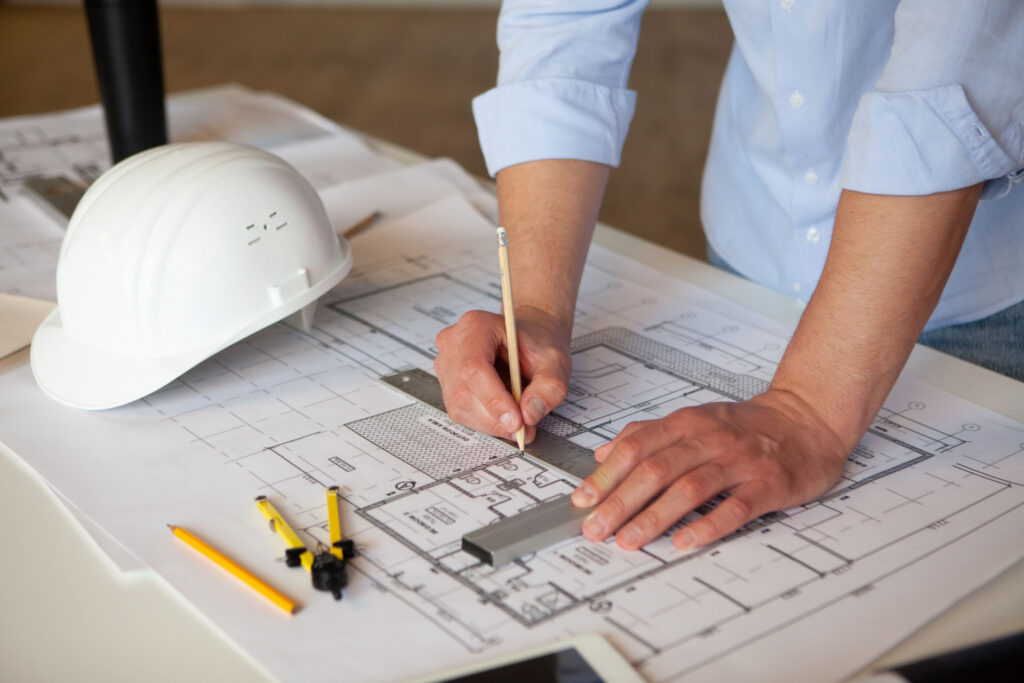
工程改善は、歩留まり向上において最も基本な対策です。現行の製造プロセスを分析し、無駄・ムラ・ムリがないかを洗い出すことで、不良の発生源を特定できます。
特にボトルネック工程の見直しや、作業手順の標準化は、品質と効率の両面で改善効果が期待できます。例えば、以下の項目の見直しによって、微細なズレや応力の偏りを解消し、製品のバラつきを抑えることが可能です。
- 加工順序
- 温度管理
- 搬送経路
また、工程内検査の頻度やタイミングを適正化することで、不良品の早期発見にもつながります。
改善活動は一度きりではなく、継続的に行うことが重要です。QCサークル活動や現場主導の改善を実施することで、現場に即した改善案が生まれやすくなり、成果も定着しやすくなります。
設備・装置の保守管理強化
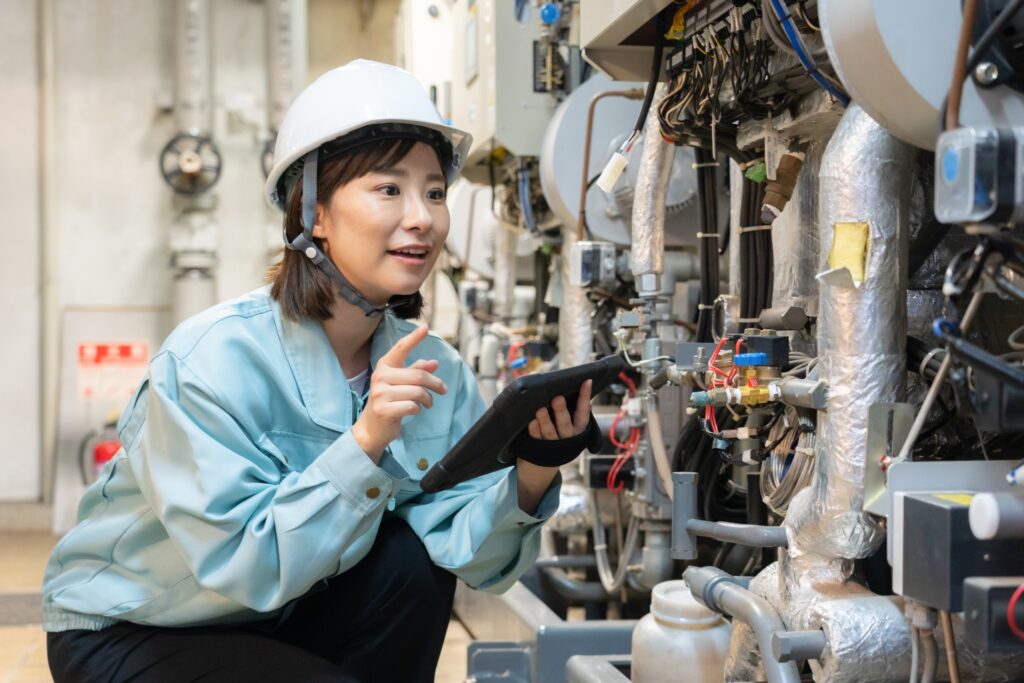
設備の安定稼働は、歩留まりの安定に直結する要因です。設備の老朽化や劣化、消耗品の摩耗が原因で不良品が発生するケースは多く、定期的な点検とメンテナンスが不可欠です。保守管理を強化することで、突発的なトラブルを未然に防ぎます。
そのためには、点検項目の明確化と保守履歴の記録が必要です。部品の交換時期や過去のトラブル情報を共有することで、予防保全に役立ちます。さらに、振動センサーや温度センサーなどを活用し、異常の兆候をリアルタイムで監視する仕組みを構築することも有効です。
また、設備の操作方法や条件設定が標準化されていない場合は、オペレーターごとにばらつきが生じ、品質不良の原因となります。そのため、操作マニュアルの整備や自動制御化も併せて検討するとよいでしょう。
原材料の品質管理とトレーサビリティ強化
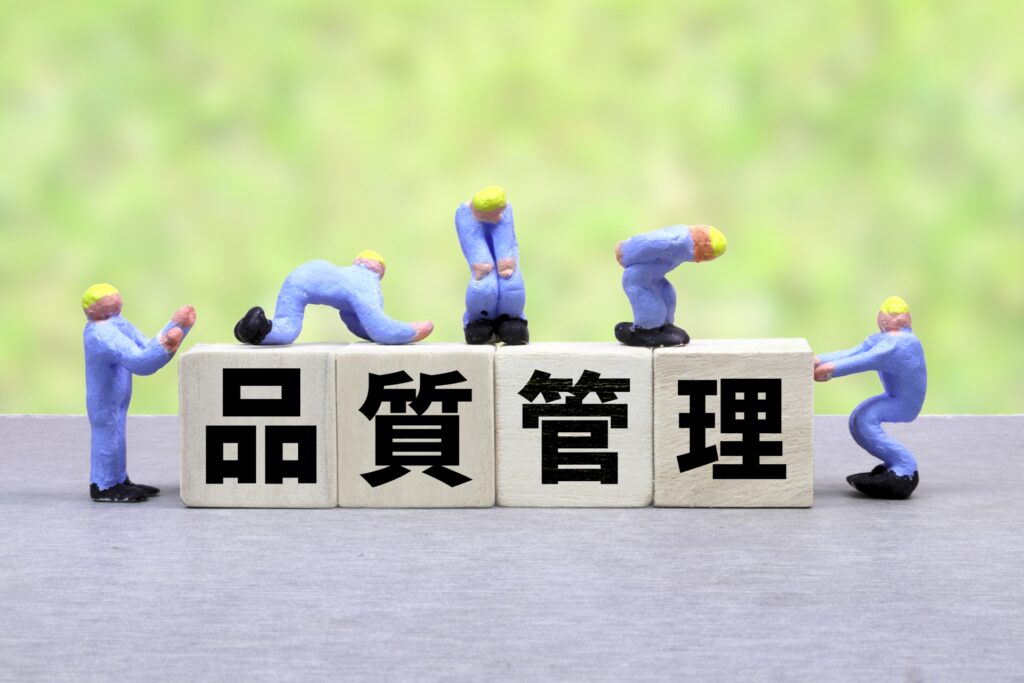
原材料の品質は、製品の仕上がりに大きく影響します。そのため、材料受入時の検査体制を強化し、不良品の元となる原料を事前に排除することが必要です。特に以下のような要素は、加工中に不具合を生じさせるため、厳密なチェックが求められます。
- 異物混入
- 粒度不良
- 水分量の偏り
また、トレーサビリティの確保も重要です。原材料ごとにロット番号や入荷日などを記録・管理することで、万が一不具合が発生した際にも速やかに原因を特定し、対策を講じることが可能です。
さらに、原材料の安定調達のためには、仕入先との連携と品質要求の明文化が不可欠です。定期的な品質監査や仕様の再確認を行うことで、品質のばらつきを最小限に抑えられるでしょう。
AI・IoTによる監視・検査システムの導入
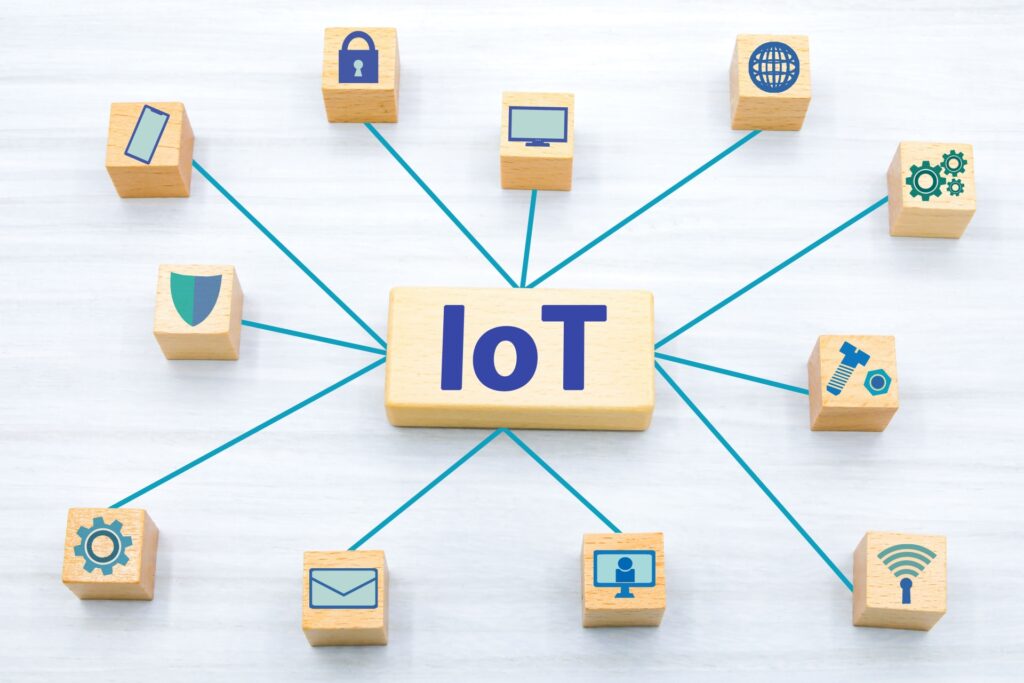
最新のAIやIoT技術を活用することで、歩留まりの改善は飛躍的に進化します。例えば、画像認識AIを搭載した自動検査装置は、目視では見落としがちな微細なキズや汚れを高精度に検出できます。これにより、検査品質の安定化と省人化が同時に実現可能です。
また、IoTセンサーを活用した設備状態の常時監視は、機械の異常を早期に発見し、予防保全につなげる手段として有効です。生産ライン全体の稼働データを収集・分析することで、不良発生の傾向や時間帯などのパターンも把握しやすくなります。
AIの最新技術を積極的に取り入れることで、現場の改善速度を大幅に高めることが期待できるでしょう。
人材教育・技能継承
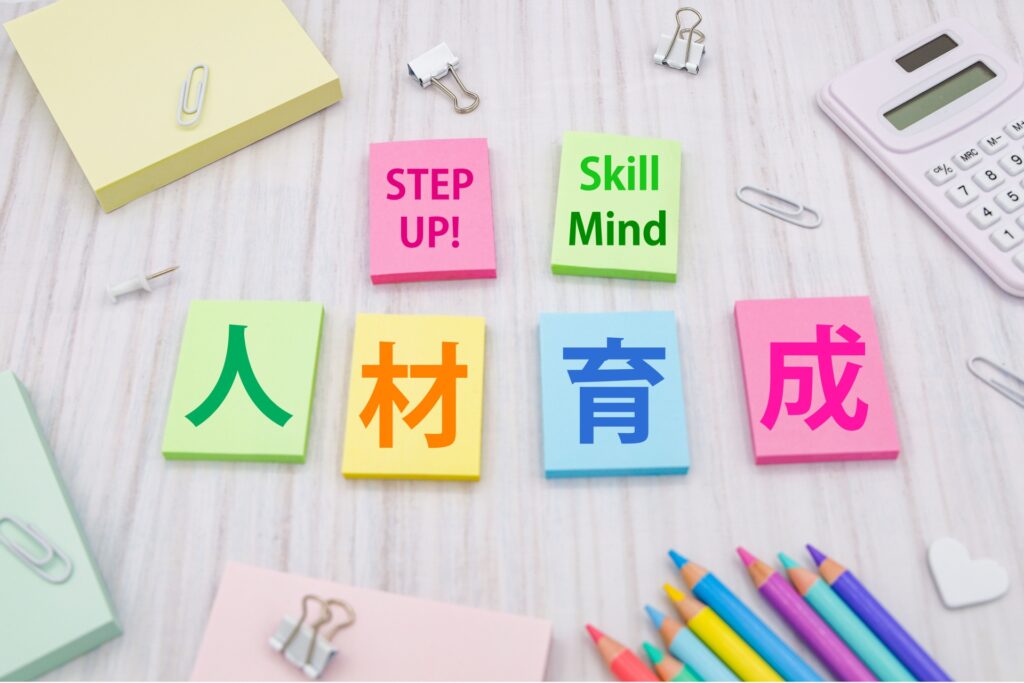
作業者の技術力や意識は、歩留まりの安定に不可欠な要素です。経験や知識の差が作業品質に直結するため、継続的な教育と技能継承が必要になります。特に属人化している作業や、感覚に頼った手作業工程では、新人や非熟練者による不良の発生率が高くなりがちです。
まずは、標準作業手順書(SOP)の整備し、活用できるようにしましょう。誰が作業しても同じ品質が保てるよう、わかりやすい手順書と動画などの視覚的教材を併用することが重要です。
OJTだけでなく、定期的なスキル確認テストや社内検定制度を導入することで、現場力の底上げにつながります。さらに、熟練者による技能の形式知化も重要です。暗黙知を見える化し、教育資料として残すことで、世代交代による技術断絶を防ぎます。
品質分析とPDCAサイクルの実践
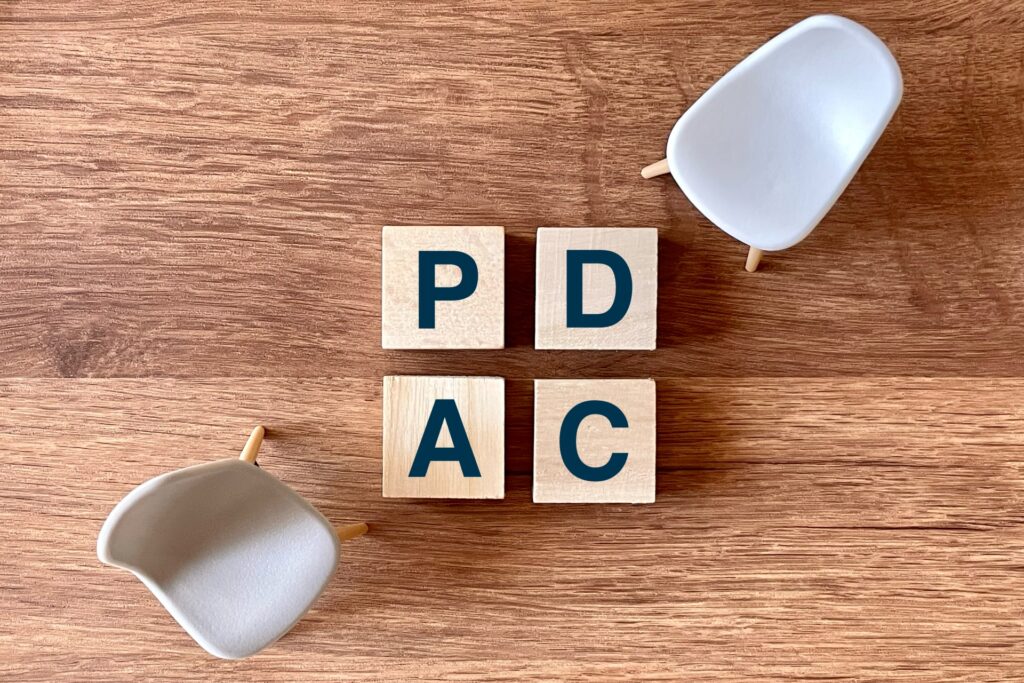
歩留まり改善においては、原因を明確に把握し、継続的に改善活動を進めることが重要です。そのためには、品質データを活用した分析と、PDCAサイクルの徹底が欠かせません。
まず、工程ごとの不良率や傾向をデータで可視化し、どの工程に問題が集中しているかを明らかにします。次に、原因を仮説立てして対策を講じ、効果を検証するという流れを定着させることで、根本的な改善が可能になります。
PDCAサイクルにおいては、特に「Check」と「Action」の段階を重視し、改善策の効果を数値で評価することがポイントです。また、分析には以下のようなQC手法を活用することで、より精度の高い改善が実現できます。
- ヒストグラム
- パレート図
- 特性要因図(フィッシュボーン)
全体の品質管理体制を底上げしながら、歩留まり改善に直結する取り組みを積み重ねることが、安定した生産の実現につながります。
歩留まり改善によって得られる効果
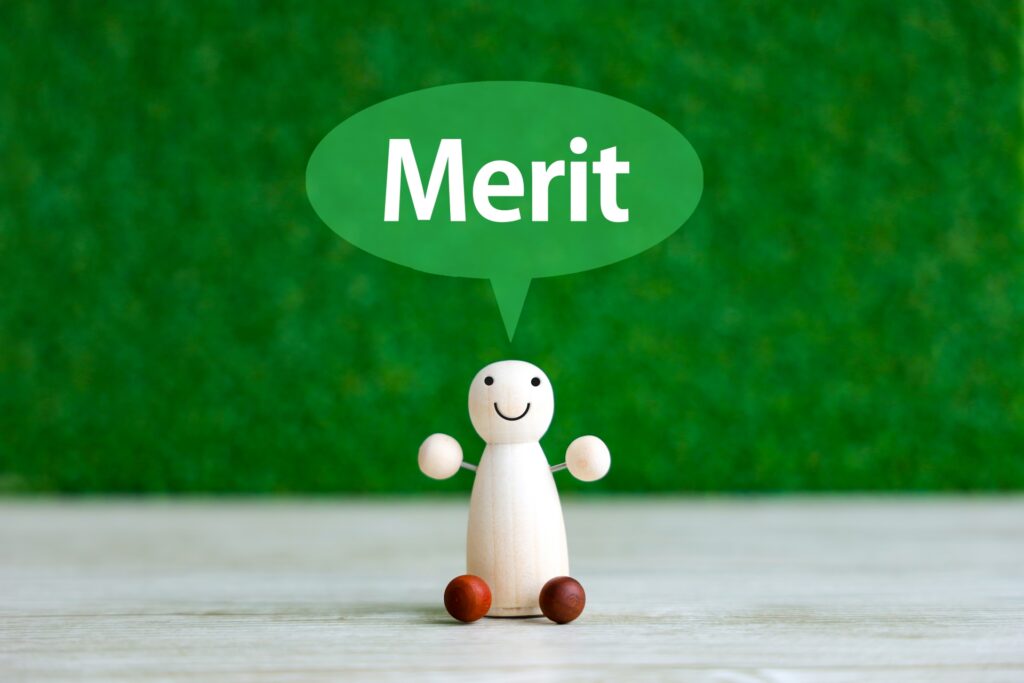
歩留まりを改善することは、単に不良品を減らすだけではありません。製造現場全体に波及効果をもたらし、コスト削減・品質向上・納期遵守といった多方面の成果につながります。具体的な効果としては、以下の通りです。
それぞれの効果について解説していきます。
製造原価の圧縮
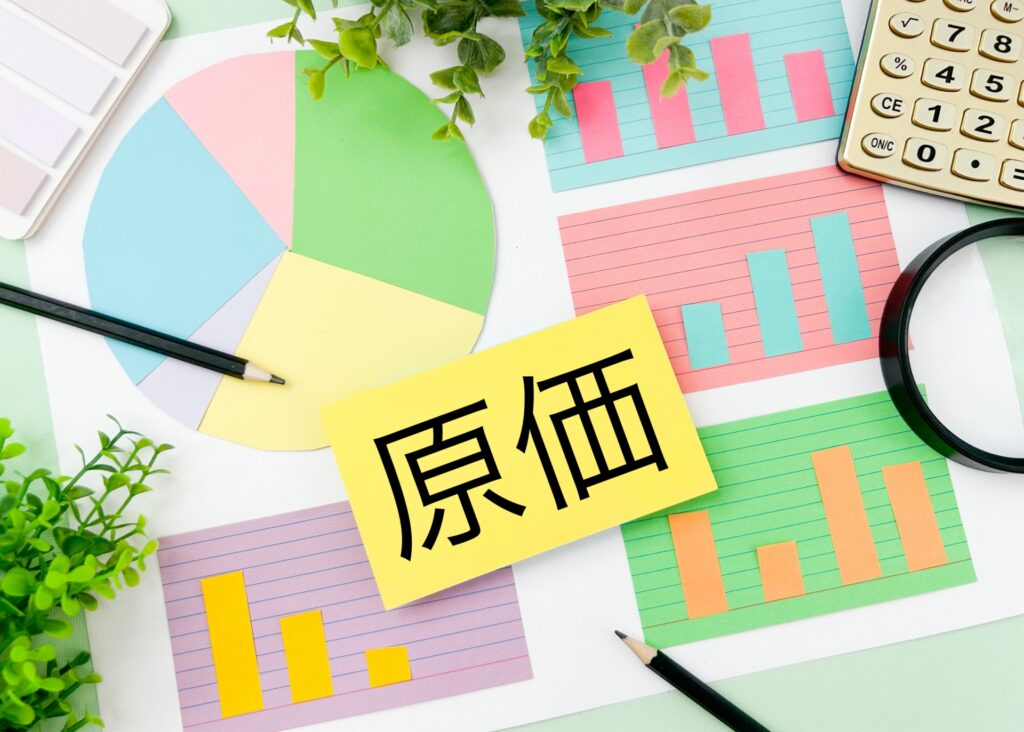
歩留まりが改善されることで、最も顕著に現れるのが製造原価の削減です。不良品が減るということは、それだけ原材料や部品、作業時間の無駄が削減されることを意味します。
また、原価の削減に伴い加工途中でのロスや再加工による手間が減るため、人件費やエネルギーコストの面でもメリットがあります。特に高価な原材料や部品を使用している場合、歩留まりの向上はダイレクトに利益に直結するでしょう。
さらに、製造原価が安定することで、価格競争力のある製品づくりが可能となり、市場での競争優位性を高める要因にもなります。継続的な歩留まり改善によって、製品ごとのコスト構造を最適化できれば、収益体質の強化にもつながります。
不良品対応の削減
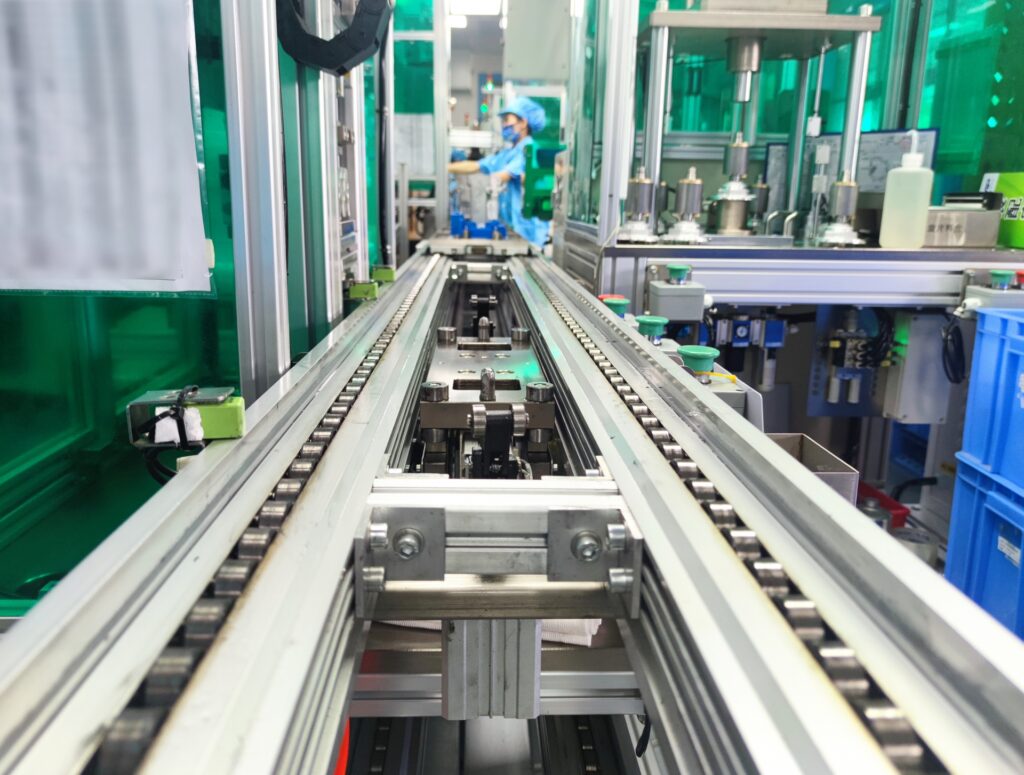
歩留まりの向上は、不良品発生に伴う対応工数の削減にも寄与します。不良品が発生した場合には、原因調査・再製造・報告書作成・取引先への連絡といった対応が必要になりますが、これらの業務は本来の生産活動とは直接関係なく、企業にとっては非効率なコストです。
また、顧客からのクレームや返品が発生すれば、信頼の低下や売上損失といった二次的な影響も避けられません。歩留まりが高い状態を維持できれば、こうしたリスクを回避でき、品質に対する安心感を顧客に与えることが可能です。
納期遵守率・供給安定性の向上
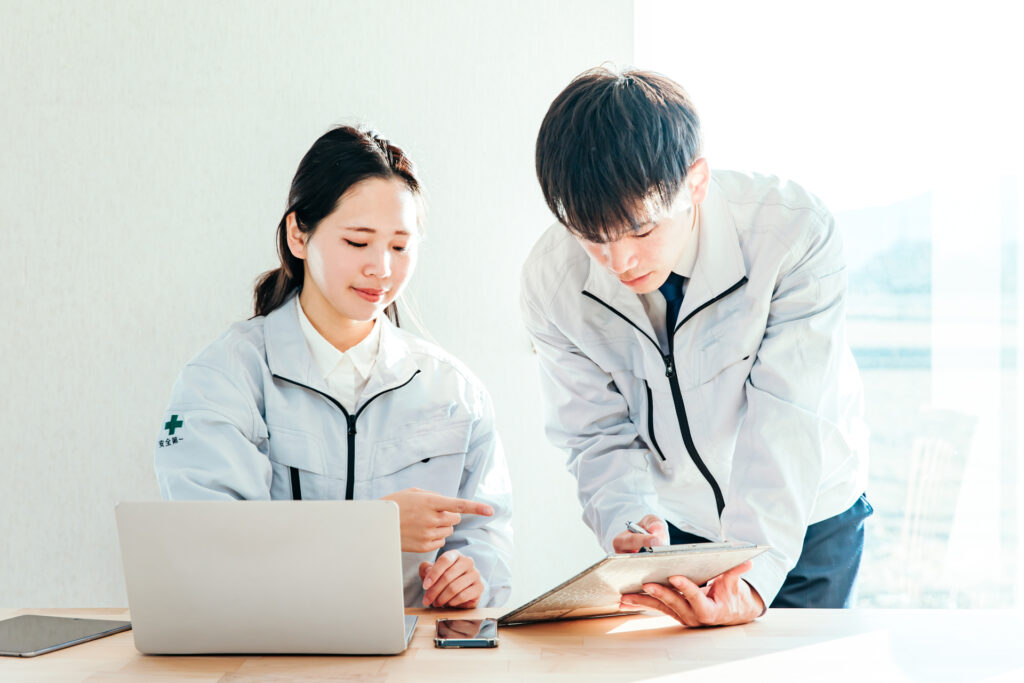
歩留まりの改善は、納期の遵守や製品供給の安定化にも貢献します。
歩留まりが低下している現場では、不良品の再製造や再検査に時間を要し、予定通りに出荷できない事態に陥りがちです。これによって納期の遅延や計画変更が頻発し、顧客からの信頼を損なうリスクが高まります。
一方で、歩留まりが安定していれば、予定通りの数量を確保しやすく、無駄なリードタイムの発生も抑えられます。結果として生産スケジュールが守られやすくなり、納期遵守率が向上するでしょう。
特に、ジャストインタイムを重視する取引先に対しては、安定供給の実現が大きな強みとなります。さらに、急な追加注文やトラブル発生時にも対応できる生産余力が生まれるため、ビジネスの拡大や新規受注にもつながります。
設備稼働効率の向上
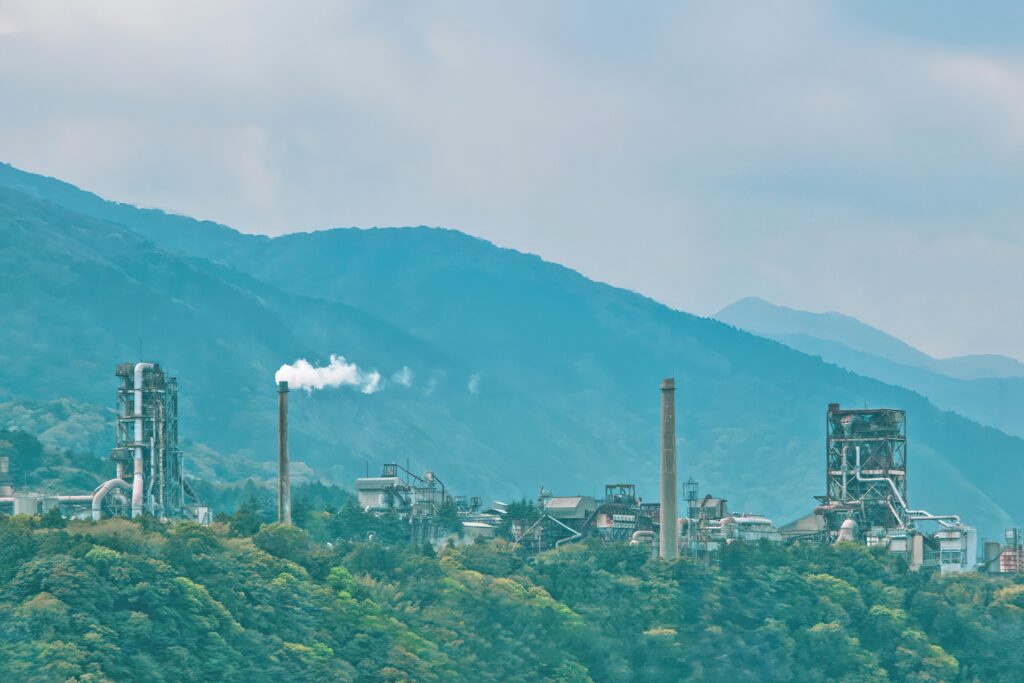
歩留まりの向上は、設備の稼働効率(OEE)にも直接影響を与えます。不良品の発生率が高いと、ライン停止や再加工のための段取り替え、調整作業が必要となり、設備の稼働時間が減少してしまうでしょう。これにより、せっかくの高性能な機械も能力を十分に発揮できない状態に陥ります。
一方で、歩留まりが改善されると、ラインがスムーズに流れ、停止時間が減少します。また、品質不良による作業中断や不具合対応の頻度が減ることで、全体の稼働率が向上します。生産能力の最大化を図るうえで、歩留まりの改善は重要な指標です。
さらに、稼働率が向上すれば、同じ時間・同じ設備でより多くの製品を製造できるため、設備投資の回収期間短縮やROIの向上にもつながります。
おすすめの全自動組み合わせはかりメーカー3選
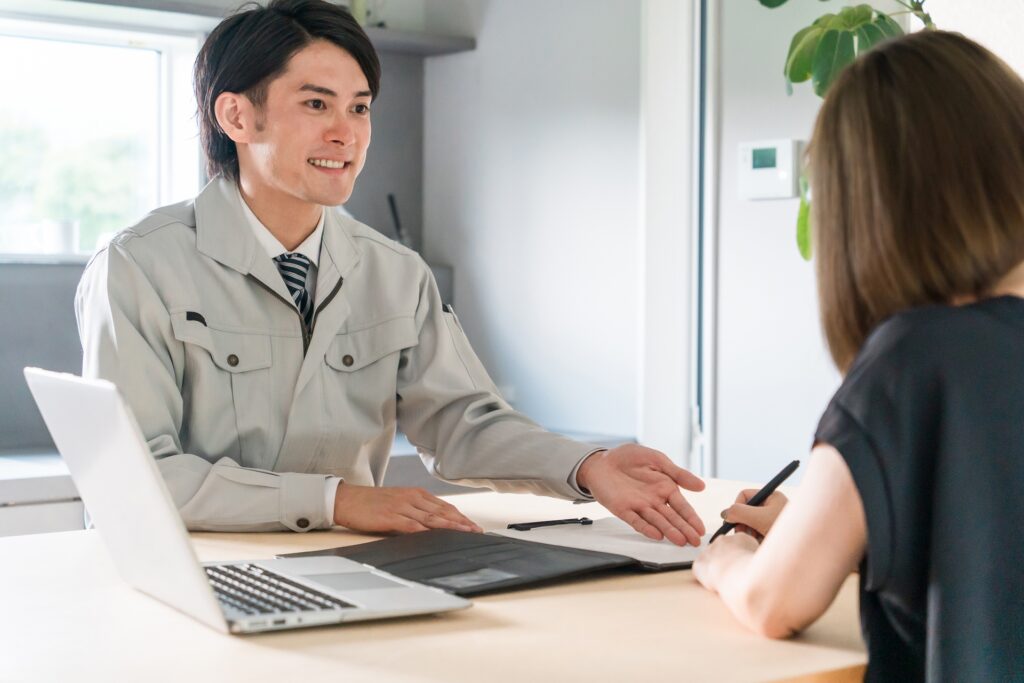
歩留まり改善や生産効率の向上を実現する上で、全自動組み合わせはかりの導入は効果的です。特に食品や医薬品、部品などを正確かつスピーディーに計量・選別する現場では、組み合わせはかりの性能が製品の品質や生産スピードに直結します。
信頼性と実績に優れた全自動組み合わせはかりメーカーとして、以下の3社をご紹介します。
自社の課題に合ったメーカー選定の参考として、ぜひお役立てください。
大和製衡株式会社
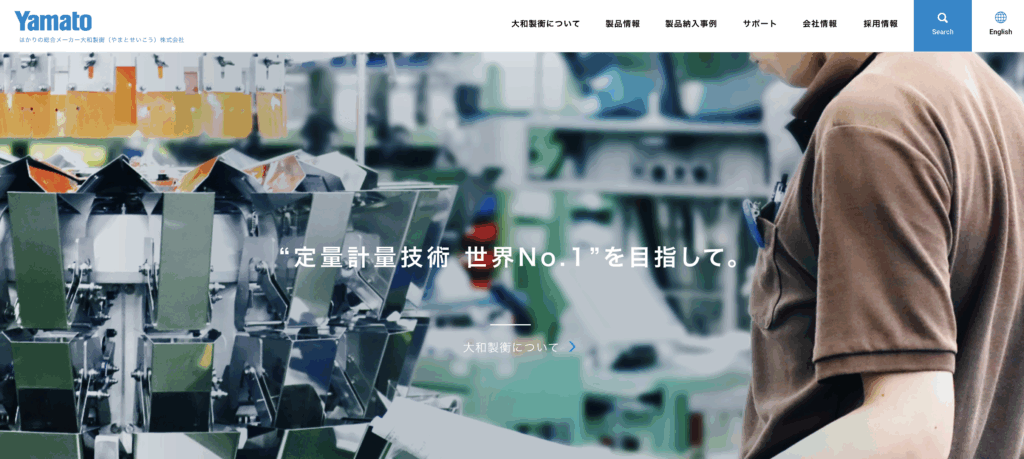
大和製衡株式会社は、兵庫県明石市に本社を構える老舗の計量機器メーカーで、組み合わせはかり分野において高い技術力を誇ります。同社の組み合わせはかりは、食品業界をはじめ、医薬品・工業製品など幅広い分野で導入されています。
項目 | 詳細 |
会社名 | 大和製衡株式会社 |
住所 | 〒673-8688(〒673-0849) 兵庫県明石市茶園場町5番22号 |
電話番号 | 078-918-5526 |
公式HP | https://www.yamato-scale.co.jp/ |
独自の重量演算アルゴリズムにより、計量スピードと正確さを両立しており、設定値に対する歩留まりの最適化も可能です。また、防塵・防水設計のモデルも充実しており、衛生管理が求められる現場でも安心して使用できます。
さらに、現場に即したカスタマイズ対応にも定評があり、工程に応じたライン設計や自動化との連携も柔軟に対応可能です。国内でのサポート体制も充実しており、導入後の保守や教育にも力を入れています。
全自動組み合わせはかりの導入をお考えの方は、一度の大和製衡株式会社ホームページを訪れてはいかがでしょうか。
以下の記事では、大和製衡株式会社の特徴や口コミ、導入事例などをさらに詳しく解説していますので、気になる方はぜひ一度チェックしてみてください。
株式会社イシダ
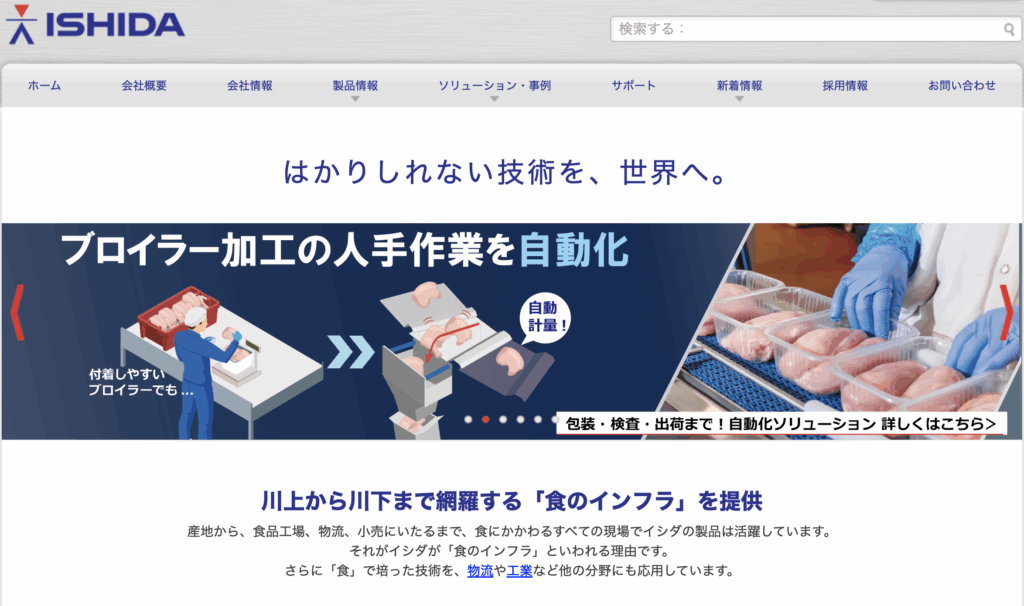
株式会社イシダは、京都に本社を構える総合計量機器メーカーで、全自動組み合わせはかりの分野において世界的なリーダー企業の一つです。
項目 | 詳細 |
会社名 | 株式会社イシダ |
住所 | 〒606-8392 京都市左京区聖護院山王町44番地 |
電話番号 | 075-771-4141 |
公式HP | https://www.ishida.co.jp/ww/jp/ |
イシダの製品は、優れた操作性と高速・高精度な計量機能が特長です。マルチヘッド構造による組み合わせ演算により、歩留まりを最小限に抑え、材料の無駄を大幅に削減できます。
さらに、ライン全体の自動化・省人化を支援する多彩なオプションと、異物検査機や包装機とのシームレスな連携が可能です。アフターサービス体制も国内外に広がっており、トラブル発生時の迅速な対応が期待できます。
以下の記事では株式会社イシダの評判や特徴について紹介しているので、ぜひ参考にしてください。
アンリツ株式会社
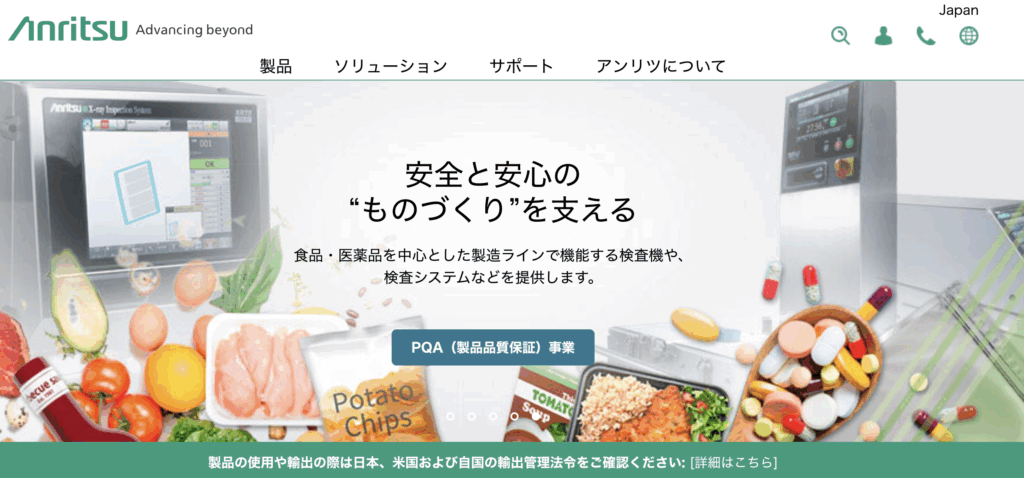
アンリツ株式会社は、通信機器メーカーとしてのイメージが強い企業ですが、実は検査機器や計量機器の分野においても高い実績を持っています。全自動組み合わせはかりでは、食品や医薬品などの現場に向けて、高性能なソリューションを展開しています。
項目 | 詳細 |
会社名 | アンリツ株式会社 |
住所 | 〒243-8555 神奈川県厚木市恩名5-1-1 |
電話番号 | 046-223-1111 |
公式HP | https://www.anritsu.com/ja-jp/ |
アンリツの組み合わせはかりは、コンパクト設計でありながら、極めて高精度な重量演算を実現しており、スペースに制限のある生産ラインでも効率的に運用できます。また、自社開発のセンサー技術を応用した高感度な検出機能により、わずかな重量誤差も見逃しません。
さらに、トレース性の高い記録管理機能を搭載しており、歩留まり管理や品質保証の面でも強みを発揮します。小規模ラインから高負荷生産まで柔軟に対応可能な点も魅力で、現場ニーズに応じた多様な提案力を持つメーカーです。
以下の記事ではアンリツ株式会社の評判や特徴について紹介しているので、ぜひ参考にしてください。
まとめ
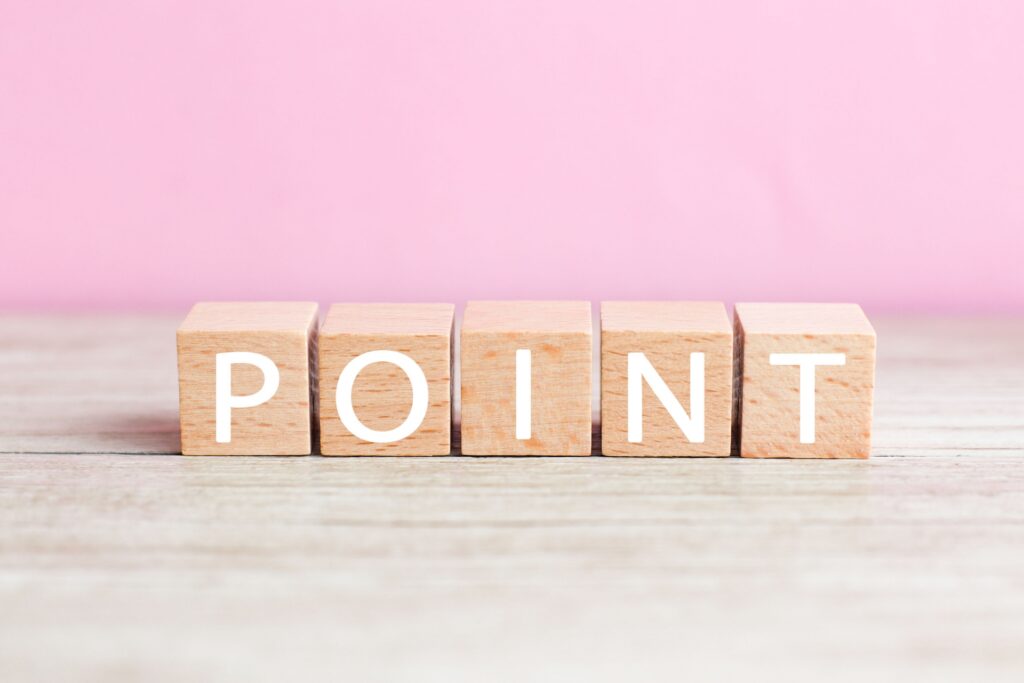
歩留まりの低下は、製造現場におけるコスト増や品質不良、納期遅延といった深刻な課題を引き起こします。しかし、その原因を正しく把握し、工程・設備・人材・検査体制などを多角的に見直すことで、改善は十分に可能です。
特に全自動組み合わせはかりの導入は、計量精度と効率を両立させ、歩留まり改善に大きく貢献します。
本記事で紹介した内容をもとに、まずは自社の不良発生要因を整理し、改善すべきポイントを明確にしましょう。そして、改善策の実施と効果検証を繰り返すことで、安定した生産体制と高い品質の両立が実現できます。