製造現場において、慢性的な人手不足に頭を抱える方も多いはずです。製造業界では近年、採用難や高齢化に伴い、人手の確保がますます困難になっています。
このままでは、生産効率の低下や納期遅延といった深刻な影響を及ぼしかねません。しかし、課題の本質を見極め、適切な対策を講じることで、人手不足をチャンスに変えることも可能です。
本記事では、製造業界における人手不足の現状を整理し、その影響や解決策をご紹介します。これからの製造現場を支える持続可能な取り組みに挑戦したい方は、ぜひ最後までご覧ください。
また、以下ではおすすめの組み合わせはかりメーカーについて紹介しているので、ぜひ参考にしてみてください。
製造業界が直面する人手不足の現状
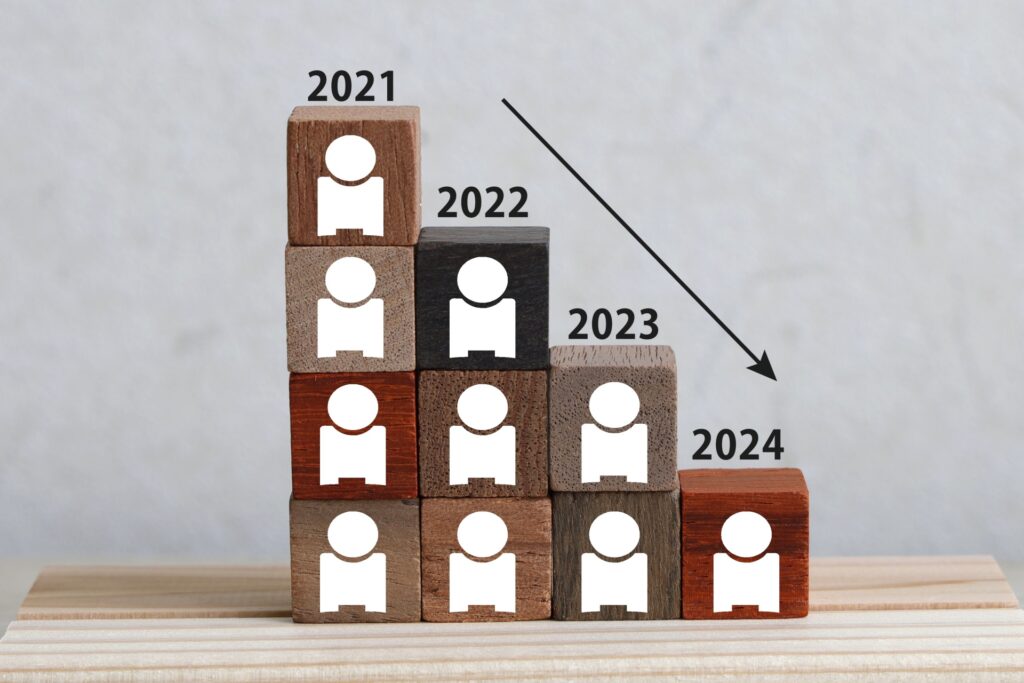
製造業では慢性的な人手不足が深刻化しており、就業者数や有効求人倍率からその深刻さが浮かび上がります。以下では、求人倍率と労働人口に注目して、製造業界を見ていきましょう。
有効求人倍率:1.25倍(令和6年11月時点)
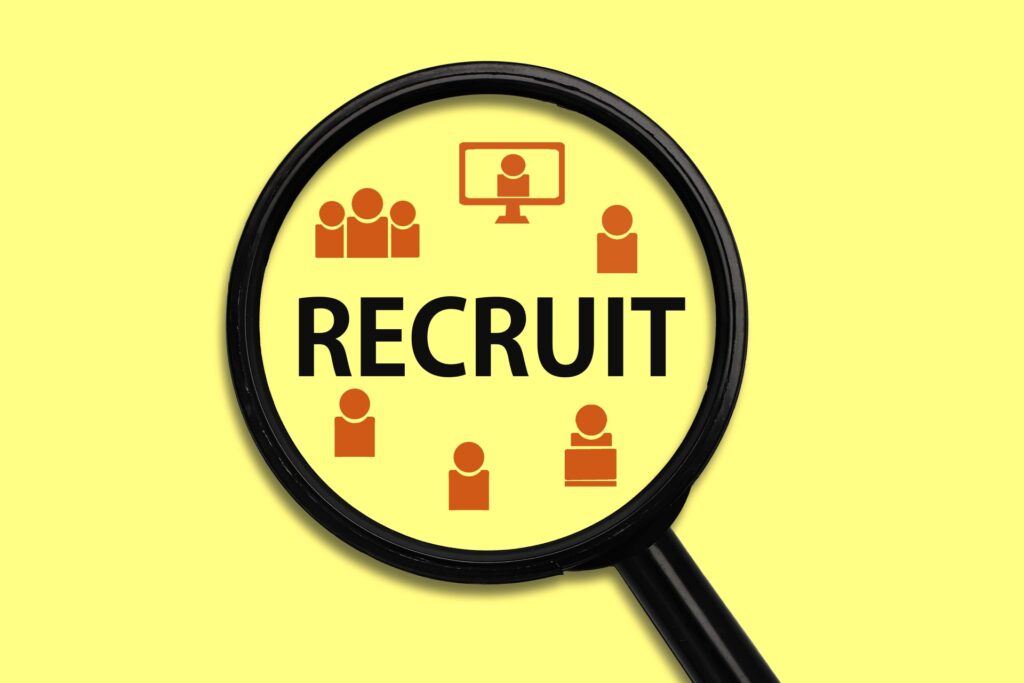
製造業における有効求人倍率は、全国平均の1.25倍を超える高水準で推移しており、人手不足が常態化していることを示しています。令和6年11月時点の厚生労働省資料では全職業の平均が1.25倍の一方、「生産工程の職業」における倍率は1.50倍、機械整備・修理職では4倍超という職種も存在します。
有効求人倍率は以下の計算式で算出されますが、倍率が1を超えると求人が多い状態、つまり求職者に対して募集が多い状況を意味します。
有効求人倍率 = 求人件数÷求職者数
製造業では特に倍率が高いため、企業間での採用競争が激化しており、魅力的な求人条件や現場改善が急務となっているのです。
労働人口:157万人が減少している
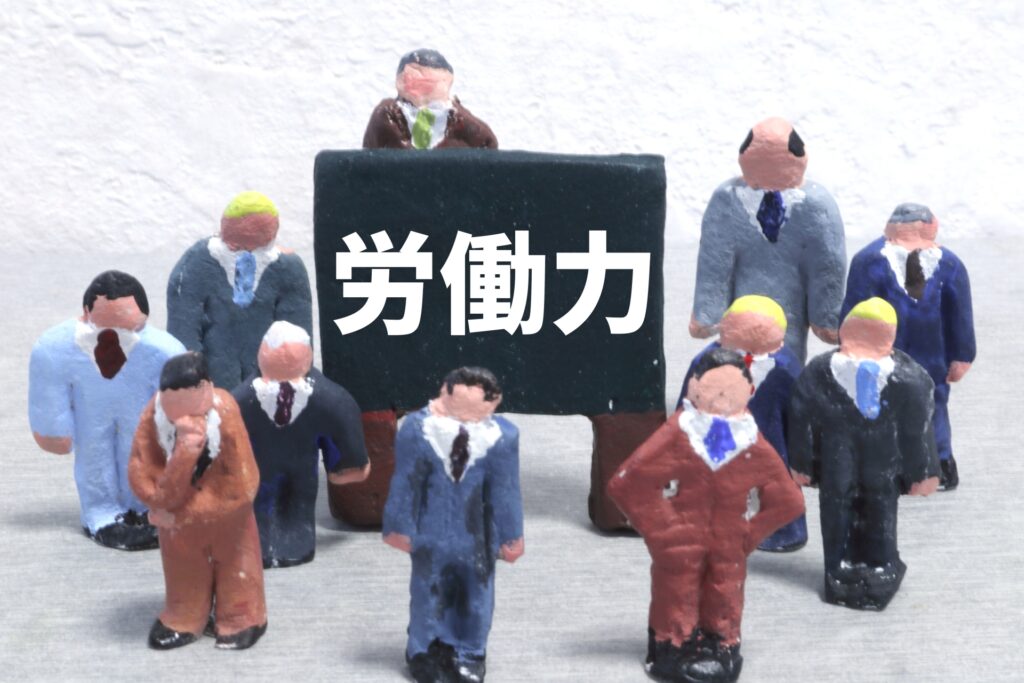
製造業の現場では、労働人口の大幅な減少が深刻な問題となっています。経済産業省などによる調査では、2002年から2021年にかけて製造業の就業者数が約157万人減少しており、全産業に占める割合も3.4ポイント低下しました。さらに、34歳以下の若年層が121万人減少しており、これは次世代の労働力不足と技能継承の断絶につながる懸念です。
一方で、65歳以上の就業者は33万人増加し、高齢化による人材構成の偏りも顕著です。このように若年層の減少と高齢化の進行が同時に進んでいる現状では、人材確保と人材育成の両輪で戦略を立てる必要があります。
製造業が人手不足に陥る根本的な理由
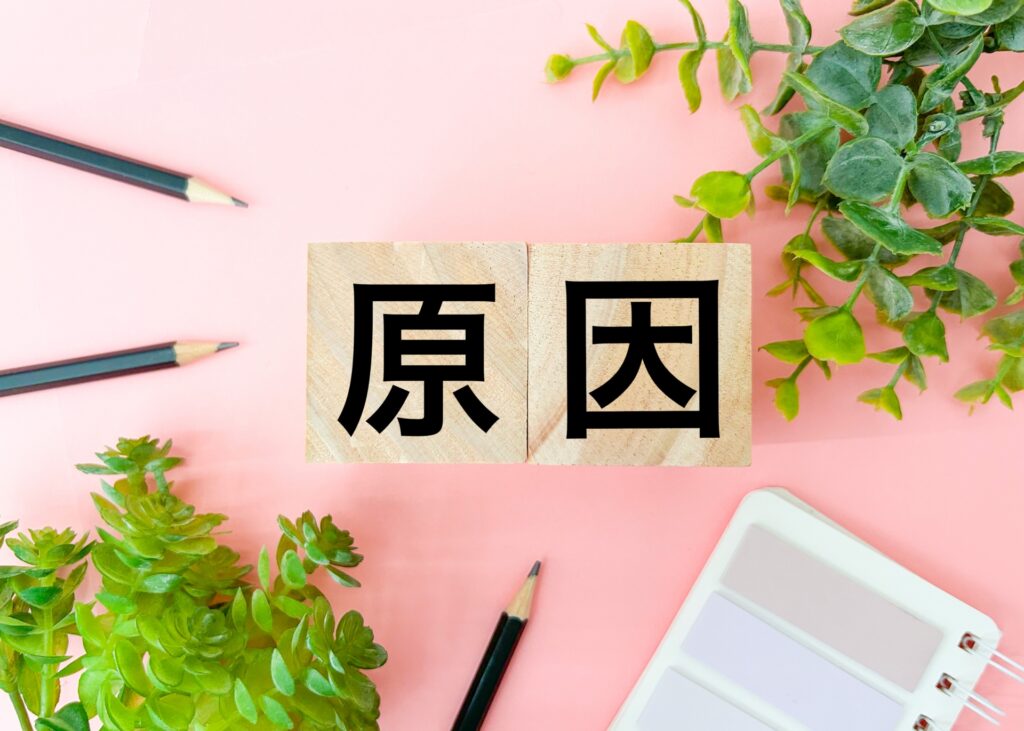
製造業が慢性的な人手不足に陥っている背景には、単なる少子高齢化だけでは説明しきれない、業界特有の根本的な課題が潜んでいます。特に若年層の就業者が減少し続けている一因には、仕事として選ばれにくい要素が存在します。
具体的には、以下のような理由です。
それぞれの理由について解説していきます。
3K(きつい・汚い・危険)のイメージが根強い
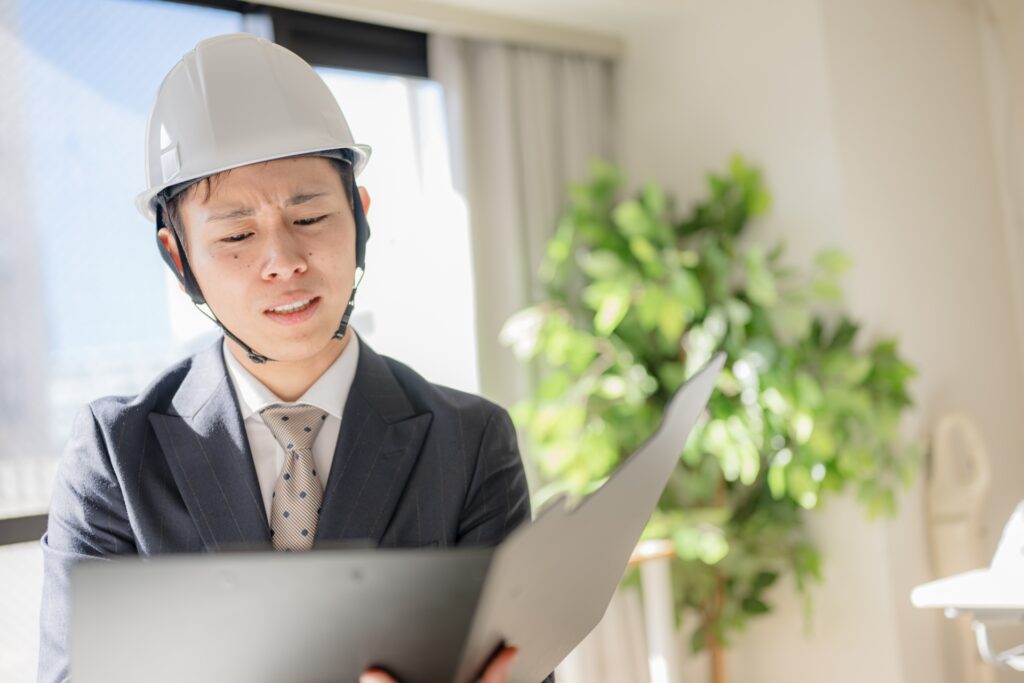
製造業界は長年にわたり、3K(きつい・汚い・危険)というイメージを払拭できずにいます。この印象は、就職活動中の若者やその保護者の意思決定にも影響を与え、応募数の減少や離職率の高さにつながっています。
現場では体力を要する作業や、油や粉塵を扱う業務も少なくありません。また、高温・高湿環境、重機による事故リスクなどもあるため、他業界と比較して「安心して働ける職場」として選ばれにくいのが現状です。
一方で、実際には機械化や自動化が進み、作業負担の軽減が実現している現場も増えています。しかし、その事実が十分に発信されておらず、ネガティブな先入観だけが残っているのです。
技能伝承・教育が行われていない
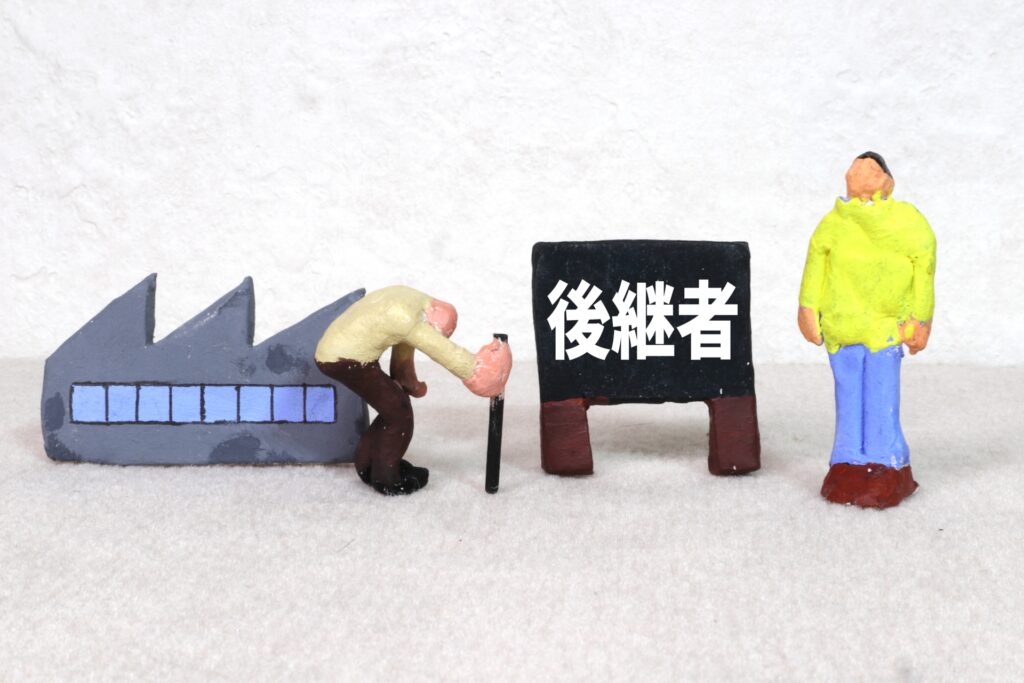
熟練作業者の退職が進む一方で、次世代への技能伝承が進んでいない現場も多く見受けられます。すると、特定の作業が限られた人に依存してしまい、生産性の大幅な低下や品質のばらつきにつながるケースも少なくありません。
この背景には、教育制度の整備不足やマニュアル化の遅れが挙げられます。新人が現場で即戦力となるには、計画的な育成カリキュラムとOJTの体系化が不可欠です。
しかし実際には「見て覚える」「慣れで対応する」といった非構造的な指導が主流となっており、技能の継承が属人化しています。加えて、ITやデジタル技術を活用した教育支援ツールの導入も遅れており、若手が成長を実感しづらい環境が続いています。
労働環境が更新されていない
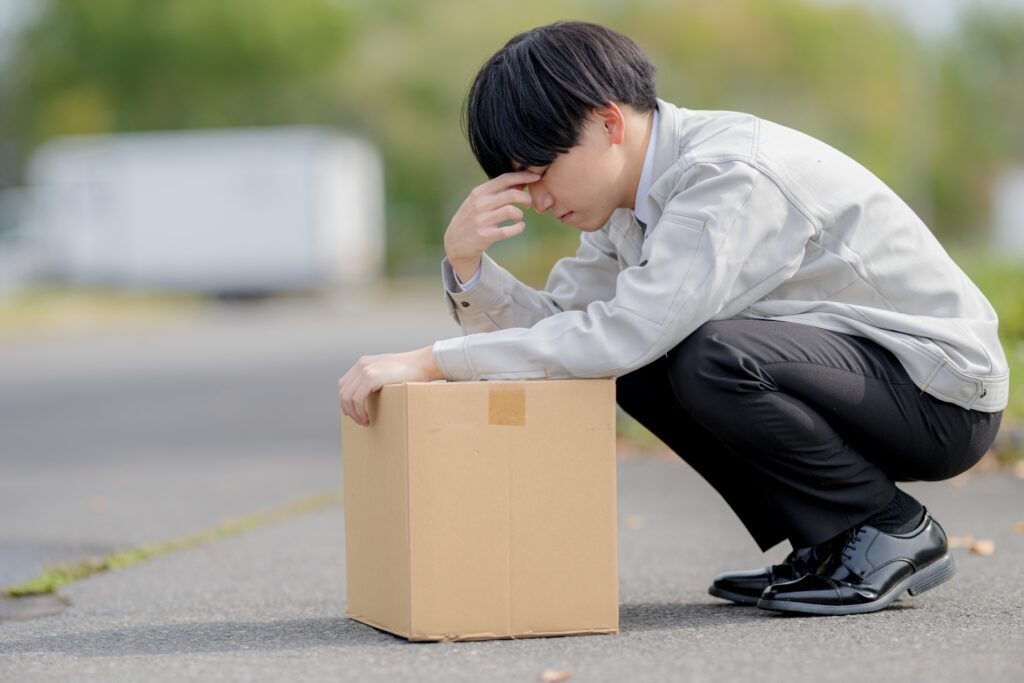
製造現場では、労働環境そのものの古さが人材確保を妨げる要因としてあります。労働環境の快適性や柔軟性は職場選びの重要な基準ですが、製造業ではその期待に応えきれていないケースが目立ちます。
長時間労働や休日出勤が常態化している職場では、ライフワークバランスを重視する世代に敬遠されがちです。また、空調の整備が不十分な工場や、作業スペースが狭く整備されていない現場では、快適な就労環境とは言えません。
こうした職場環境は、従業員の満足度や定着率にも大きく影響します。また、テレワークやフレックスタイムといった柔軟な働き方が広がるなか、製造業では導入が困難とされ、他業界との労働条件のギャップが拡大しています。
人手不足が製造現場にもたらす悪影響
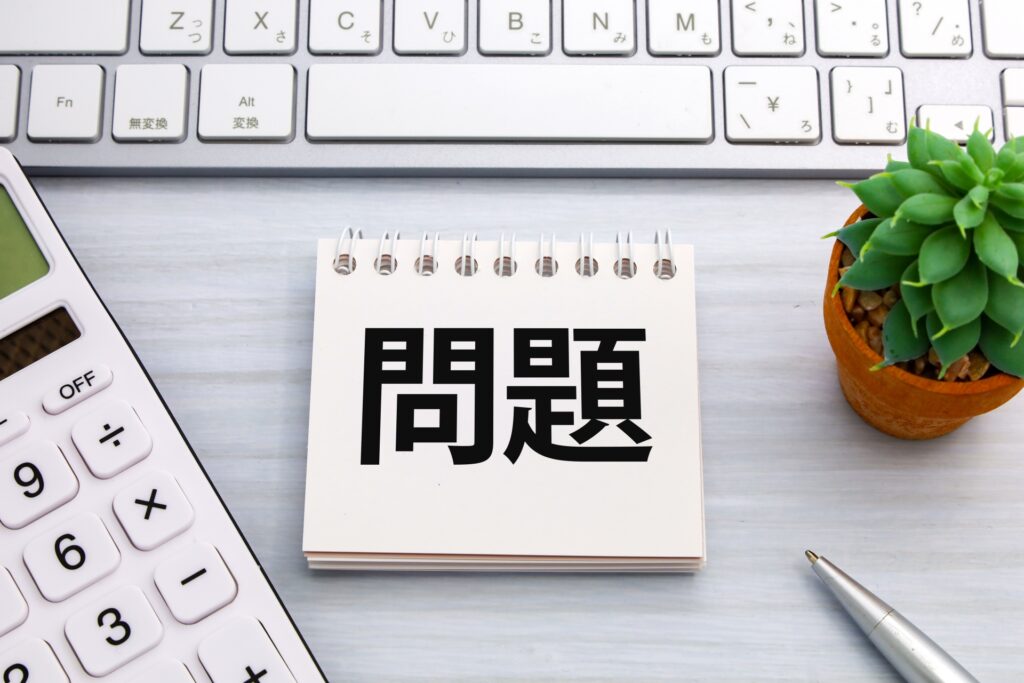
製造現場における人手不足は、単なる業務の遅れにとどまらず、現場全体の運営や経営基盤に深刻な影響を及ぼします。現場の中核を担う作業員が不足すると、生産効率の低下だけでなく、品質管理や納期遵守も困難です。
人手不足がもたらす悪影響としては、以下の5つが想定されます。
それぞれの悪影響について解説していきます。
生産性の低下
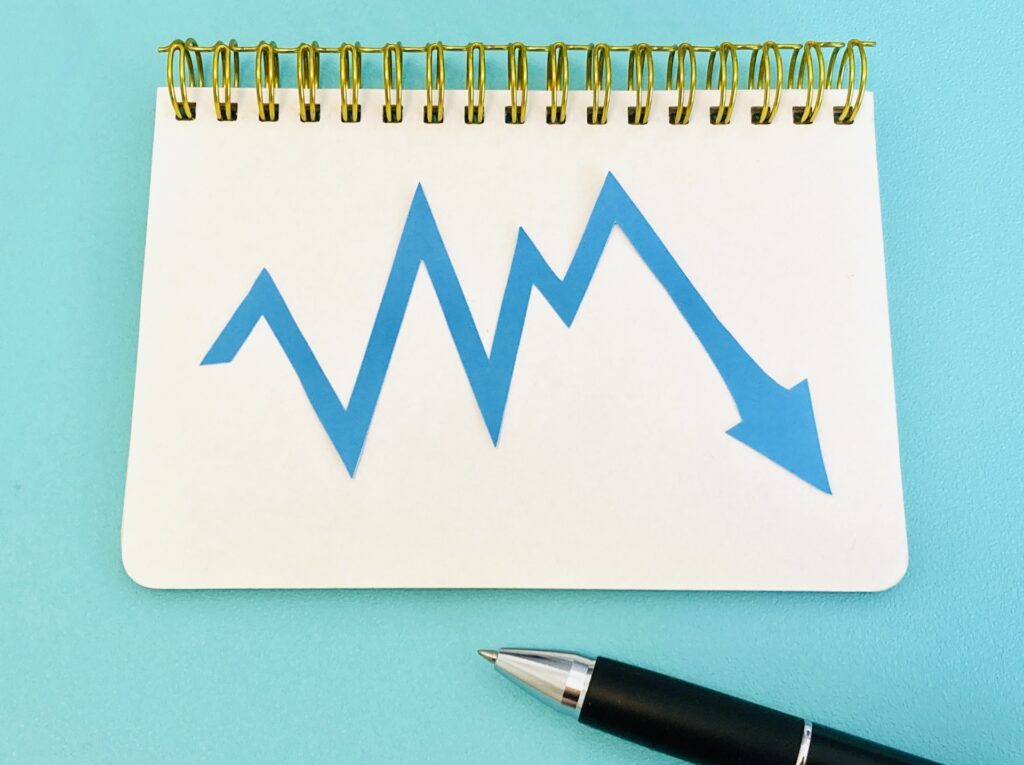
人手が足りない現場では、作業の効率が著しく低下します。本来、複数人で分担するべき作業を少人数で対応することで、手戻りや段取り替えの頻度が増え、生産性が著しく落ちてしまいます。
さらに、短納期の案件が増える中で、無理なスケジュールを組まざるを得なくなり、工程全体の最適化が困難です。このような状況が続けば、機械の稼働率にも影響を与え、設備の遊休時間が増加します。
また、作業時間あたりのアウトプットが減少するため、同じコストをかけても利益率が低下する構造に陥ります。
品質の不安定化
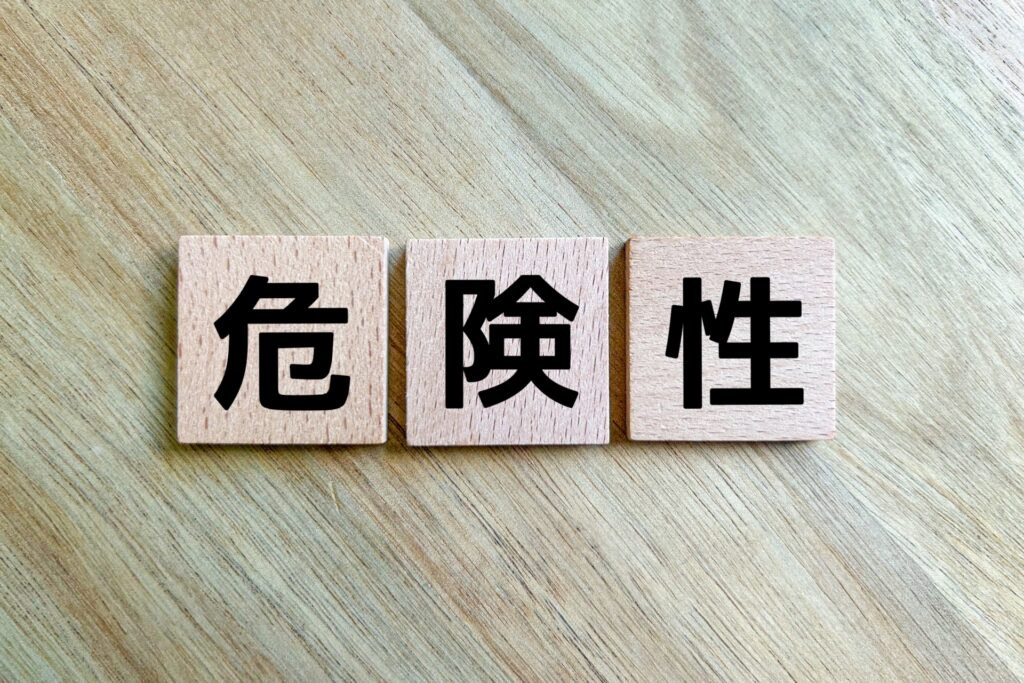
作業者の熟練度や経験に依存する工程が多い製造現場では、人員が不足すると品質の安定が難しくなるのが一般的です。新たに採用した人材が十分に育成されていないまま業務に就くことが多く、ミスや不良品の発生率が上昇する傾向にあります。
また、現場の人員が不足すると、工程ごとのダブルチェックや検査業務も省略されがちです。これにより、最終製品にばらつきが出たり、顧客からのクレームが増加したりと、企業の信用にも悪影響を及ぼします。
品質のばらつきが続くと、納品先との取引継続が難しくなる場合もあり、長期的な損失を招くリスクがあります。
作業員への負荷増大
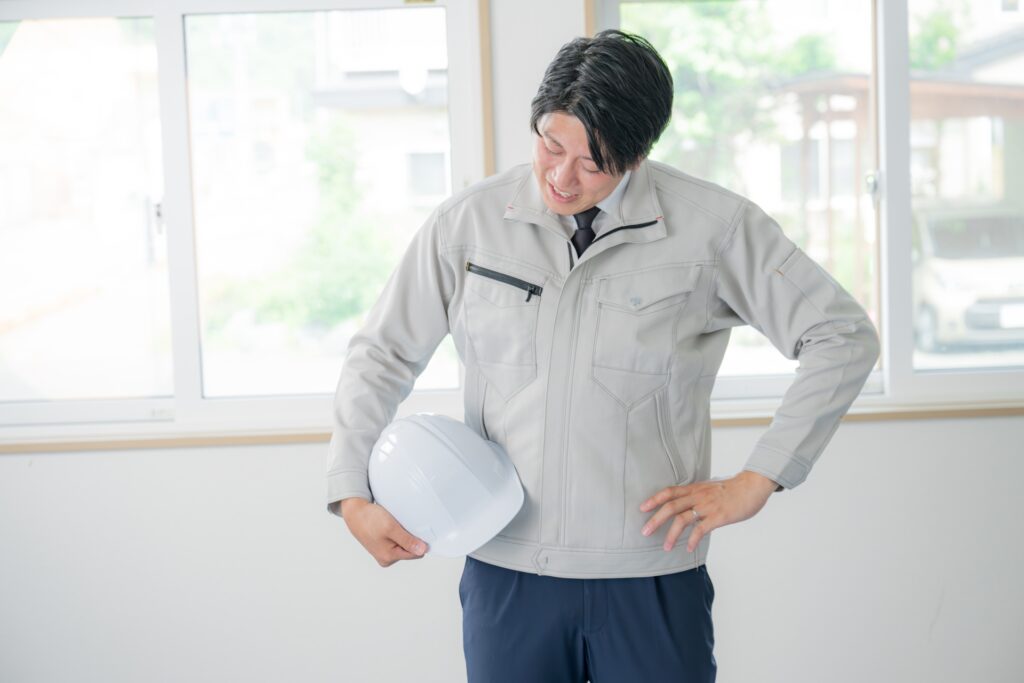
人手が足りない状況では、残された従業員の業務負荷が大きくなります。残業や休日出勤が常態化することで、従業員の疲労が蓄積され、集中力の低下や事故のリスクも高まります。
特に高齢の作業員が多い職場では、体力的な負担が深刻化しやすく、健康障害を引き起こす可能性も否定できません。結果として、さらなる離職者を生み出す原因となり、慢性的な人手不足のスパイラルが発生します。
このような負荷増大は、労働環境の悪化だけでなく、企業全体の士気低下にもつながります。
設備投資・自動化が遅れる
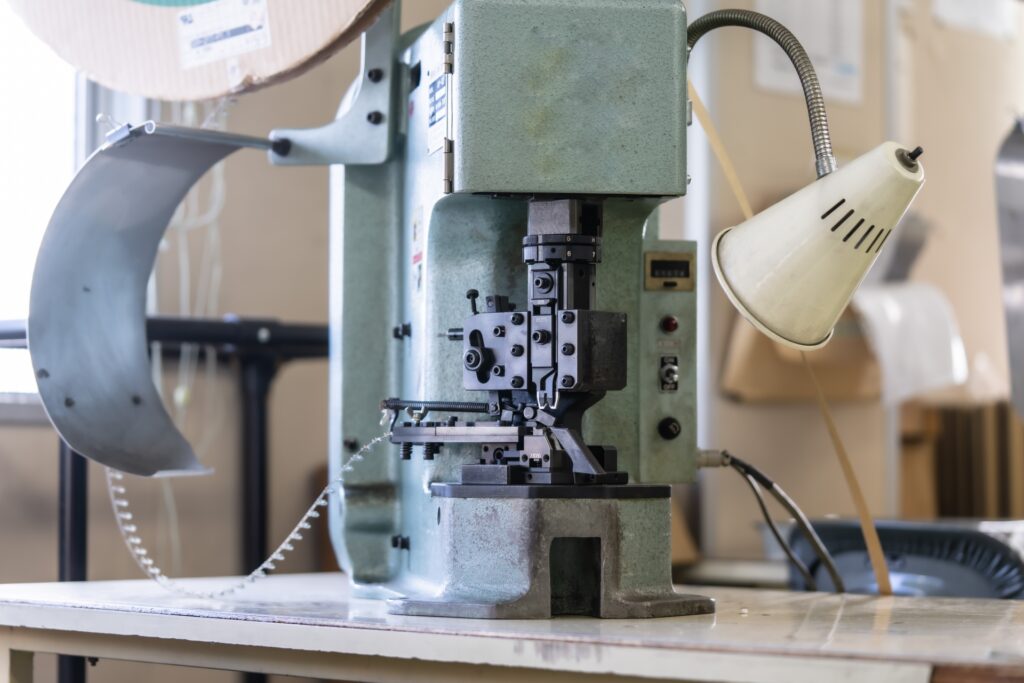
慢性的な人手不足が続く現場では、本来進めるべき設備投資や自動化の取り組みが後回しになりがちです。これは人員の確保や日々の業務で手一杯となり、長期的な視点での改善や予算確保が難しくなるのが原因として挙げられます。
また、現場にノウハウを持った人材が少ないと、新技術や新設備の導入に対する抵抗感も強くなります。その結果、他社と比べて自動化の進展が遅れ、競争力の低下を招く恐れがあります。
自動化やデジタル化は、将来的に人手不足を緩和する有効な手段であるにもかかわらず、それを進める余裕がないという矛盾に陥ってしまうのです。
事業が立ち行かなくなる
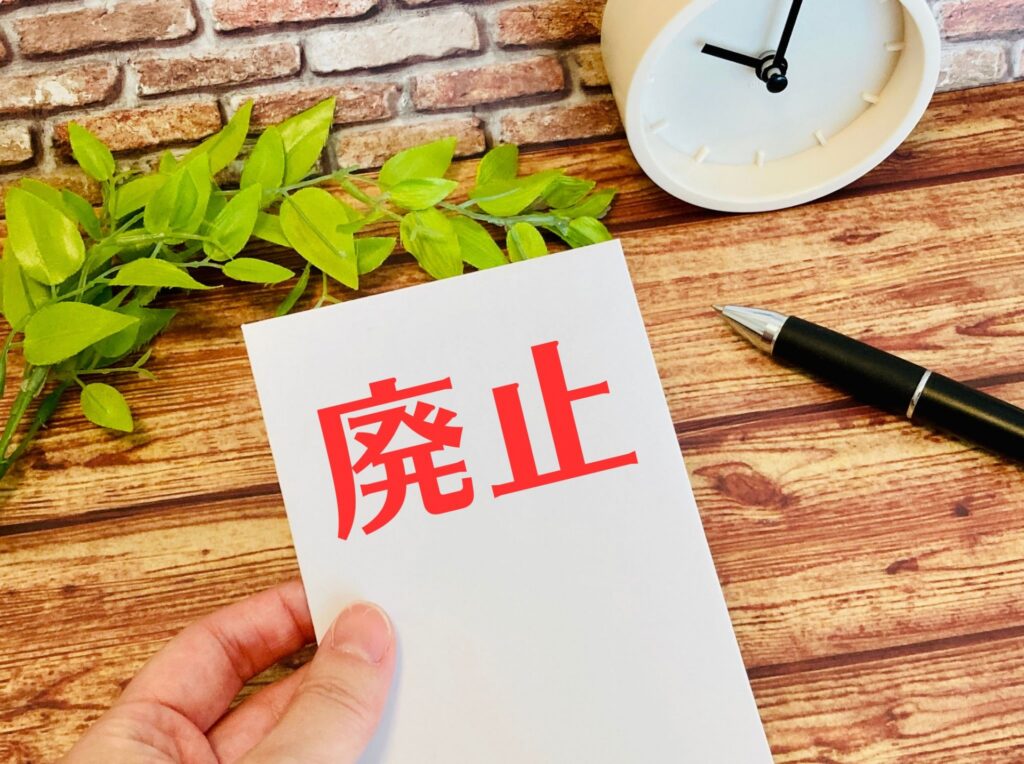
人手不足が長期間にわたって解消されない場合、最終的には事業そのものの継続が危ぶまれる状況に陥る可能性があります。人材が定着せず、納期遅延や品質トラブルが頻発するようになると、顧客からの信頼を失い、取引が打ち切られるリスクも懸念されます。
また、既存の従業員が離職してしまうと、事業継続に必要な工程を維持するのは困難です。最悪の場合、生産停止に追い込まれるケースもあります。
特に中小企業では、人材に余裕を持たせる余地が少ないため、ひとりの離脱が事業全体に与える影響が極めて大きくなります。
人手不足は多くの業界で蔓延している
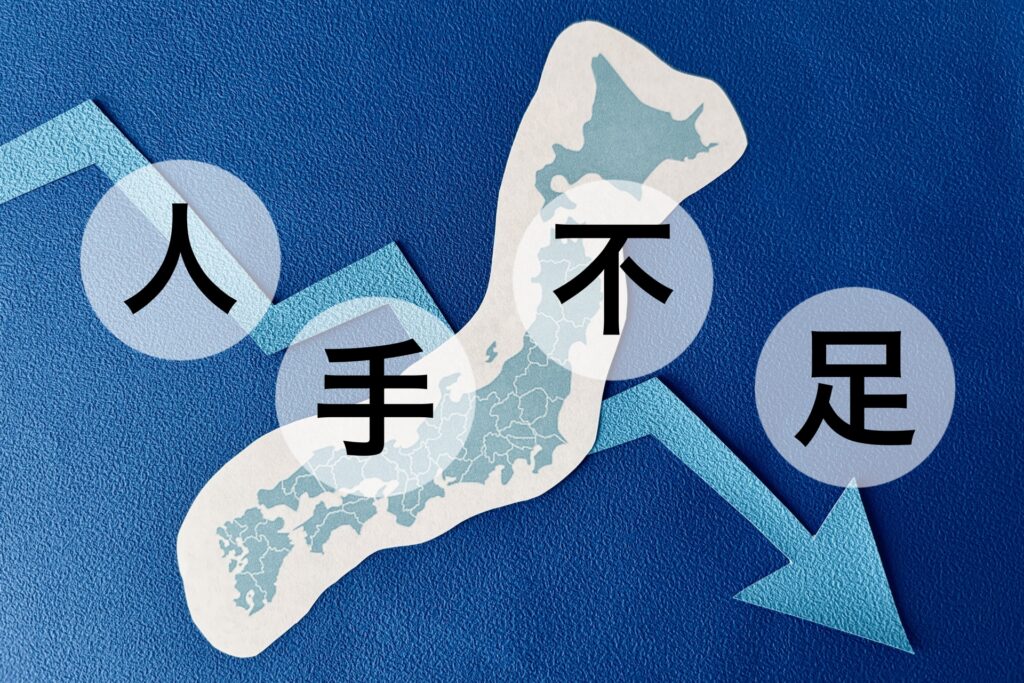
人手不足の問題は、製造業界に限らず、現在の日本社会全体で深刻な課題となっているのが現状です。総務省や厚生労働省の調査によれば、少子高齢化の進行によって生産年齢人口が減少を続けており、特に地方や中小企業において労働力の確保が難しくなっています。
加えて、働き方の多様化や若者の職業観の変化により、従来の労働集約型の産業では人材が集まりにくい傾向が強まっています。以下のような業種でも人手不足は深刻であり、それぞれの業界で業務の遅延やサービスの質の低下が進行しています。
- 建設
- 運輸
- 介護
- サービス業
製造業もその例外ではなく、他業界との人材獲得競争に晒されている状況です。結果として、待遇や職場環境など、総合的な魅力を持つ企業が人材を確保しやすくなり、そうでない企業は人手不足が加速するという二極化も進行しています。
このように、人手不足は業界全体の課題であり、製造業単体での対策だけでは根本的な解決には至りません。
製造現場における人手不足に対する解決策
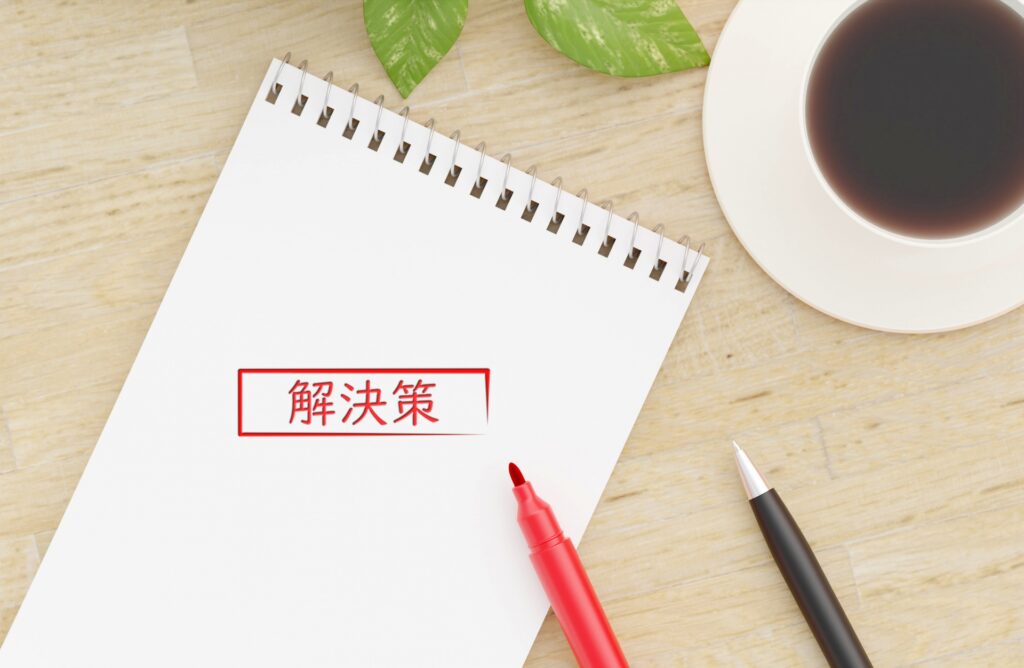
製造業における人手不足を解消するには、従来の採用強化だけでは限界があります。今後の生産体制を持続可能なものにするためには、現場の構造そのものを見直し、多様な人材の活用や業務プロセスの最適化が欠かせません。
具体的な解決策としては、以下の4つが有効です。
それぞれの解決策について解説していきます。
DX化による自動化・省人化の推進
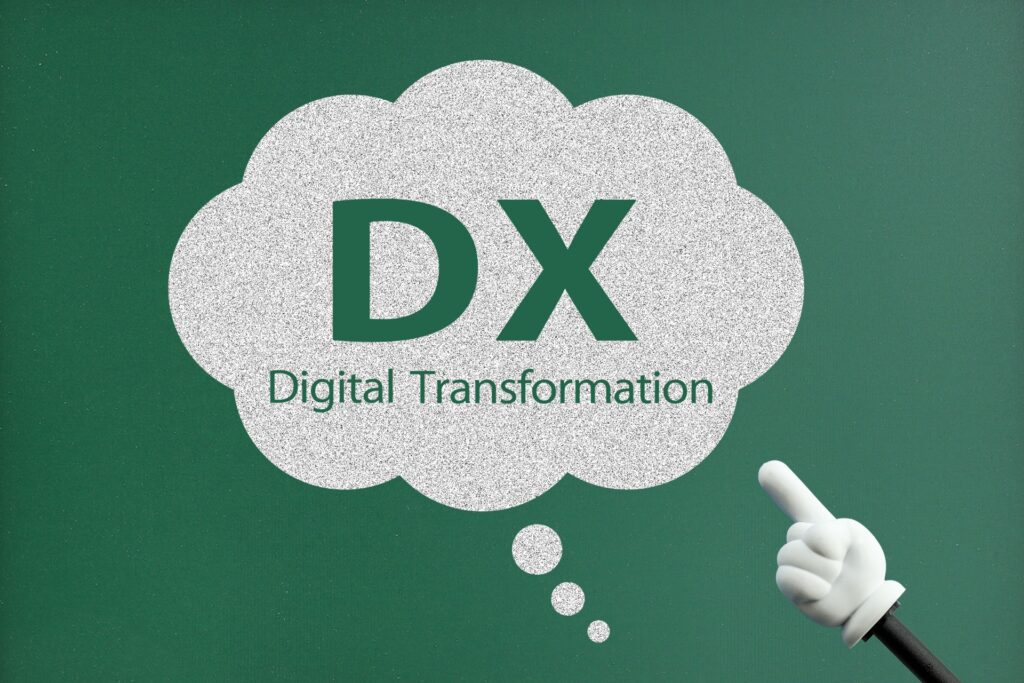
人手不足の根本的な解決には、業務そのものを見直すことが求められます。その中核を担うのが、DX(デジタルトランスフォーメーション)による自動化・省人化の推進です。
例えば、検査や計量といった定型作業は、AIやセンサーを活用することで人の手を介さずに処理することが可能です。計量機メーカーとしては、組み合わせはかりなどの導入によって、手作業の負担を軽減し、精度とスピードの両立を実現できます。
また、クラウド型の生産管理システムを活用すれば、作業進捗や人員配置の最適化も図れます。これにより、少人数でも安定した生産体制の維持も可能です。DX化は一朝一夕には進みませんが、段階的な導入と社内の意識改革を進めることで、確実に効果が現れます。
女性・高齢者・障がい者の積極採用
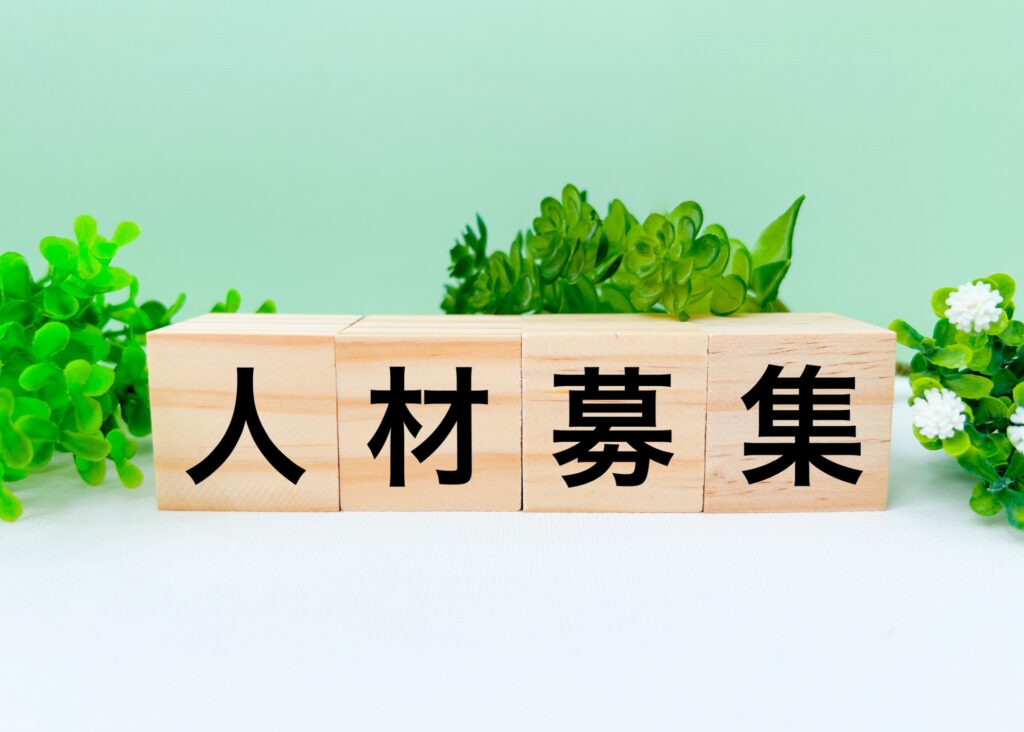
人材不足を補うためには、これまで十分に活用されてこなかった人材層に着目することが有効です。女性・高齢者・障がい者は、適切な環境整備や業務設計によって戦力として活躍してもらえます。
具体的には、以下のような配慮によって、女性や高齢者が働きやすい環境を整えることが可能です。
- 立ち作業を減らしたライン設計
- 力作業の軽減
- 休憩スペースの整備
また、障がい者についても、定型作業や検品業務など適性に応じた配置を行うことで、生産性の向上につなげることが可能です。これらの取り組みは、多様な人材を受け入れるだけでなく、職場の風土やコミュニケーションの活性化にも良い影響を与えます。
標準作業書や動画マニュアルによる教育の平準化
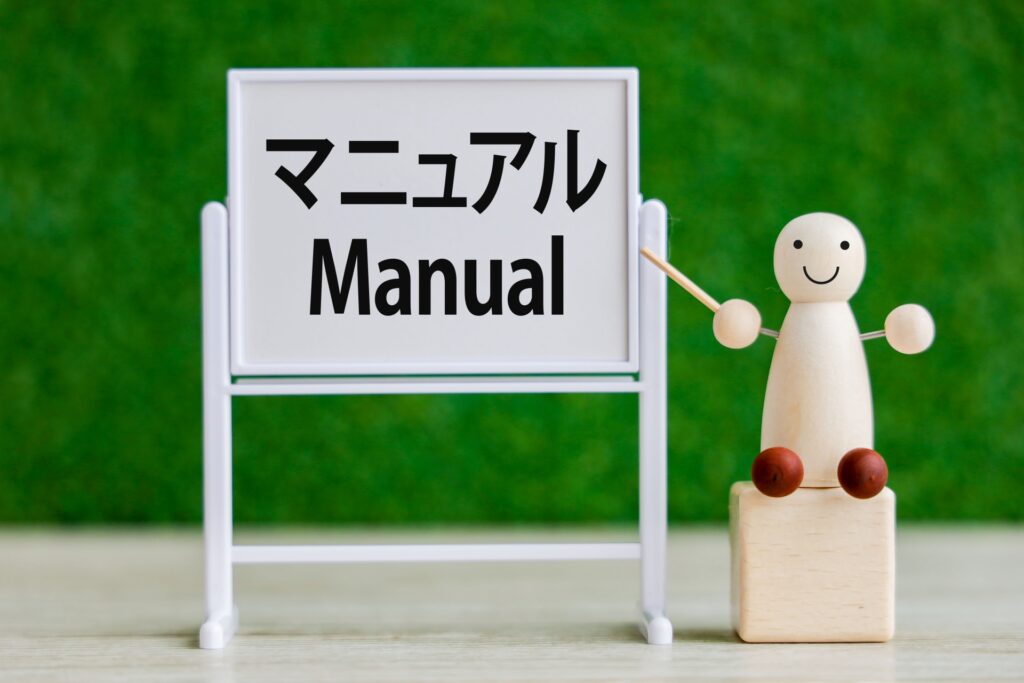
即戦力となる人材が限られている中で、人手不足を補うためには、教育の効率化と平準化が欠かせません。現場の技能やノウハウを属人化させず、誰でも一定の品質で作業できるようにするためのツールが、標準作業書や動画マニュアルです。
作業手順を明文化したマニュアルや、実際の作業を収録した動画教材を用いることで、新人でも短期間で基本作業を習得できます。視覚情報を活用することで、言語や理解度の差を超えてスムーズな習得が可能です。
また、教育担当者の負担を軽減しつつ、複数拠点での一貫した教育が可能になるため、大規模な製造現場でも効果的です。業務の品質安定化と教育コストの削減を同時に実現できる点でも、導入価値の高い施策といえるでしょう。
時短・フレックスなどの働き方の導入
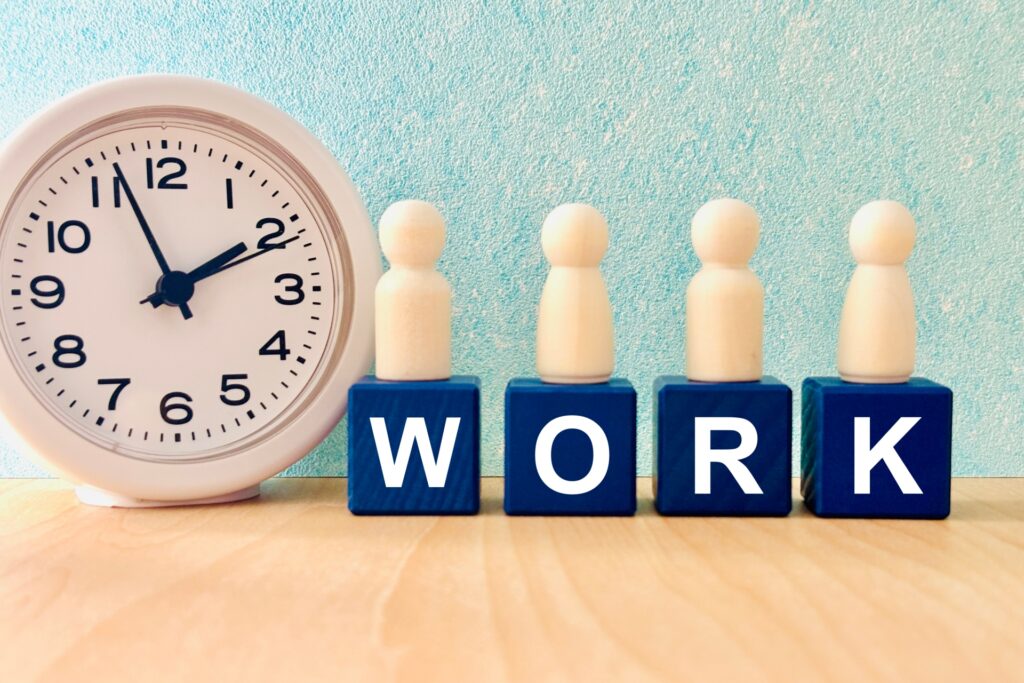
人手不足の解消には、働きやすい環境づくりも重要です。近年では、時短勤務やフレックスタイム制など、柔軟な働き方へのニーズが高まっており、製造現場でも導入が進みつつあります。
育児や介護と両立しやすい時短勤務制度を導入すれば、離職防止と人材の継続雇用につながります。フレックスタイム制を導入すれば、通勤負担の軽減やライフスタイルに応じた就労が可能になり、職場への満足度向上も期待できるでしょう。
製造業は「時間と場所が固定された職場」というイメージが強いですが、工程ごとの見直しやタスク分担の工夫によって柔軟な働き方を取り入れることは十分可能です。
製造現場における計量工程を省人化する方法
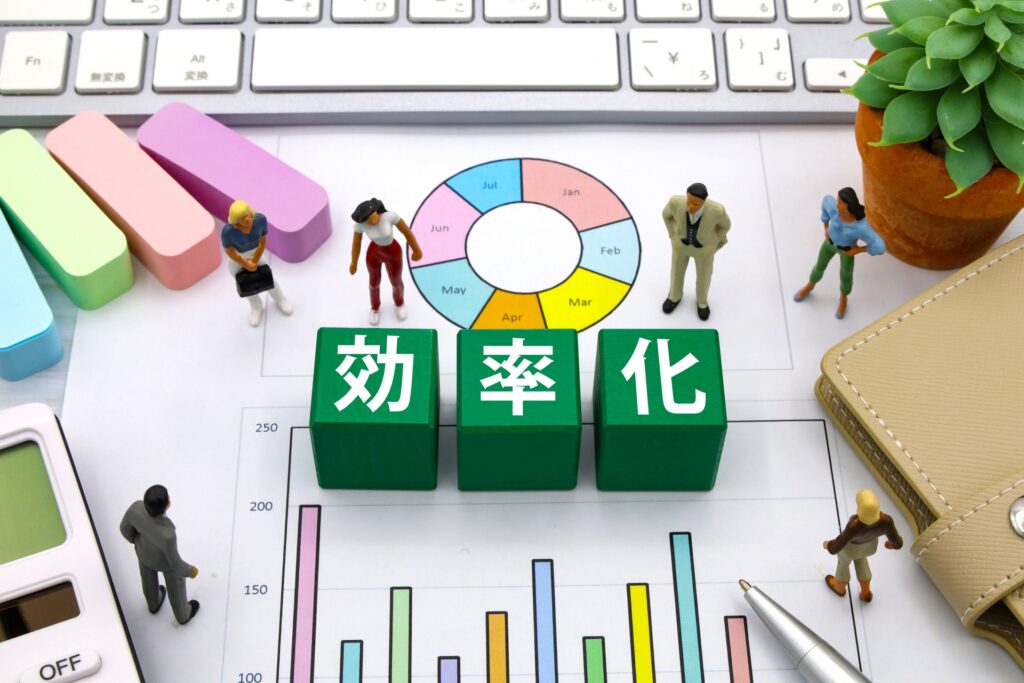
製造現場にける計量工程では、作業時間のばらつきやヒューマンエラーのリスクが伴います。そのため、省人化と自動化を実現するための設備導入が急務です。特に注目されているのが、以下のようなアプローチ手法です。
それぞれの方法について解説していきます。
全自動組み合わせはかりを導入する
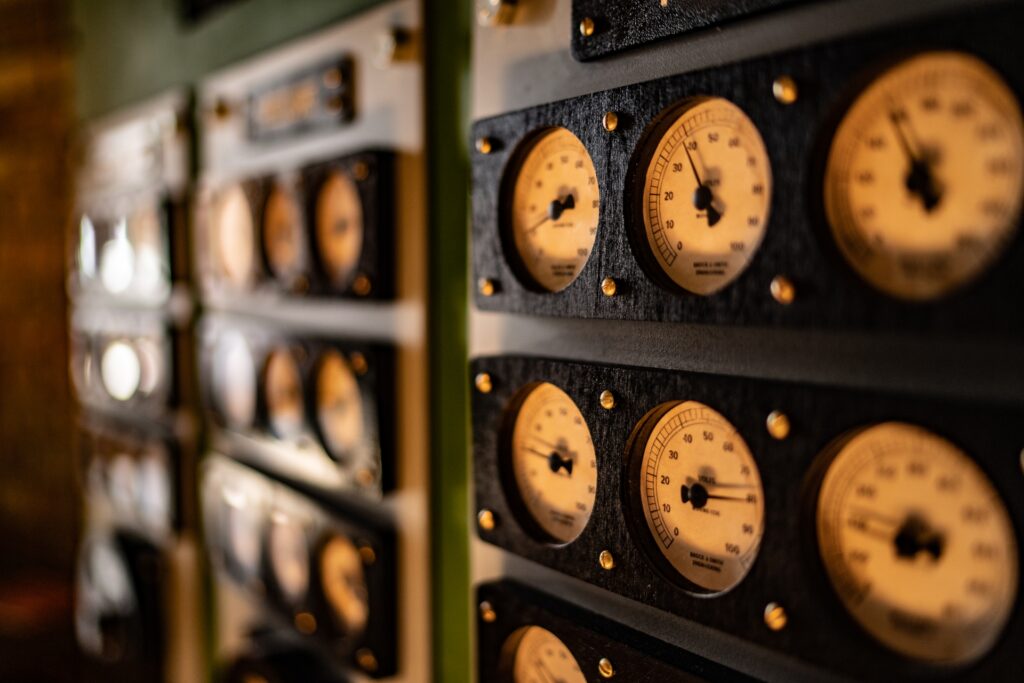
計量工程の省人化において、最も即効性が高いのが全自動組み合わせはかりです。全自動組み合わせはかりは複数の計量ユニットを組み合わせて、目標値に最も近い重量を高速で自動的に計算・排出します。
従来の手作業による計量では、精度の確保とスピードの両立が難しく、作業者の経験に依存しやすい課題がありました。しかし、全自動組み合わせはかりを用いることで、1回あたりの計量が数秒以内で完了し、かつ精度誤差も最小限に抑えることが可能です。
このシステムは、一度設定すれば連続的に稼働できるため、人員を割く必要がなくなり、作業者はより高度な工程や品質管理に集中できるようになります。
協働ロボットとの連携
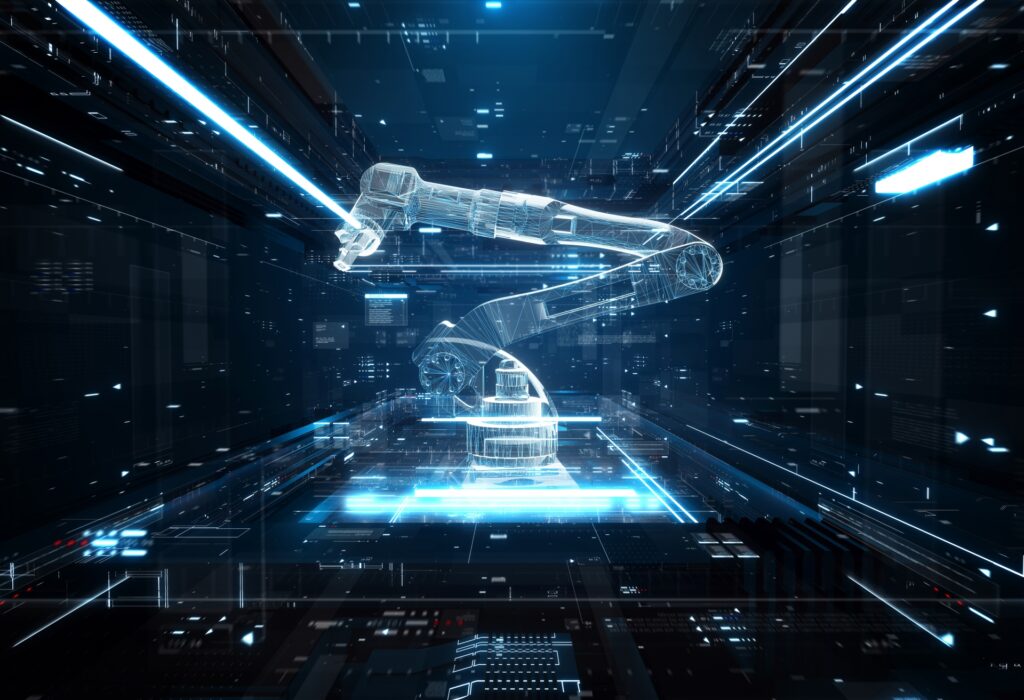
全自動組み合わせはかりと相性が良いのが、協働ロボットとの連携です。協働ロボットは人と同じ空間で作業できる安全設計のロボットで、柔軟な動作と高精度な作業が可能です。
計量済みの製品を次工程に受け渡したり、梱包機へ配置したりする作業を自動化することで、省人化と作業の均一化を実現します。また、導入・設定が比較的簡単で、既存の設備と柔軟に組み合わせられる点も特徴です。
結果として、ライン全体の省人化が促進され、従業員の負担軽減と生産性向上の両立が図れます。
バーコード・RFIDによる材料認識の自動化
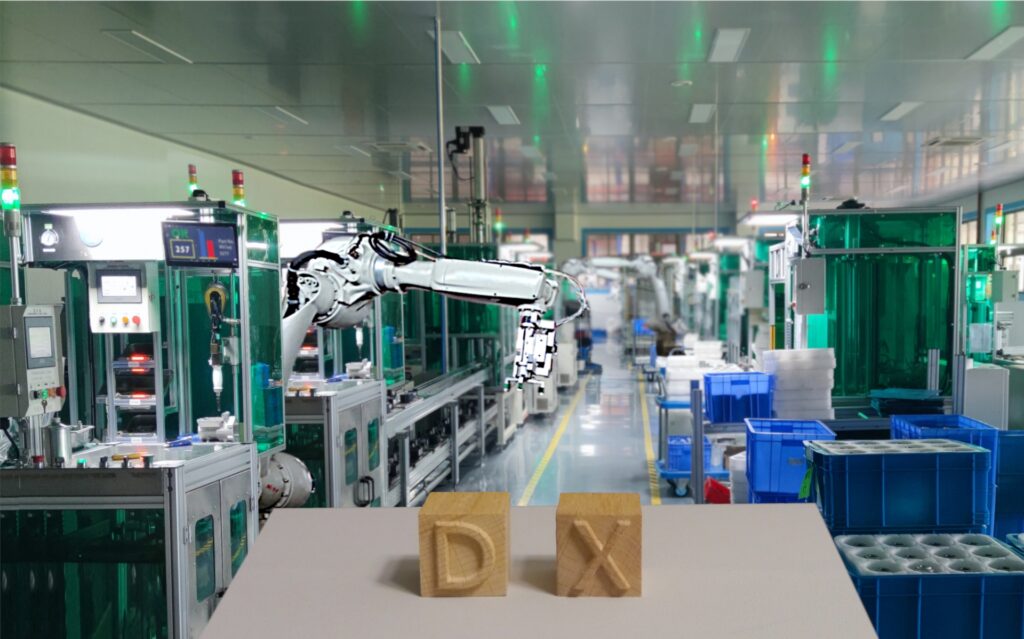
材料の識別や計量前の準備作業も、人手不足を補うための自動化対象です。特に有効なのが、バーコードやRFID(無線ICタグ)を活用した材料認識の自動化です。
これらの技術を活用することで、資材の種類・ロット番号・数量といった情報を瞬時に読み取り、システム上で自動処理することが可能になります。RFIDやバーコードを利用すれば、非接触・高速での情報取得が可能になり、工程の効率化と品質保証が同時に進められます。
また、全自動組み合わせはかりや搬送ロボットと連動させることで、材料の投入から計量、出荷までの一連の流れを自動化することが可能です。これにより、作業者の負担を減らしながら、正確な在庫管理と工程管理が実現します。
搬送工程をAMR(自律搬送ロボット)で自動化
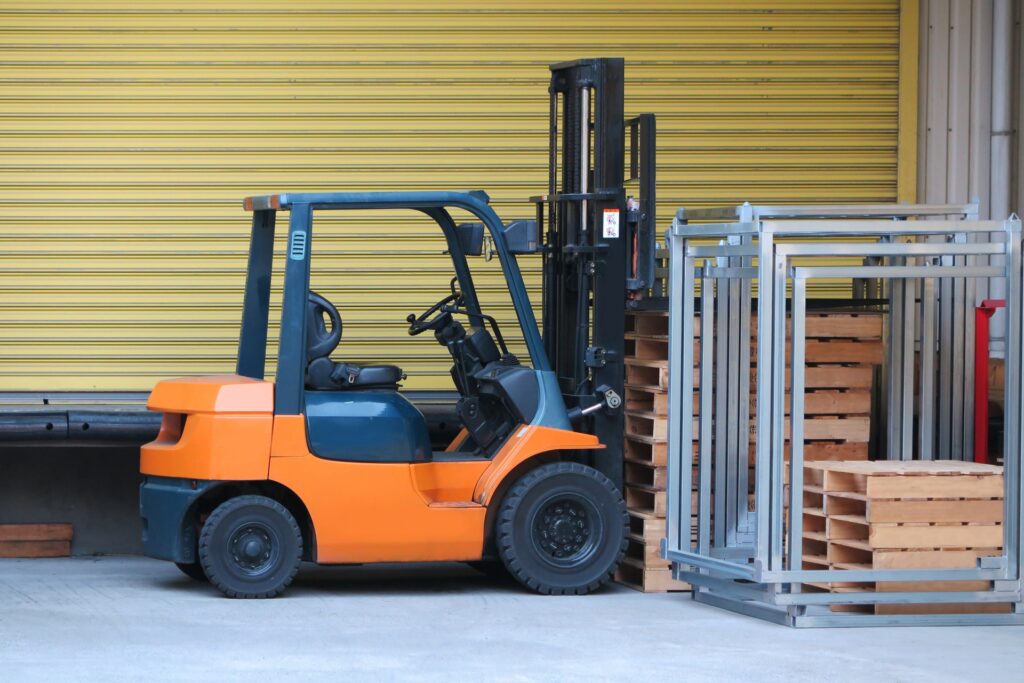
工場内での資材や計量済み製品の搬送負担を解消する有効な手段が、AMR(Autonomous Mobile Robot)の導入です。AMRは、事前にルートを固定することなく、現場の状況に応じて最適なルートを自律的に判断・走行します。
これにより、工程間の搬送作業が完全に自動化され、人手を割く必要がなくなります。AMRはセンサーやマップ認識機能を備えており、障害物を避けながら安全に移動できるため、人的リスクの低減にも期待できるでしょう。
また、工場内のデジタル管理システムと連携すれば、材料供給や完成品の出荷指示なども自動化され、スムーズなライン運用が可能です。
おすすめの全自動組み合わせはかりメーカー3選
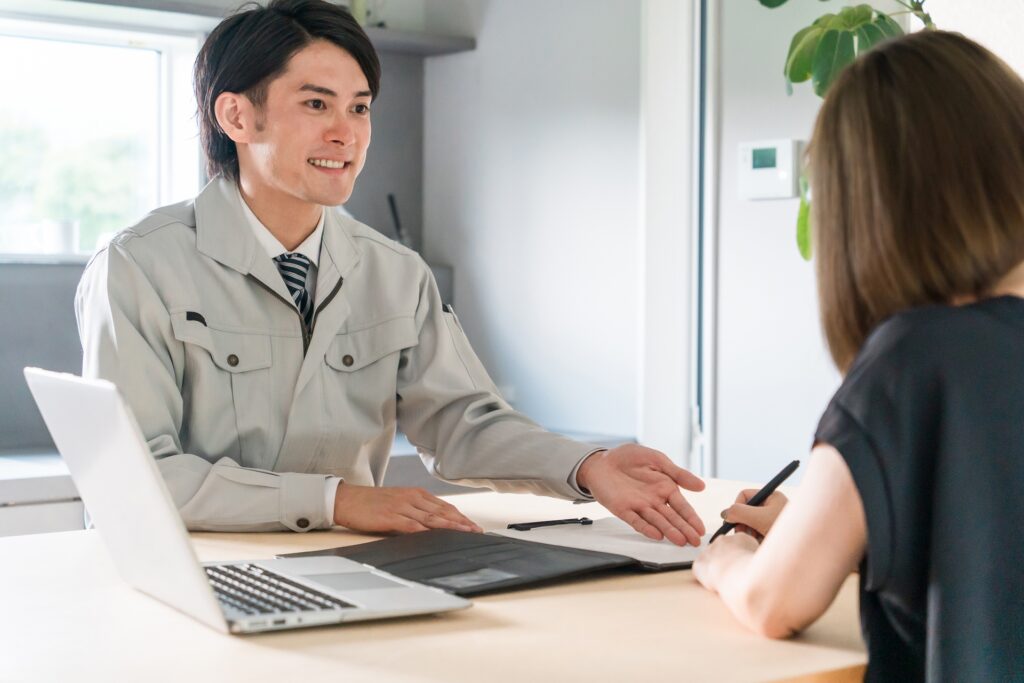
以下では、全自動組み合わせはかりの導入を検討している担当者向けに、信頼性と実績のある国内メーカーを3社厳選してご紹介します。
それぞれの特徴を比較しながら、自社に最適な選択を進めてください。
大和製衡株式会社
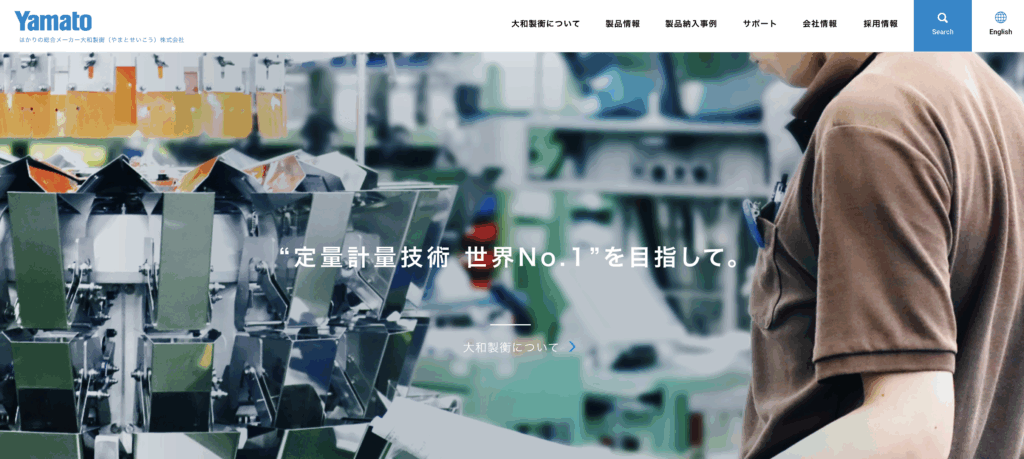
大和製衡株式会社は、国内外で高い評価を受ける老舗のはかりメーカーであり、全自動組み合わせはかりの分野でも豊富な実績を持ちます。
項目 | 詳細 |
会社名 | 大和製衡株式会社 |
住所 | 〒673-8688(〒673-0849) 兵庫県明石市茶園場町5番22号 |
電話番号 | 078-918-5526 |
公式HP | https://www.yamato-scale.co.jp/ |
食品や医薬品の計量をはじめ、農産物、工業部品まで多様な業界に対応したモデルを展開しており、その汎用性と安定性の高さが強みです。
同社の製品は、精密な重量制御技術と独自のソフトウェアによって、計量精度とスピードのバランスに優れています。また、製造ラインに合わせたカスタマイズが可能で、設置後の運用効率も高く評価されています。
さらに、アフターサービスやメンテナンス対応も手厚く、導入後のトラブルにも迅速に対応してくれる点も安心です。国内工場での導入事例も多いため、品質管理が厳しい業種でも安心して導入できます。
全自動組み合わせはかりの導入をお考えの方は、一度の大和製衡株式会社ホームページを訪れてはいかがでしょうか。
以下の記事では、大和製衡株式会社の特徴や口コミ、導入事例などをさらに詳しく解説していますので、気になる方はぜひ一度チェックしてみてください。
株式会社イシダ
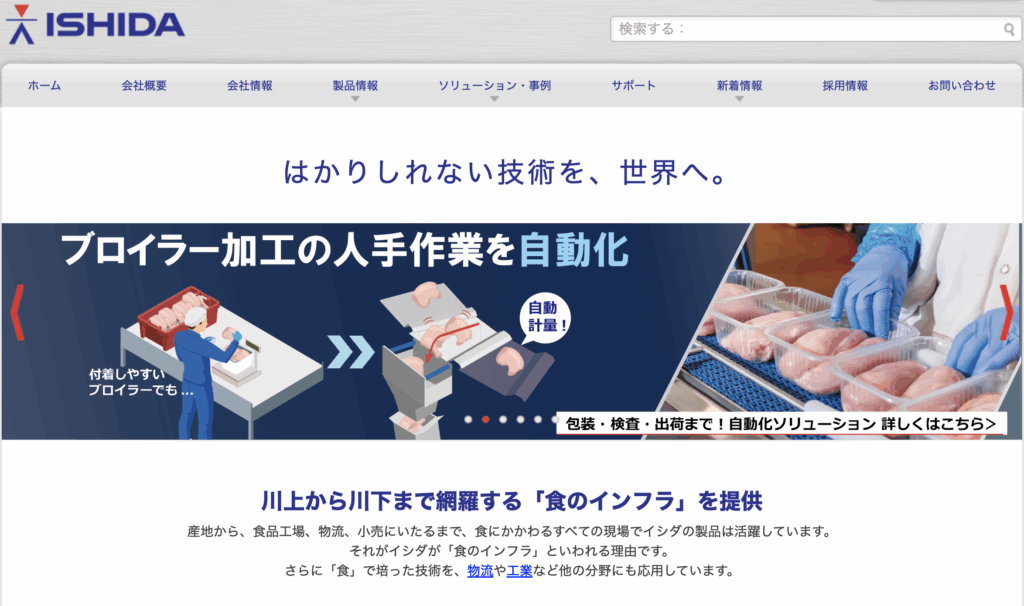
株式会社イシダは、組み合わせはかりのパイオニアとして世界的にも知られており、国内市場においてもトップクラスのシェアを誇ります。
項目 | 詳細 |
会社名 | 株式会社イシダ |
住所 | 〒606-8392 京都市左京区聖護院山王町44番地 |
電話番号 | 075-771-4141 |
公式HP | https://www.ishida.co.jp/ww/jp/ |
イシダ製の組み合わせはかりは、独自開発のセンサー技術により、わずかな重量差も正確に検知します。また、直感的な操作が可能なタッチパネルや多言語対応など、現場での使いやすさにも配慮されています。
さらに同社は、包装機や検査装置との一体化にも強みを持っており、ライン全体の自動化を視野に入れたソリューションを提案できる点が特徴です。業種や生産規模を問わず、長期的な投資対効果を見込める製品群を揃えています。
以下の記事では株式会社イシダの評判や特徴について紹介しているので、ぜひ参考にしてください。
アンリツ株式会社
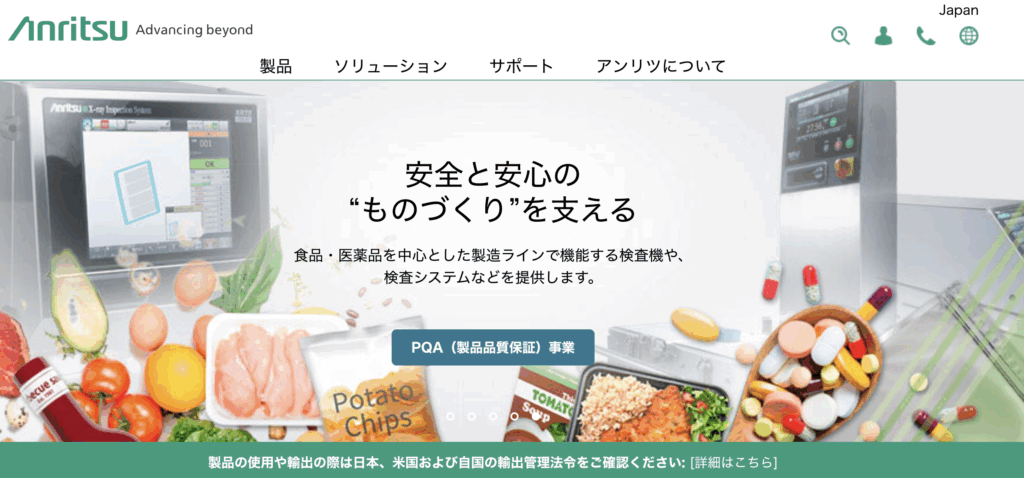
アンリツ株式会社は、もともと通信機器で高い信頼を得ている企業ですが、検査機器やはかり分野にも注力しており、近年は全自動組み合わせはかりの分野でも注目されています。衛生設計に優れた製品を多く展開しており、食品・医薬品業界から高い評価を得ています。
項目 | 詳細 |
会社名 | アンリツ株式会社 |
住所 | 〒243-8555神奈川県厚木市恩名5-1-1 |
電話番号 | 046-223-1111 |
公式HP | https://www.anritsu.com/ja-jp/ |
同社のはかりは、堅牢な構造とともに高い防塵・防水性能を備えており、厳しい現場環境にも対応可能です。また、データ管理やネットワーク対応機能も充実しており、トレーサビリティや製造記録の自動化を推進したい現場に最適です。
さらに、異物検出や金属検出機能を持つ製品との連携もスムーズで、品質管理の強化もサポートします。
以下の記事ではアンリツ株式会社の評判や特徴について紹介しているので、ぜひ参考にしてください。
まとめ
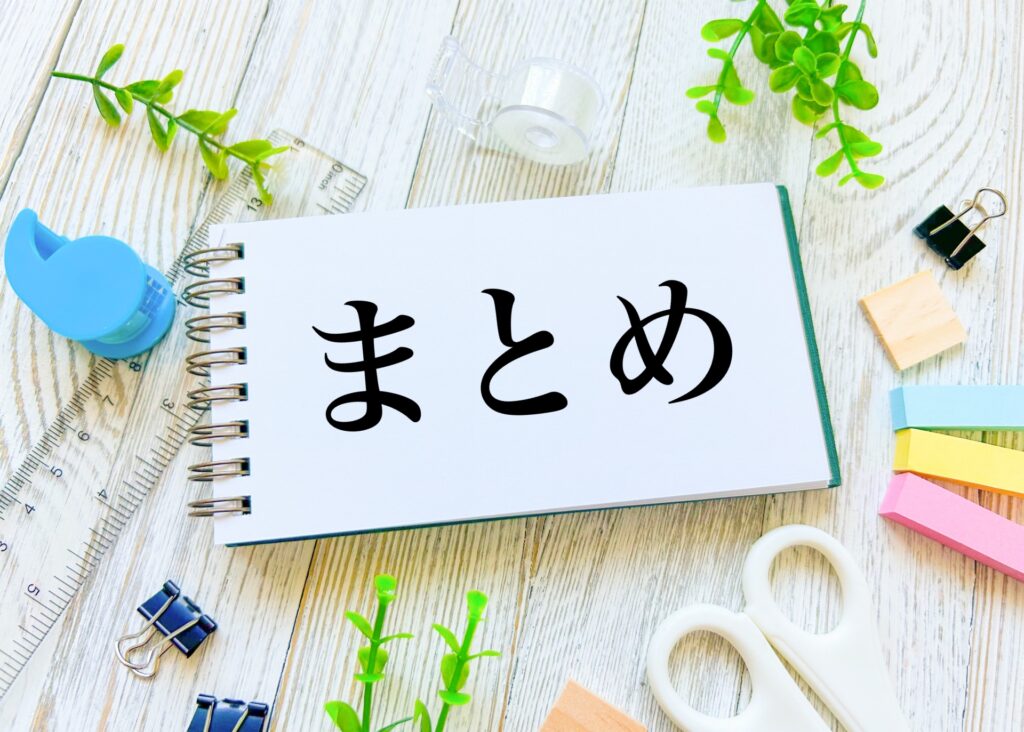
製造業界における人手不足は、構造的な課題として日本中で広がっています。生産性の低下や品質の不安定化といった現場のリスクを放置すれば、将来的には事業の継続すら脅かされかねません。
そのため、DXによる自動化をはじめ、多角的な取り組みが必要です。計量工程においては、全自動組み合わせはかりの導入やロボットとの連携によって、省人化と品質向上を同時に実現することが可能です。
人手不足に悩んでいる方は、自社に合った設備投資や運用改善に着手し、持続可能な生産体制を構築してください。