工程のムダや人手不足、ミスの多発といった問題が積み重なると、生産性の低下やコストの増大につながりかねません。しかし、現場の課題を正しく把握し、具体的な改善策を講じることで、大きな成果を得ることは十分に可能です。
本記事では、現場担当者の方が抱える「効率の悩み」に着目し、実際に活用できるテクニックやツールをご紹介します。適切な対策を講じることで、作業のムダが減り、品質の安定や納期の短縮といったメリットも期待できます。
製造現場の悩みを抱えている方は、ぜひ参考にしてみてください。
また、以下ではおすすめの組み合わせはかりメーカーについて紹介しているので、ぜひ参考にしてみてください。
製造現場の効率低下を招く5つの要因
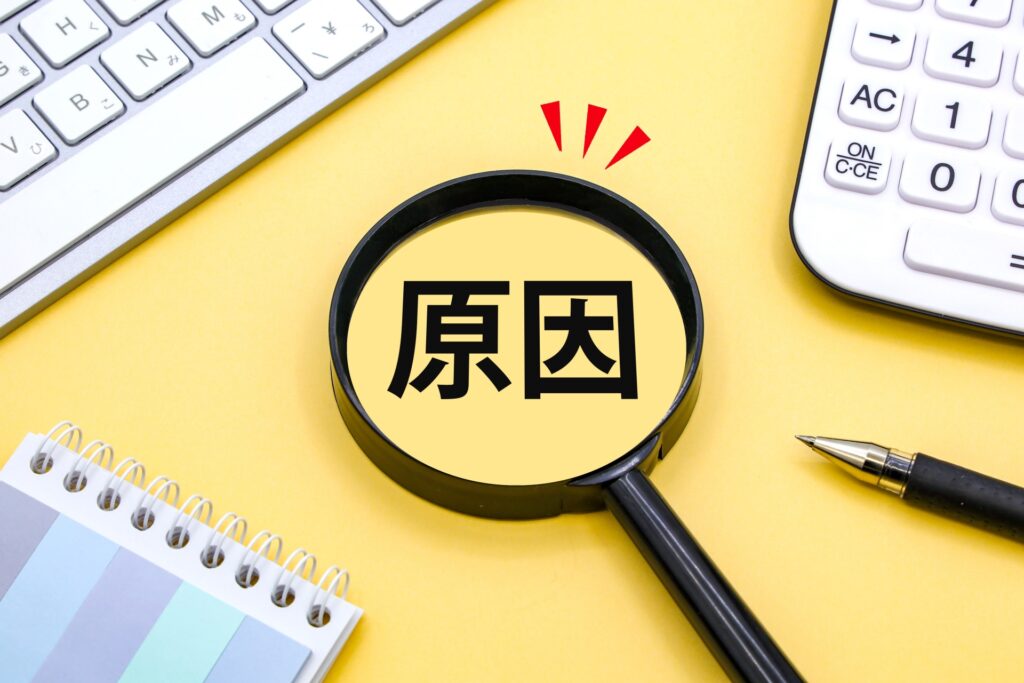
製造現場における効率の低下は、単一の問題ではなく、複数の要素が複雑に絡み合って発生することがほとんどです。具体的に挙げられるのが、以下の5つの要因です。
それぞれの要因について解説していきます。
作業工程に関する要因
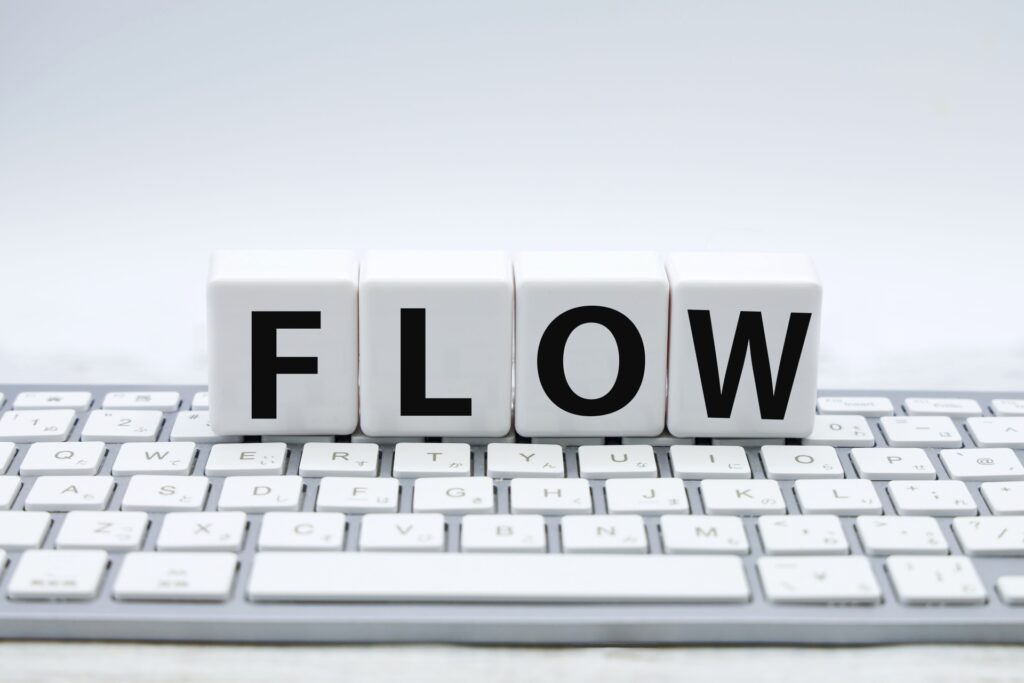
作業工程に関する非効率は、製造現場で最も頻繁に見受けられる課題です。例えば、工程ごとの役割や作業手順が標準化されていない場合、担当者によって作業時間や品質に差が生じやすくなります。
また、工程間の連携が悪いと、前工程の完了を待つ時間が増え、全体の生産スピードが落ちてしまいます。さらに、不要な動線や手戻りが発生するレイアウトも、効率を大きく損なう原因です。
そのため、現行の作業フローを可視化し、ボトルネックとなっている部分を明確にすることが重要です。工程のムリ・ムダ・ムラを見直し、作業の平準化やセル生産方式の導入などを検討することで、大幅な改善が期待できます。
設備・機械に関する要因
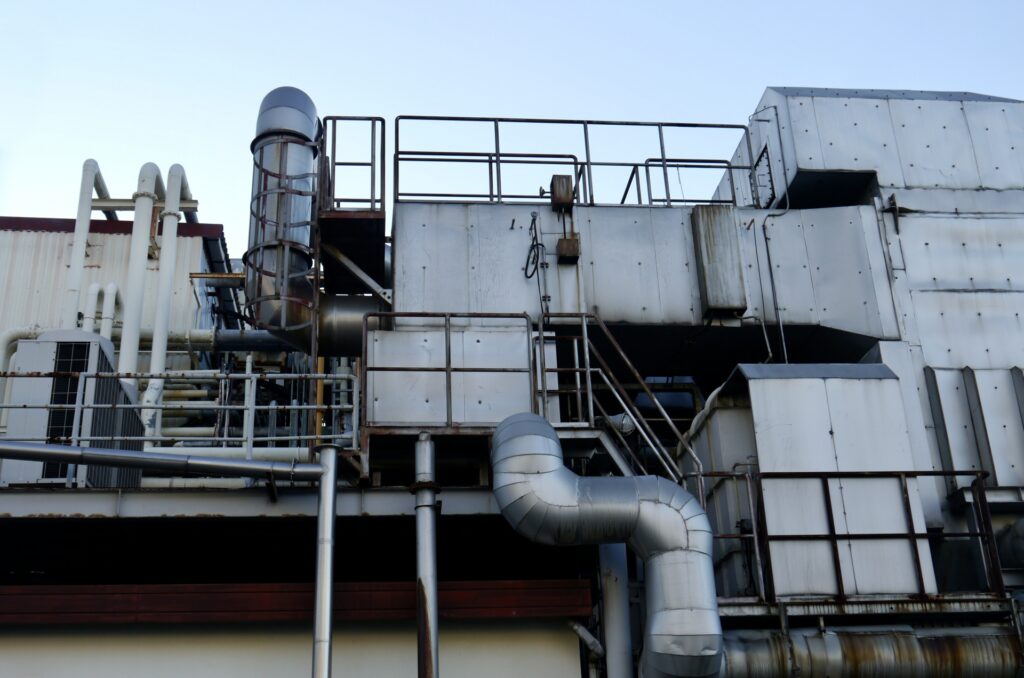
設備や機械の不具合や老朽化は、製造現場の効率低下に直結します。故障が頻発する機器は、修理や再稼働のたびにラインが止まり、生産計画に大きな影響を与えるからです。
また、メンテナンスが不十分な場合、機械の性能が低下し、加工精度や速度が落ちることもあります。さらに、現場で使われている設備が製品の多様化や少量多品種生産に対応していない場合、段取り替えにかかる時間が増加し、効率的な生産が難しくなります。
改善策としては、定期的な保守点検を徹底するとともに、IoTセンサーによる状態監視の導入などが有効です。また、省力化機器や自動化機器の導入を検討することで、機械の稼働率を高めることが可能です。
人材・労務に関する要因
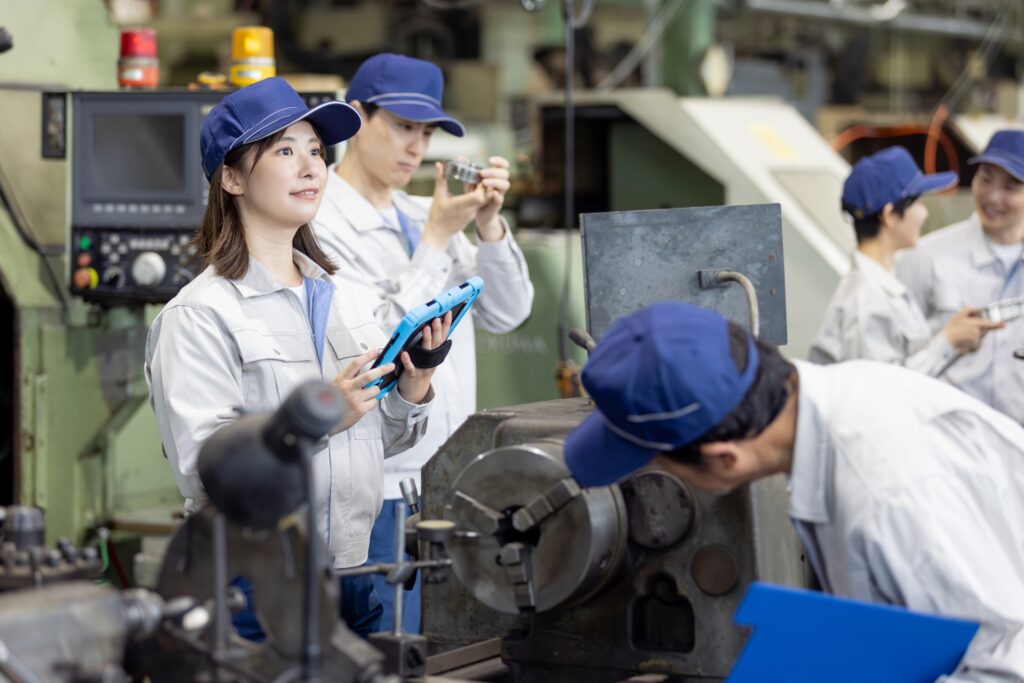
人材不足や労務管理の不備も、製造現場の効率低下を招く要因です。特に近年は、高齢化による技術継承の遅れや、若年層の入職者不足が深刻化しており、限られた人員で現場を回さなければならないケースが増えています。
作業者のスキル差が大きい現場では、工程ごとに作業品質が安定せず、全体のパフォーマンスが低下しがちです。
近年では、熟練作業者の技術を動画やARで可視化し、効率的に技術を伝える取り組みも広がっています。人を活かす仕組みを整えることで、組織全体の生産性が底上げされます。
資材・在庫に関する要因
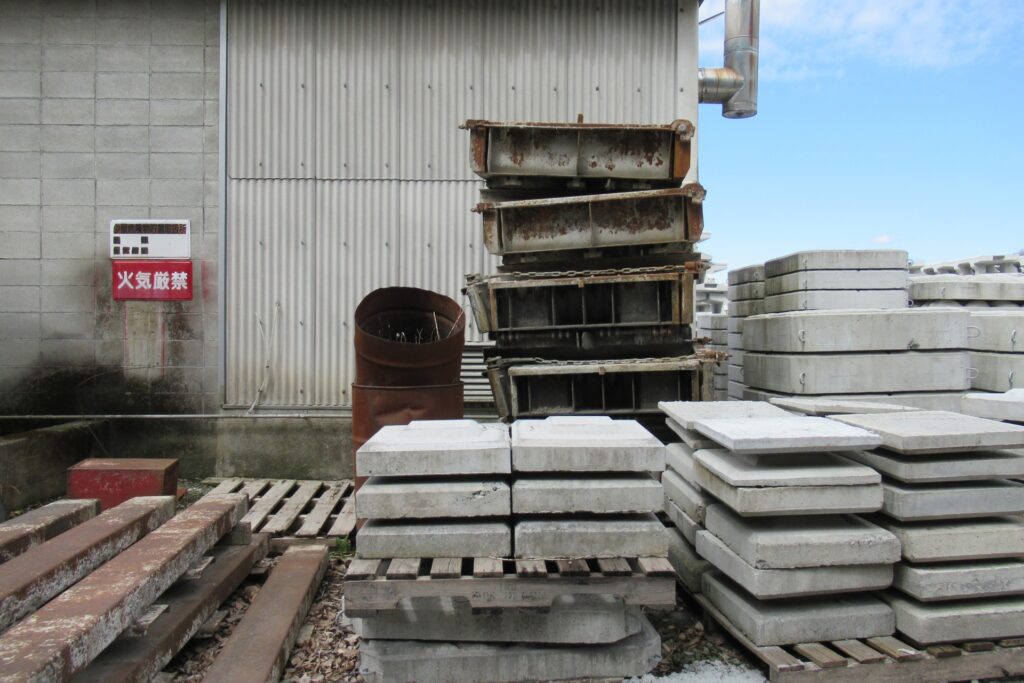
資材や在庫の管理が不十分だと、必要なタイミングで材料が届かない、過剰在庫で保管スペースが圧迫されるといった事態が起こりやすくなります。このような資材関連の問題は、作業待ちや無駄な移動、不要な発注につながり、現場の生産効率を著しく低下させる要因です。
また、在庫情報の更新がリアルタイムで行われていない場合、誤った在庫数に基づく生産計画が立てられ、過不足が発生するリスクも高まります。
これを防ぐには、在庫管理システムやバーコード・RFIDによる自動管理の導入が有効です。さらに、資材置き場の整理整頓や定置管理を徹底することで、取り間違い・探し物の時間も削減できます。
情報管理に関する要因
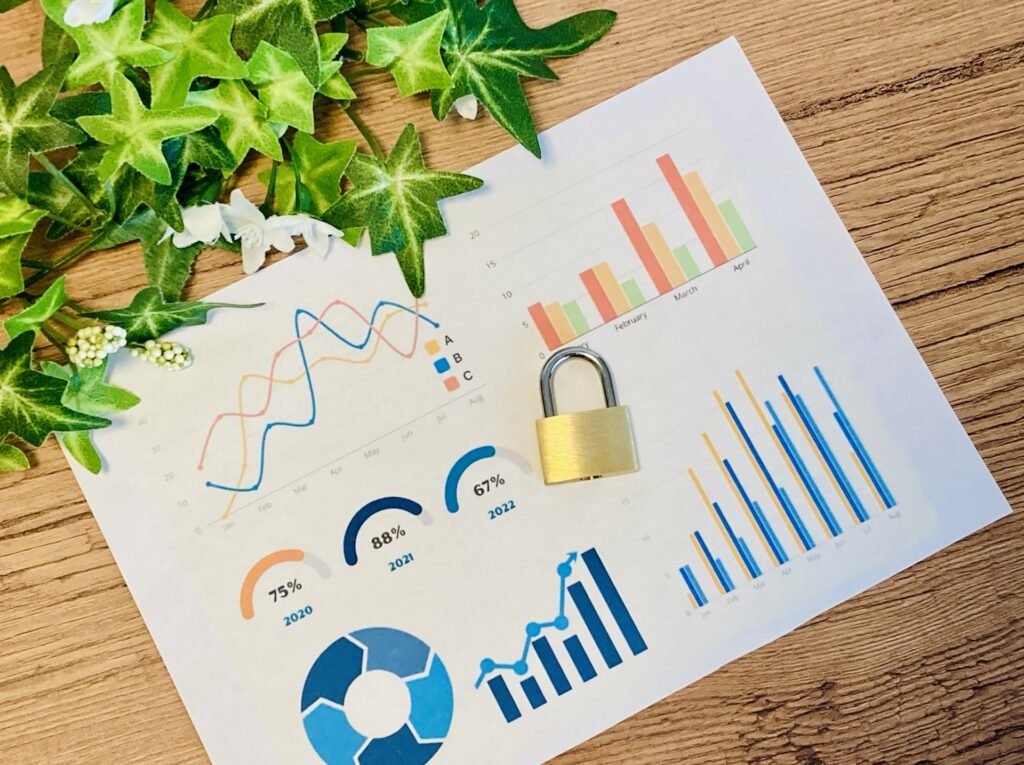
情報の共有や管理が適切でない場合、作業ミスや伝達漏れ、重複作業といったトラブルが発生しやすくなります。製造指示が紙ベースで管理されている場合、更新ミスや書類の紛失が原因で、現場で混乱が生じることも少なくありません。
また、部門間の情報連携が弱いと、材料の納品や製品の出荷タイミングにズレが生じ、生産スケジュール全体に影響を及ぼします。
こうした問題を解消するには、デジタル化による情報の一元管理が重要です。製造実行システム(MES)や工程管理ツールを活用すれば、リアルタイムで進捗や在庫状況を把握でき、判断や対応がスムーズになります。
製造現場の効率を確認するのに有効な指標
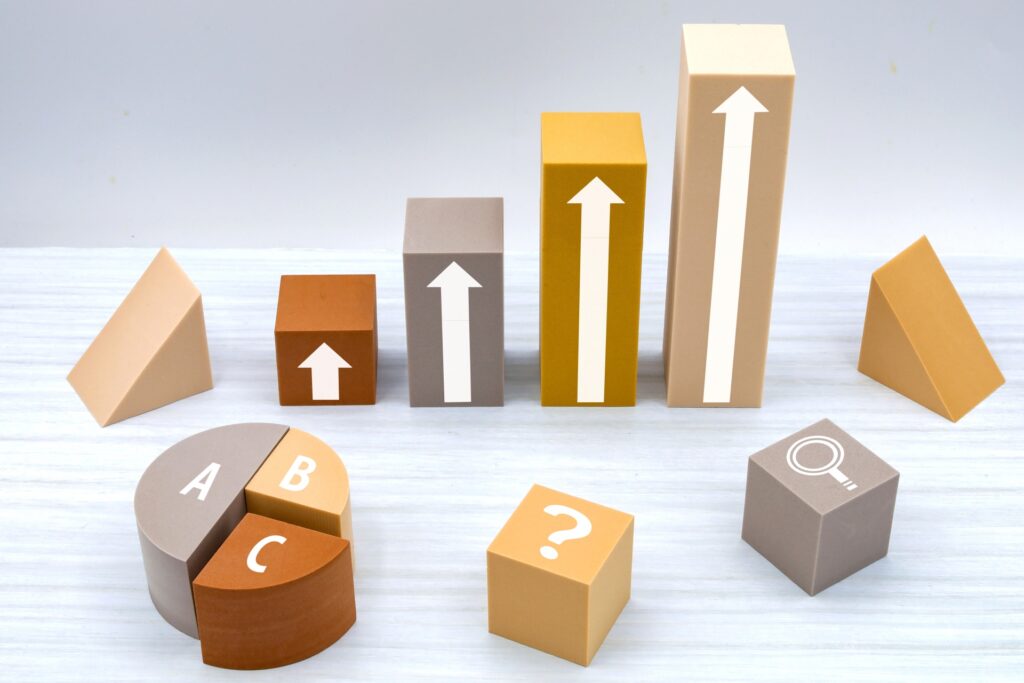
製造現場における課題を把握し、改善に向けた取り組みを進めるには、現状の効率を数値として正確に把握することが不可欠です。感覚や経験だけに頼った判断では、問題の本質を見落とすリスクが高まります。
代表的な指標には、以下の4つがあります。
それぞれの指標について解説していきます。
OEE(総合設備効率)
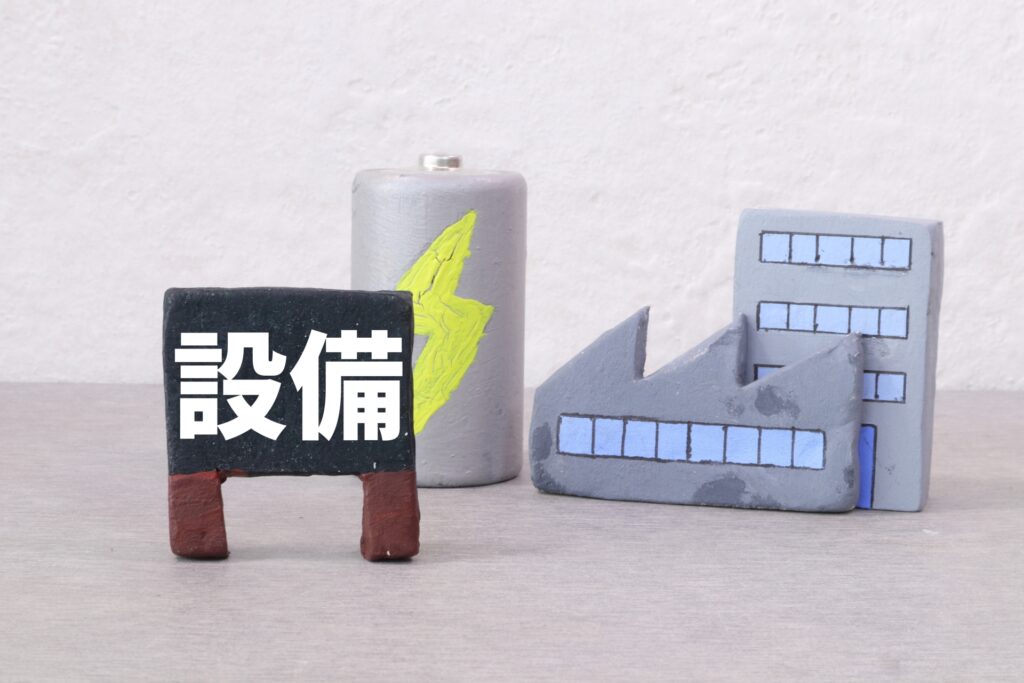
OEE(総合設備効率)は、製造現場において設備がどれだけ効率よく稼働しているかを総合的に評価する指標です。稼働率・性能・品質という3つの要素から算出され、100%に近いほど設備が無駄なく有効に活用されている状態を意味します。
具体的には、以下の計算式で求められます。
OEE = 稼働率 × 性能 × 品質
OEEを活用することで、「どこに非効率があるのか」を具体的に突き止めることが可能です。例えば、稼働率が低ければ段取りや故障の影響が疑われ、性能が低ければ速度設定や機械の老朽化が原因かもしれません。
稼働時間率
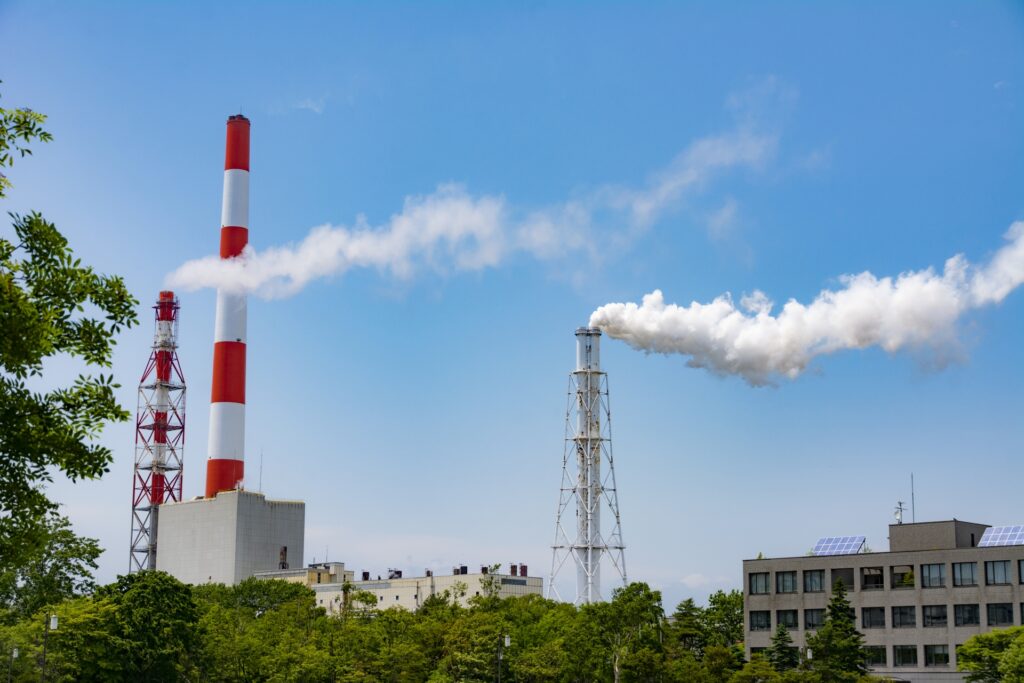
稼働時間率とは、設備やラインが計画された稼働時間のうち、実際に稼働していた時間の割合を示す指標です。設備や人員の稼働状況を確認する上で、基本でありながら重要な数値です。計算式は以下の通りとなっています。
稼働時間率(%)= 実稼働時間 ÷ 計画稼働時間 × 100
この数値が低い場合、故障や段取り作業、材料待ちなどのロスタイムが多い可能性が高いです。稼働時間率を定期的に確認することで、どの時間帯や工程で停止が多いのかを可視化し、改善活動につなげることが可能です。
歩留まり率
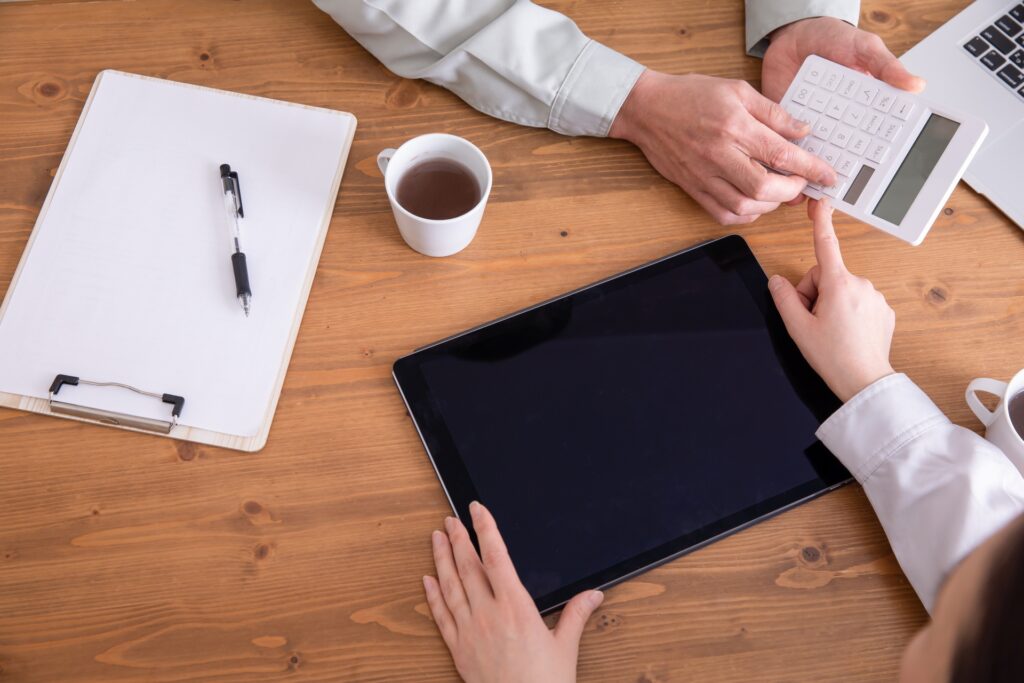
歩留まり率は、投入した原材料や部品のうち、最終的に製品として出荷可能な「良品」として完成する割合を示す指標です。製品品質や工程の安定性を測るうえで、非常に重要な役割を担っています。
歩留まり率は以下のように計算されます。
歩留まり率(%)= 良品数 ÷ 総生産数 × 100
この数値が低い場合、工程の中に品質を損なう要因が存在している可能性があります。例えば、不適切な温度管理や作業ミス、材料のばらつきなどが原因となることが想定されます。
歩留まり率の改善は、材料コストの削減や再加工工数の削減にも直結し、利益率の向上につながります。
労働生産性
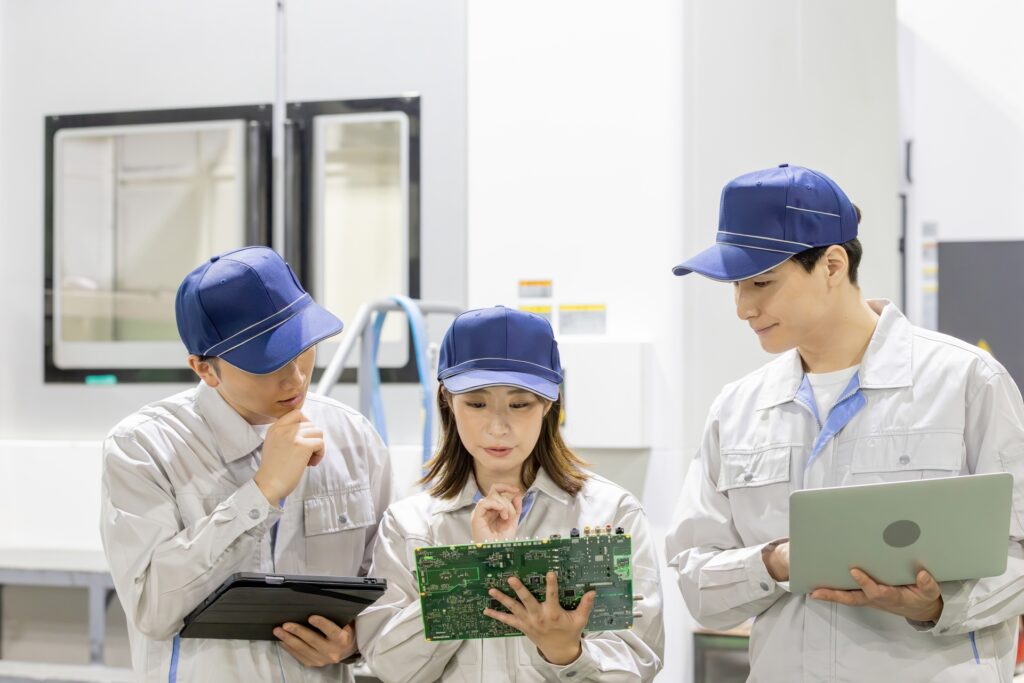
労働生産性は、従業員1人あたりが生み出す付加価値や生産量を示す指標点です。人手不足が深刻化する中、少人数でも高い成果を出せる体制づくりが求められています。一般的な計算式は以下の通りです。
労働生産性(付加価値)= 付加価値額 ÷ 総労働時間
労働生産性(生産量)= 生産数 ÷ 総労働時間
この数値が低い場合、作業のムダや待機時間、工程設計の見直しが必要です。
労働生産性を向上させるには、作業の自動化や効率化、スキルアップ支援、適切な人員配置が不可欠です。また、個人別・チーム別に指標を分析することで、教育の重点や現場の改善策も見えてきます。
製造現場の効率を改善する5つのテクニック
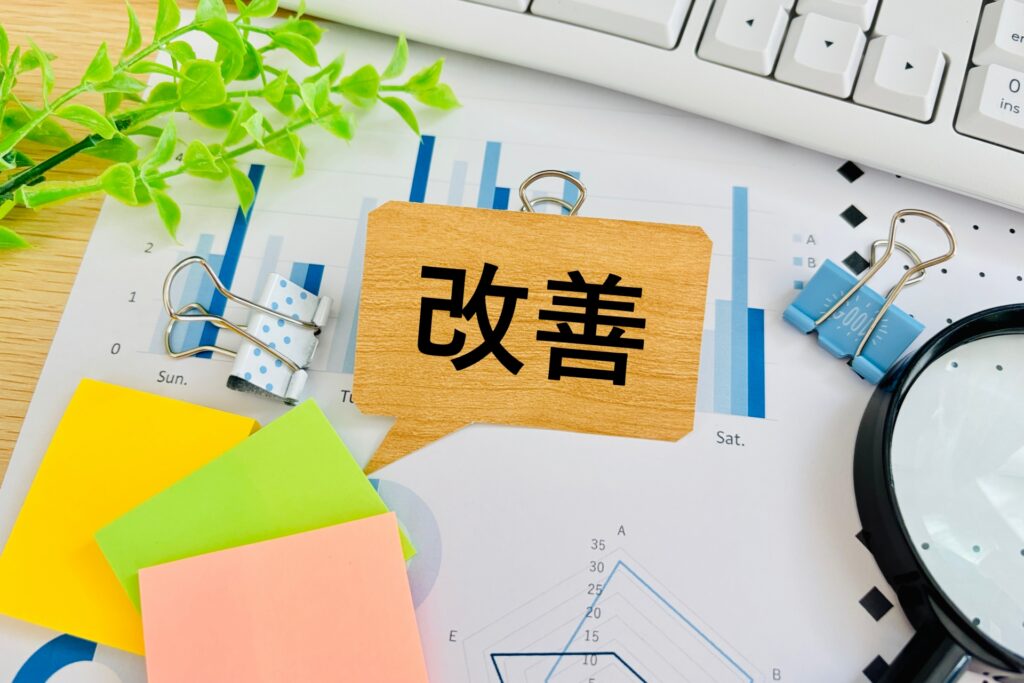
製造現場の生産効率を高めるためには、現場で起きている非効率の原因を把握し、それに対して的確な改善策を講じることが重要です。具体的な改善テクニックとして活用できるのは、以下の5つです。
それぞれのテクニックについて解説していきます。
5S(整理・整頓・清掃・清潔・しつけ)の徹底
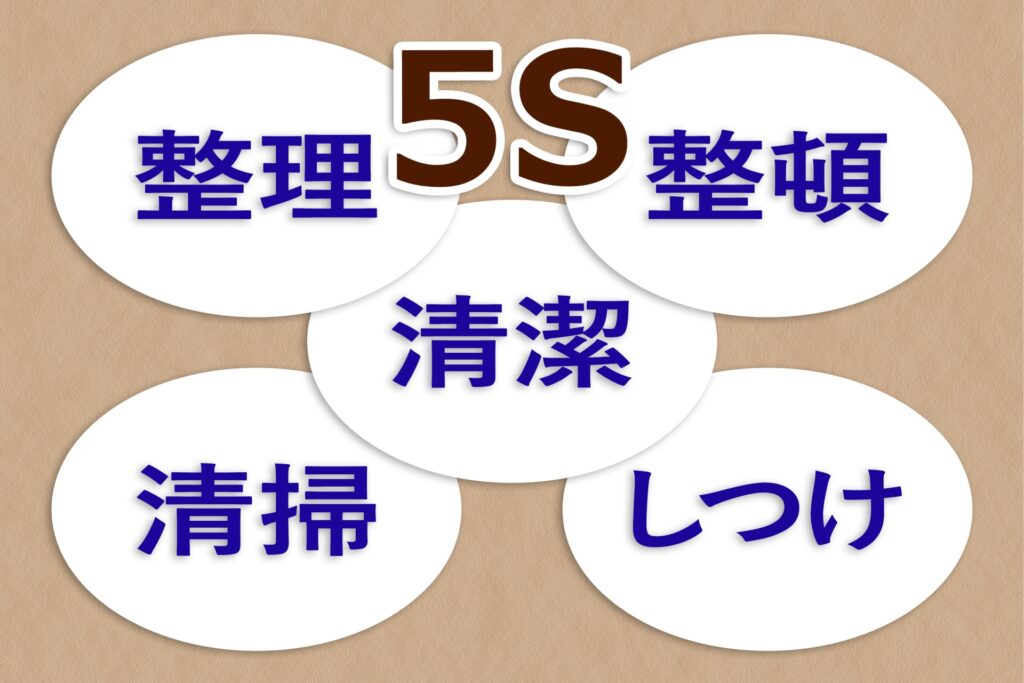
5Sとは、「整理・整頓・清掃・清潔・しつけ」の頭文字を取ったものです。作業環境の整備を通じてムダやミスを減らし、作業効率を向上させることが目的です。
整理整頓を徹底すれば、必要な物をすぐに取り出せるようになり、時間のロスやストレスも軽減されます。また、日常的な清掃や点検によって設備の異常を早期に発見でき、トラブルを未然に防ぐことも可能です。
さらに、5S活動を従業員全体に定着させることで、現場に対する意識や責任感も向上し、職場全体の雰囲気が良くなります。導入時には、「見える化」や「定位置管理」を取り入れることで、誰が見ても整った状態を維持しやすくなります。
標準作業の整備と教育の平準化
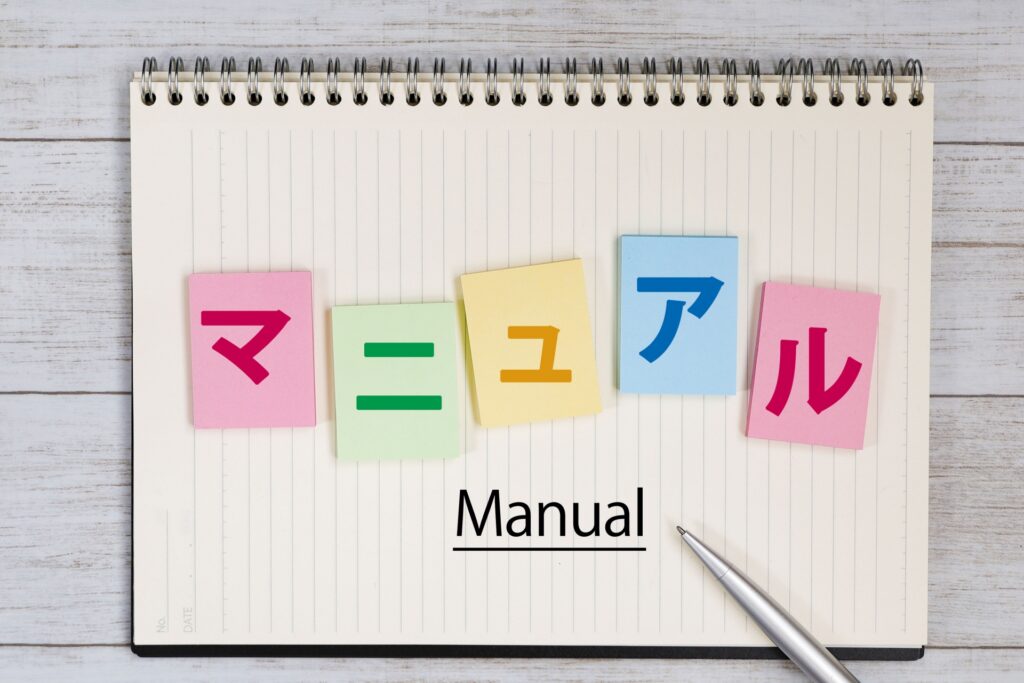
作業のバラつきが多い現場では、品質の不安定さや生産効率の低下が避けられません。そのため、標準作業の整備と作業者への教育の平準化は、効率改善において重要な施策です。
標準作業を導入することで、作業時間や品質のばらつきを抑えられ、改善活動の基準としても活用できます。熟練者と新人の間で作業手順が異なると、工程間でのズレや無駄が発生します。作業内容を可視化し、全員が同じ基準で作業することが、効率向上につながります。
また、教育面では動画やマニュアルによる視覚的ツールを活用することで、短期間でのスキル習得が可能です。OJTに偏らない教育体制を整えることで、人材育成の効率も大きく改善されます。
ラインバランスの最適化
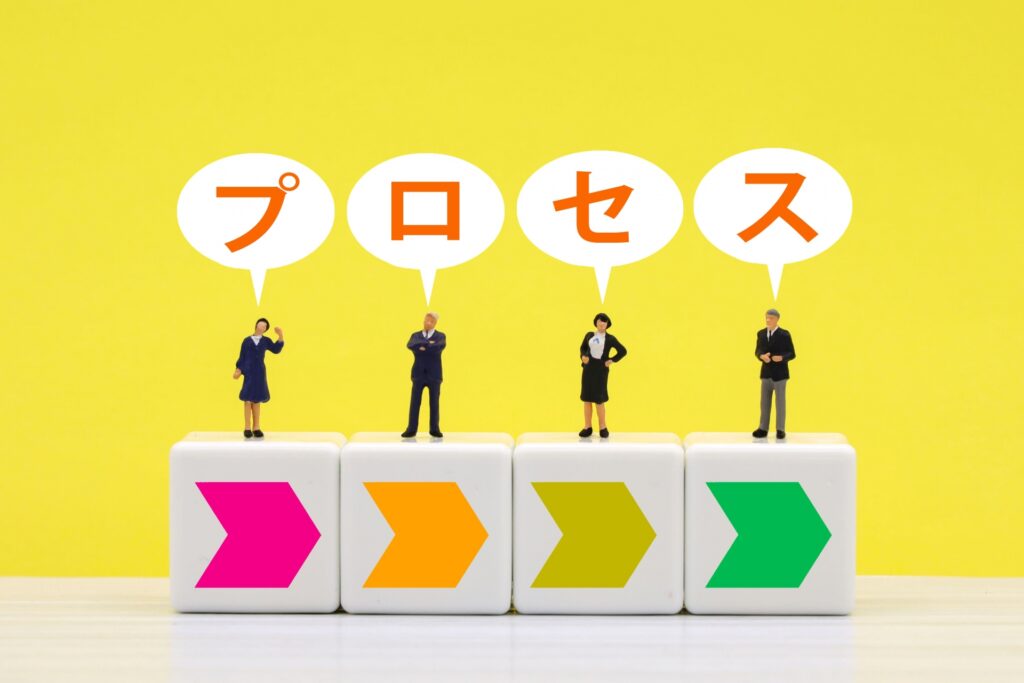
生産ラインでは、各工程の作業負荷が不均衡であると、全体の生産性が著しく低下します。ある工程だけが常に忙しく、他の工程が手待ち状態になると、ライン全体の流れが滞り、ムダな時間が発生してしまいます。
そこで最適化におすすめなのが、ラインバランスです。ラインバランスとは、各作業工程の所要時間や作業内容を見直し、全体として均等に負荷を配分することを指します。
これにより、作業者の負担が偏らず、無駄な待機や作業の重複を防ぐことが可能です。改善には工程分析を通じて、工程ごとの作業時間を正確に把握することが必要です。
具体的には、ボトルネック工程を抽出して人員を増やす、作業を分割して前工程に振り分けるといった対応が効果を発揮します。また、生産スケジュールと連動させたタクトタイムの見直しや、柔軟なライン編成もラインバランスの維持に寄与します。
工程間の搬送や動線の短縮
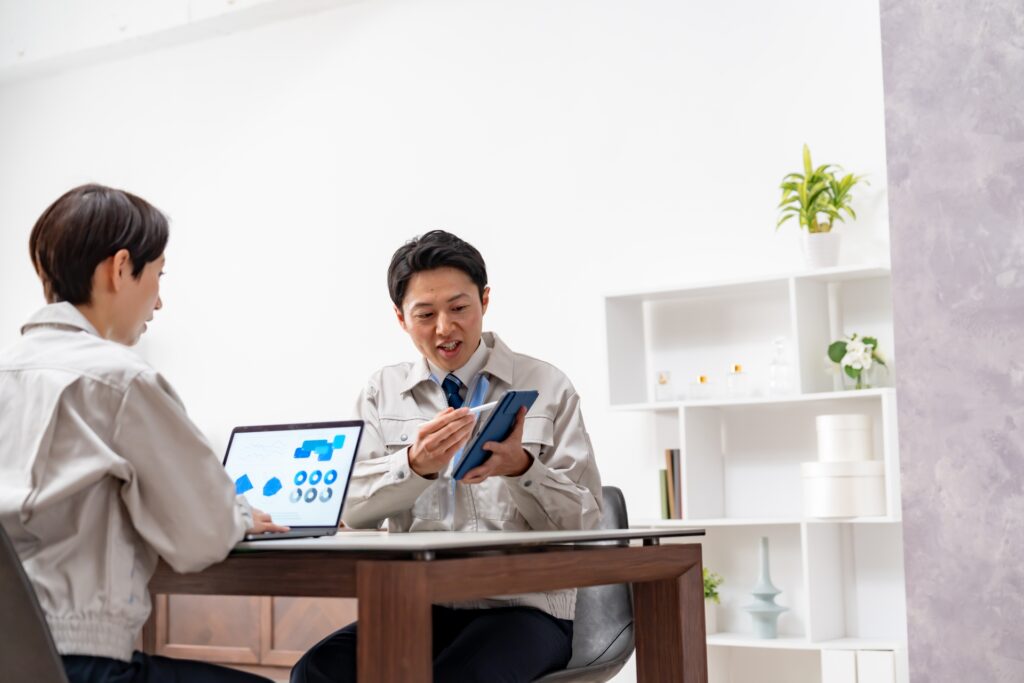
製造現場では、部品や製品の搬送に多くの時間が費やされているケースが少なくありません。工程間の距離が長かったり、作業者の動線が複雑であったりすると、無駄な移動や搬送待ちが発生し、効率を著しく低下させます。
これを解消するためには、工程配置と搬送経路の見直しが有効です。まずは、製品の流れに沿ったレイアウトを再設計し、搬送距離を最小限に抑えます。また、台車やコンベアなどの搬送補助機器を活用することで、搬送作業の自動化も実現可能です。
さらに、作業者の動線を可視化し、頻繁な移動が発生している箇所に改善の余地がないかを検討することも効果的です。動線の短縮は、作業時間の短縮だけでなく、作業者の負担軽減や安全性向上にもつながります。
IoT・センサによる稼働データの見える化
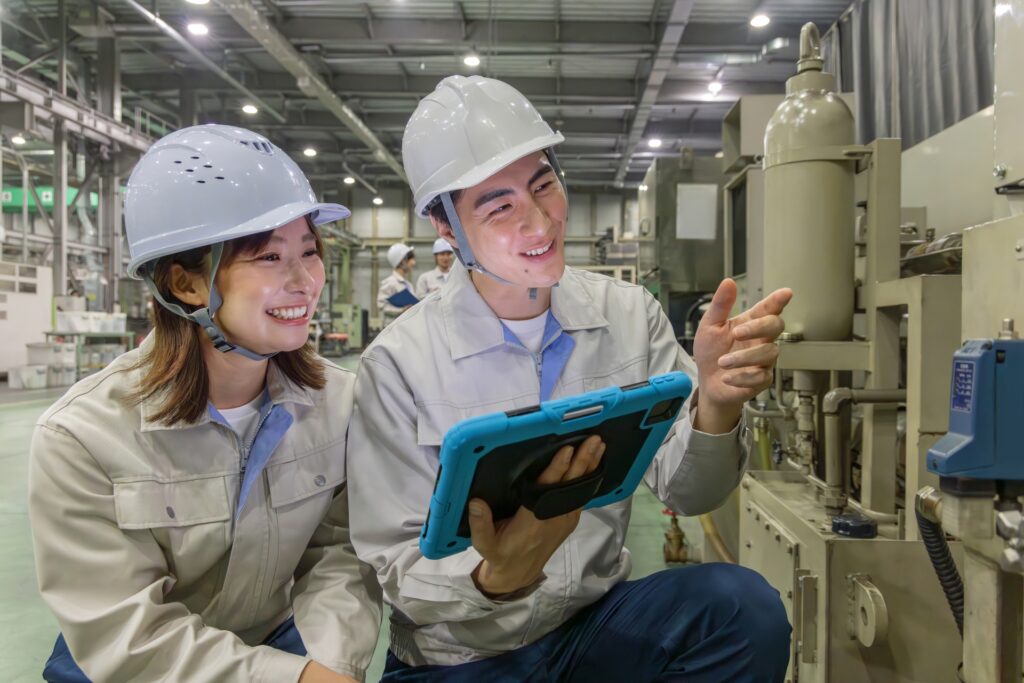
IoTやセンサ技術の進化により、製造現場の稼働状況をリアルタイムで把握できるようになってきました。以下のような要素を「見える化」することで、現場の非効率をデータに基づいて明確に捉えることが可能です。
- 設備の稼働率
- 故障履歴
- 作業時間
- 停止要因
また、ライン全体の稼働状況を可視化することで、工程間のズレやボトルネックの特定も容易になります。
IoTによるデータ収集は、人の目では把握しきれない問題を洗い出し、根拠に基づいた改善を可能にします。クラウドやダッシュボードを活用すれば、現場担当者だけでなく、管理者や経営層も状況を共有できるようになるでしょう。
製造現場の生産効率向上がもたらす効果
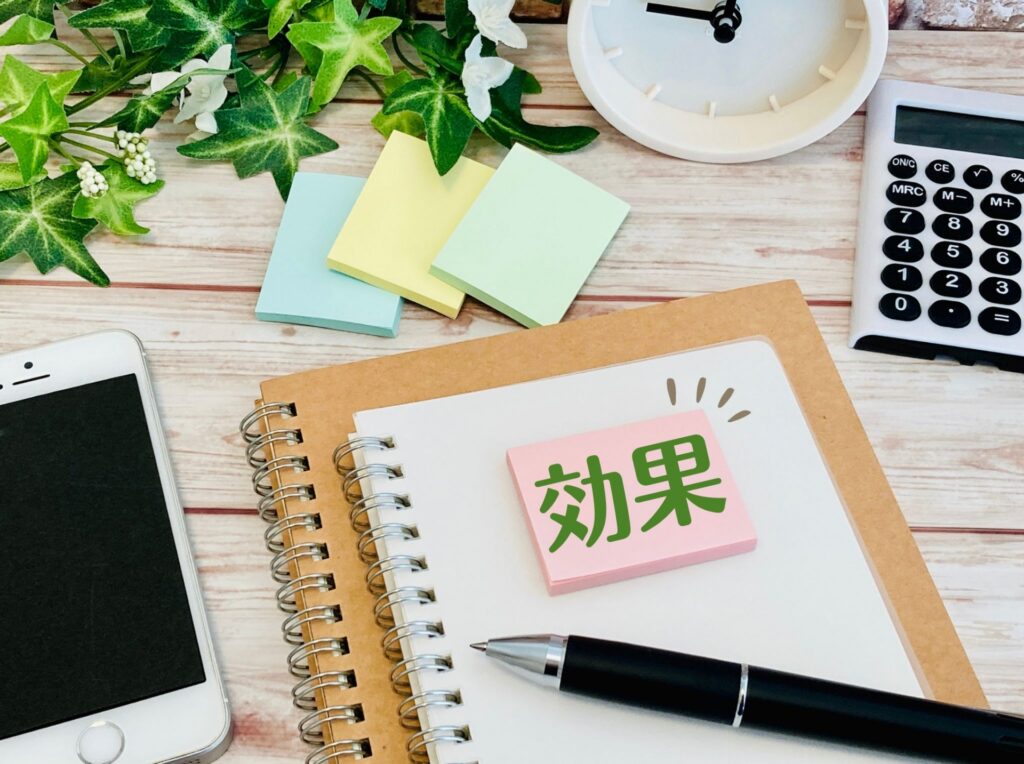
製造現場の生産効率を高めることは、単なる作業スピードの改善にとどまりません。工程ごとの無駄やムラを排除し、全体工程の最適を図ることで、以下の効果が期待できます。
それぞれの効果について解説していきます。
コスト削減
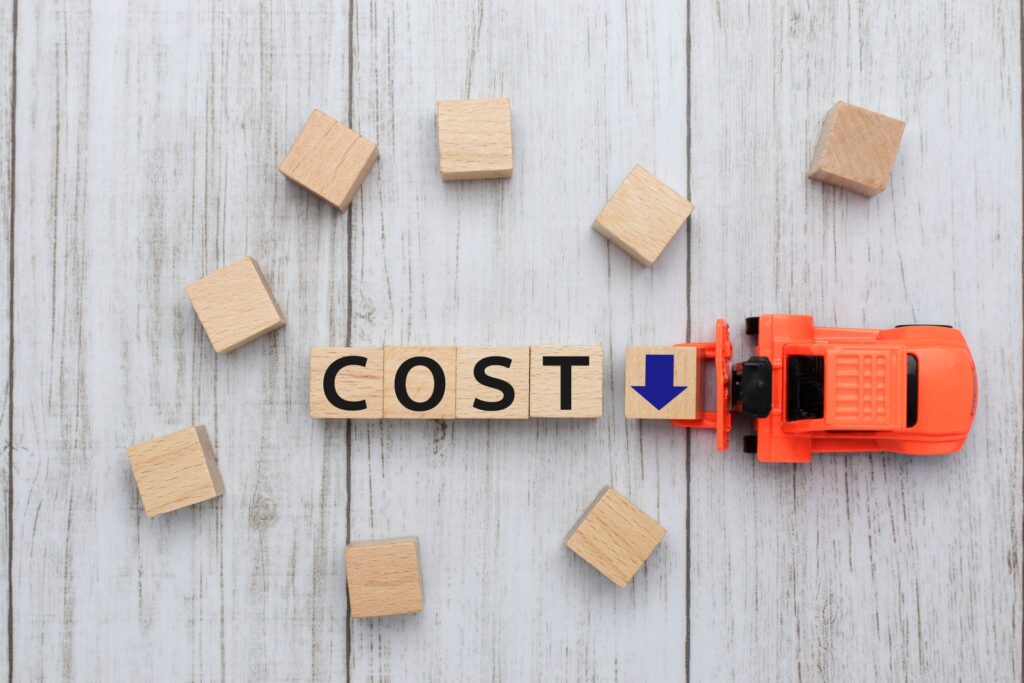
生産効率を高めることにより、直接的に得られる効果がコスト削減です。作業時間や労力を最小限に抑えながら、同じ生産量またはそれ以上の成果を上げられるようになることで、以下の経費の圧縮が可能です。
- 人件費
- エネルギー費
- 設備運用コスト
また、不良品の発生が減れば再加工や廃棄のコストも削減されます。さらに、搬送や在庫管理などの間接業務が効率化されれば、全体の運営コストを大きく見直すことが可能です。
これらの削減効果は、単年の改善だけでなく、継続的な収益体質の強化にもつながります。省エネ設備の導入やIoTによる稼働最適化など、初期投資を伴う施策でも、長期的に見ると十分な投資対効果を得られるケースが多くあります。
生産開始から納品までの時間が短縮
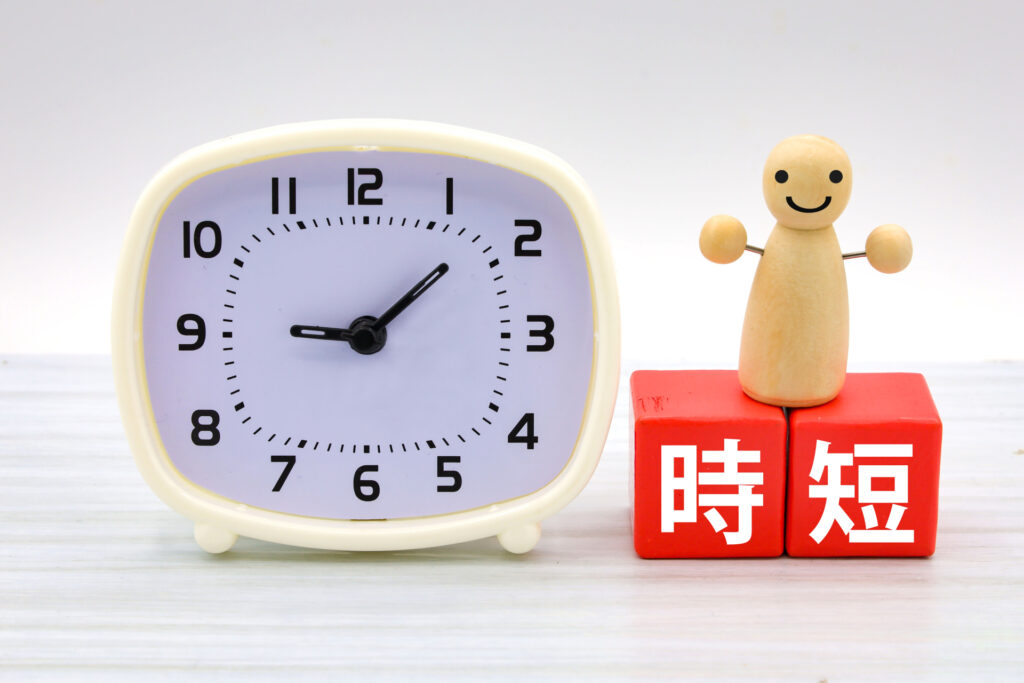
製造現場の効率が向上すると、製品が完成するまでのリードタイムを短縮することが可能です。リードタイムとは、受注から製造、検査、出荷、納品までに要する一連の時間のことを指します。この時間を短くできれば、顧客満足度の向上だけでなく、在庫圧縮やキャッシュフローの改善も期待できます。
これにより、突発的な納期遅延や手直し対応の発生を抑えることが可能です。また、段取り替えの時間短縮や、スムーズな部品供給体制の構築も、リードタイムの短縮に貢献します。
リードタイムが短い企業は、顧客の急な注文にも迅速に対応できるため、営業面でも有利に働きます。加えて、短納期を実現することは、新たな取引先の開拓や、信頼の獲得にも直結するでしょう。
品質の安定化
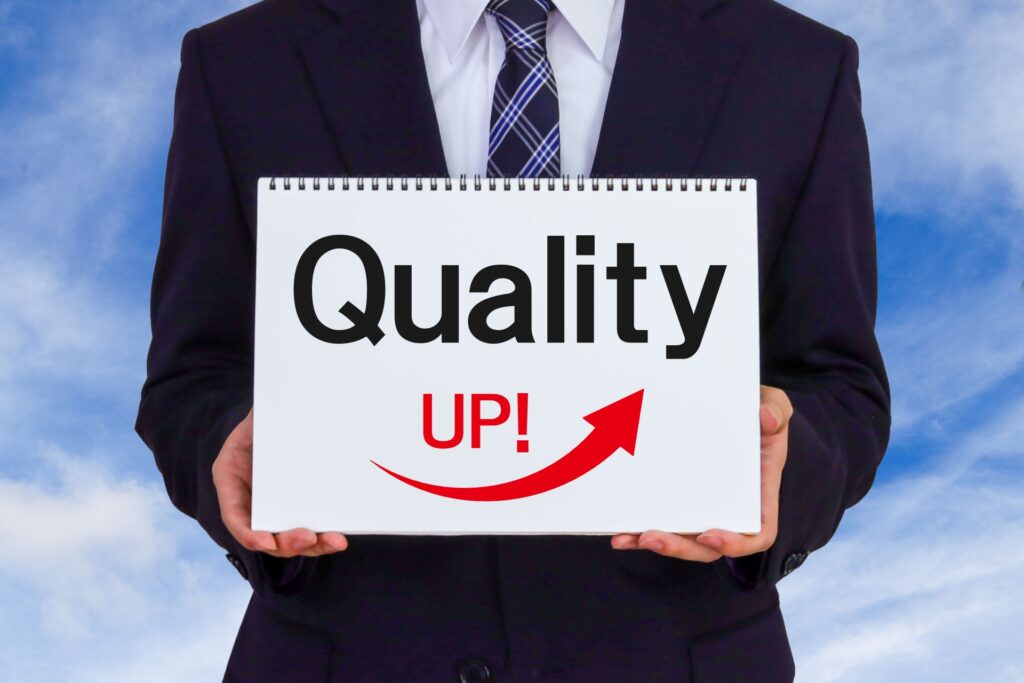
生産効率を高める施策は、製品の品質安定にも大きく寄与します。以下のような対策によって、品質トラブルの発生を未然に防ぐことが可能です。
- 作業手順の標準化
- 設備のメンテナンス強化
- リアルタイムのデータ活用
標準作業を徹底すれば、作業者ごとのばらつきが減り、製品の仕上がりが均一になります。IoTやセンサによって異常を即座に検知できれば、不良品が大量に発生する前に対処できます。
品質の安定化は、顧客満足度の向上はもちろんのこと、検査工数の削減やクレーム対応コストの低減にも効果的です。また、安定した品質を維持できれば、ブランドの信頼性が高まり、長期的な受注獲得や継続取引につながる可能性も高まります。
在庫削減とキャッシュフローの改善
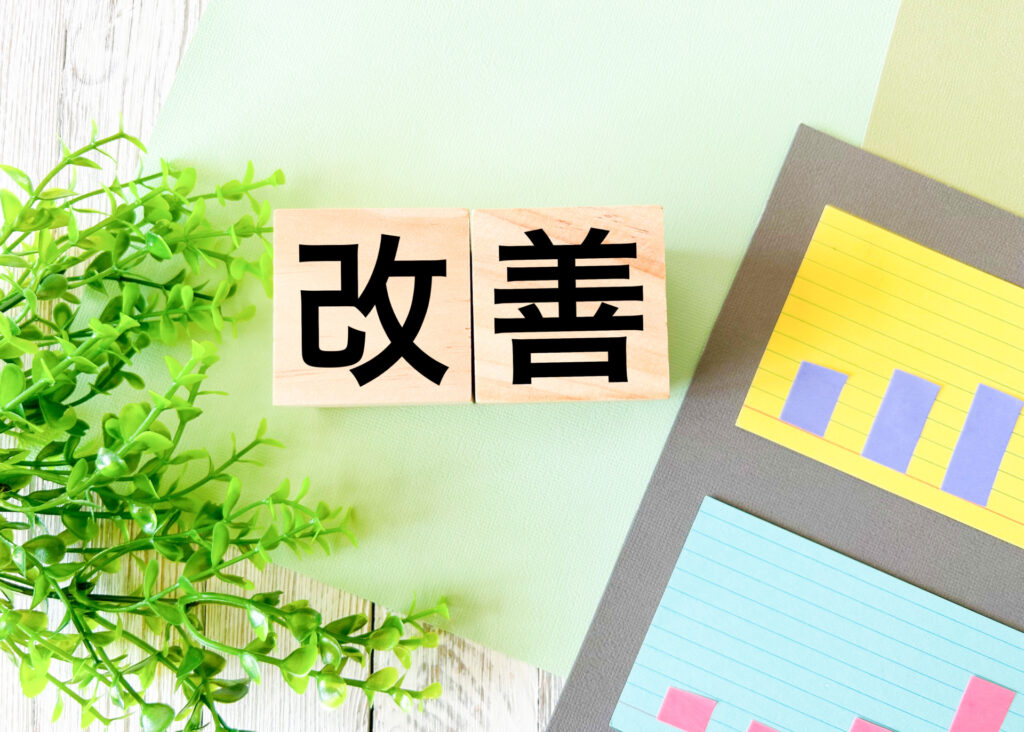
製造現場の効率が向上すると、必要以上に在庫を抱える必要がなくなり、在庫量の適正化が実現します。在庫削減は、倉庫スペースの圧縮や保管コストの削減だけでなく、キャッシュフローの改善にも効果的です。
工程のムダを排除して生産リードタイムを短縮すれば、材料の在庫回転率が上がり、滞留する資金を減らせます。
また、在庫を減らすことで、棚卸や管理業務の負担も軽減され、現場の生産性向上も可能です。在庫削減は、単なるコストカットではなく、企業全体の収益性と健全な財務体質を築くための戦略的な施策です。
計量工程の効率化なら全自動組み合わせはかりがおすすめ
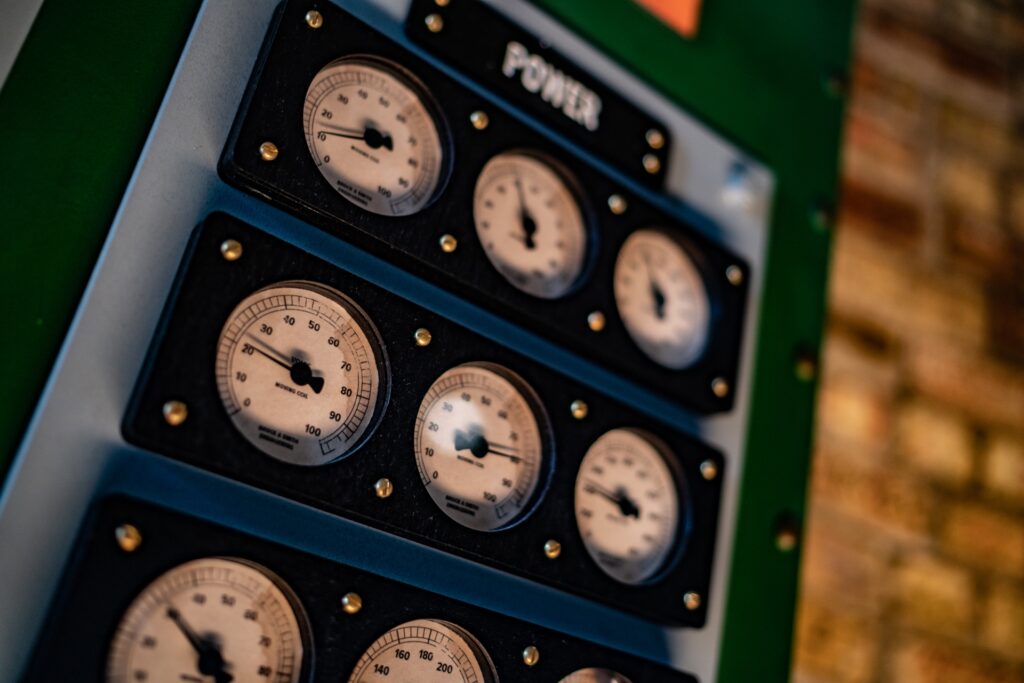
製造現場における計量工程は、正確性とスピードの両立が求められるプロセスです。しかし、手作業による計量では、作業者のスキルや体調によってばらつきが生じやすく、計量ミスや作業時間のムラが発生することもあります。
こうした課題を解決し、効率と精度を同時に向上させる手段として注目されているのが、全自動組み合わせはかりの導入です。全自動組み合わせはかりは、複数の計量ユニットを用いて材料を自動で組み合わせ、あらかじめ設定された目標重量に最も近い組み合わせを高速で選び出します。
この技術により、従来手作業では数十秒かかっていた作業が、わずか1〜2秒で完了するようになり、作業時間を大幅に短縮できます。また、グラム単位の高精度な計量が可能で、歩留まりの向上にも直結します。
さらに、操作が簡単で誰でも同じ精度で作業できるため、作業者のスキル差による品質のばらつきも低減可能です。全自動組み合わせはかりは製造ラインへの組み込みも柔軟に対応できるため、省人化や自動化を進めたい現場に最適です。
おすすめの全自動組み合わせはかりメーカー3選
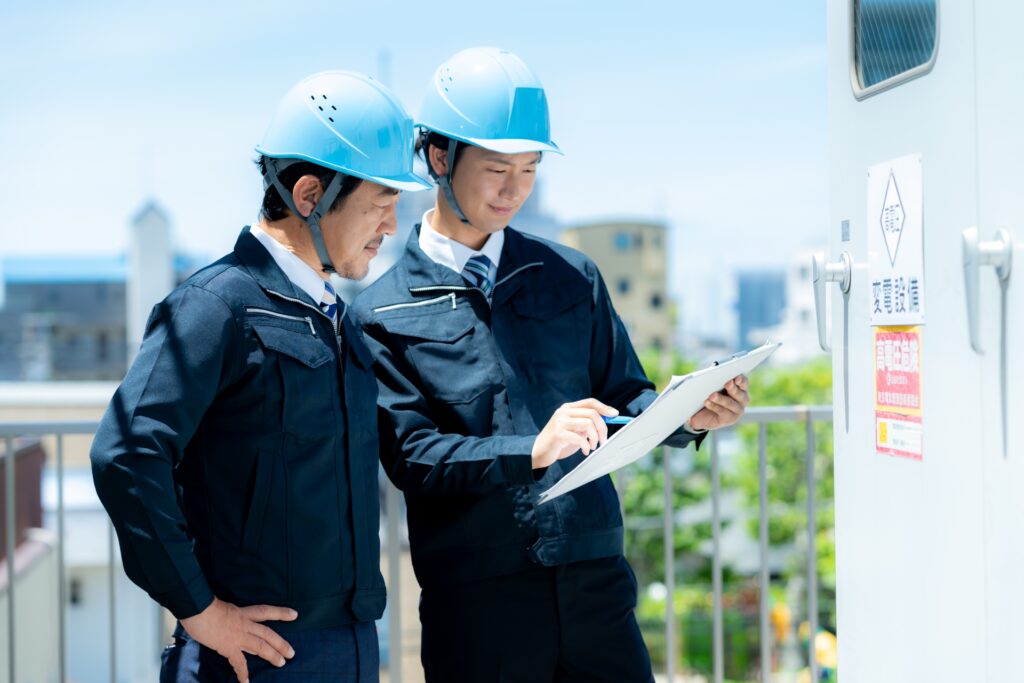
以下では、信頼性・性能・導入後の対応といった観点から、高い評価を得ている全自動組み合わせはかりのメーカーを3社ご紹介します。
それぞれの強みを理解し、自社のニーズに最適な製品選定の参考にしてください。
大和製衡株式会社
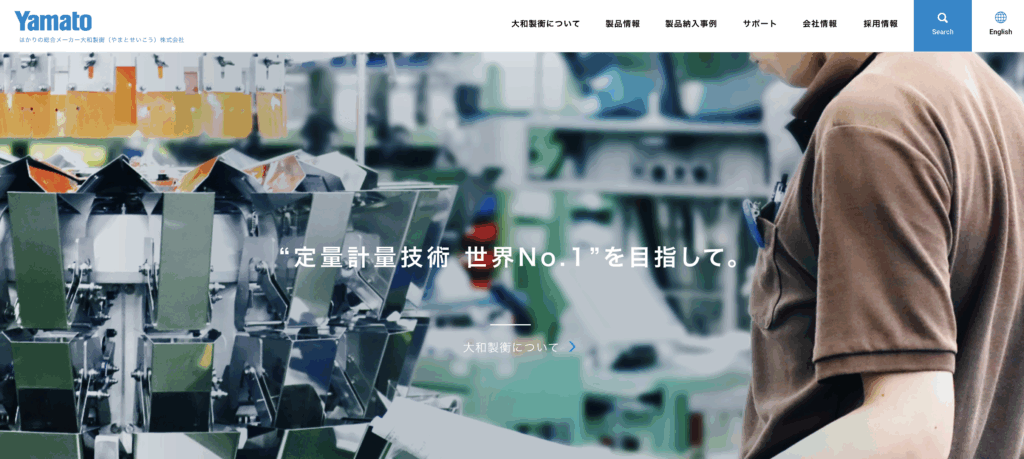
大和製衡株式会社は、兵庫県明石市に本社を構える計量機器メーカーで、業界トップクラスの技術力と豊富な製品ラインアップを誇ります。
項目 | 詳細 |
会社名 | 大和製衡株式会社 |
住所 | 〒673-8688(〒673-0849) 兵庫県明石市茶園場町5番22号 |
電話番号 | 078-918-5526 |
公式HP | https://www.yamato-scale.co.jp/ |
全自動組み合わせはかりにおいては、独自の制御技術と多彩なオプションを備えたモデルを多数展開しており、食品・医薬・化学分野での導入実績も豊富です。1g単位の高精度な計量性能に加え、衛生面やメンテナンス性にも優れています。
また、多言語対応の操作画面やクラウド連携機能など、現場のDX化にも柔軟に対応可能です。サポート体制も充実しており、国内外に設置された拠点による迅速な保守対応や、導入後の運用支援も評価されています。
全自動組み合わせはかりの導入をお考えの方は、一度の大和製衡株式会社ホームページを訪れてはいかがでしょうか。
以下の記事では、大和製衡株式会社の特徴や口コミ、導入事例などをさらに詳しく解説していますので、気になる方はぜひ一度チェックしてみてください。
株式会社イシダ
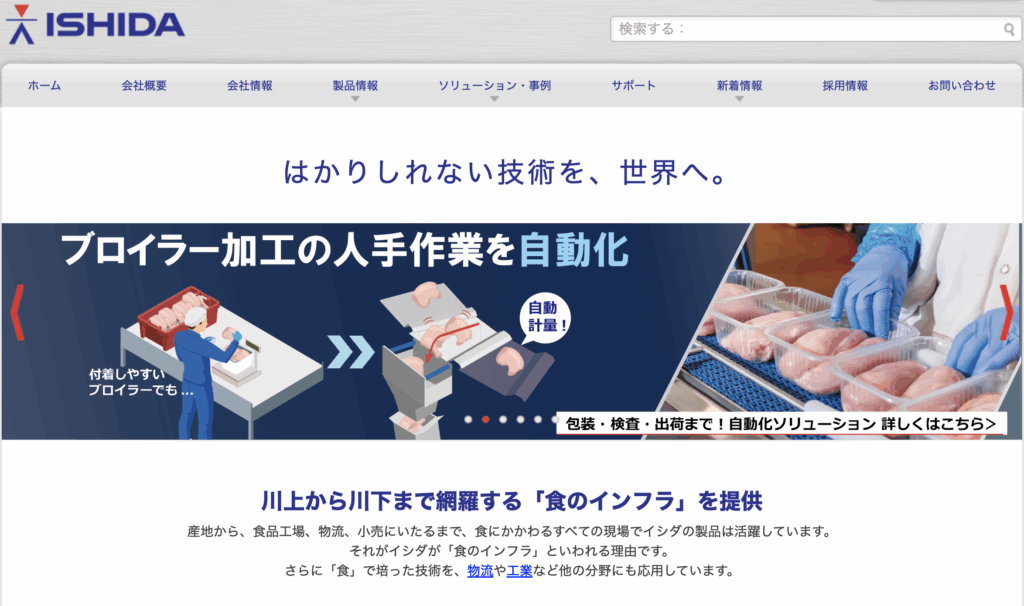
株式会社イシダは、京都府に本社を構える老舗の計量・包装・検査機器メーカーで、世界中にネットワークを展開しているグローバル企業です。
項目 | 詳細 |
会社名 | 株式会社イシダ |
住所 | 〒606-8392 京都市左京区聖護院山王町44番地 |
電話番号 | 075-771-4141 |
公式HP | https://www.ishida.co.jp/ww/jp/ |
同社の組み合わせはかりは、製品ごとの特性に応じた最適な組み合わせアルゴリズムを搭載しており、無駄な材料ロスを最小限に抑えることが可能です。また、操作性に優れたタッチパネル式のコントロールユニットや、生産ライン全体の制御との連携機能なども備えています。
特筆すべきは、イシダが提供する「スマートファクトリー」構想の一環として、全自動はかりにIoTやAIを融合させている点です。リアルタイムの稼働監視や予防保全、歩留まり分析など、工場全体の最適化につながるソリューションが充実しています。
以下の記事では株式会社イシダの評判や特徴について紹介しているので、ぜひ参考にしてください。
アンリツ株式会社
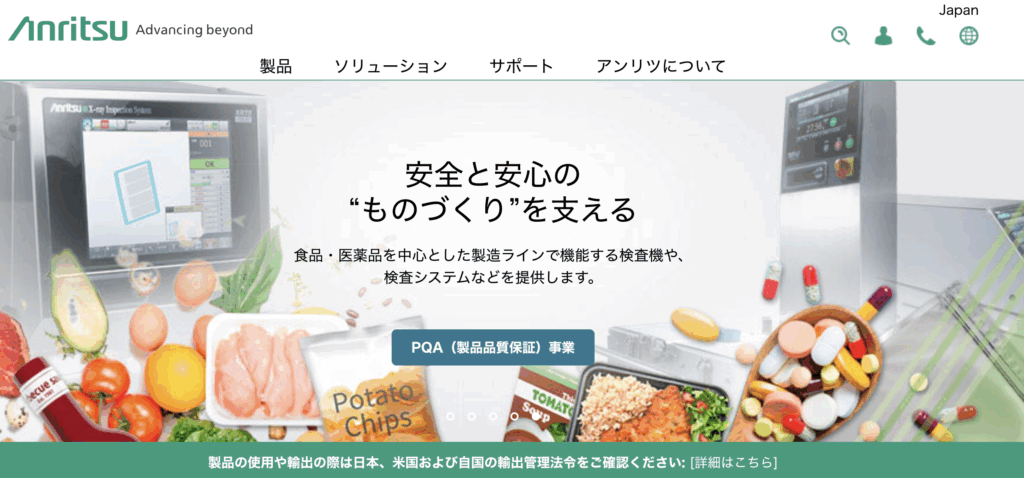
アンリツ株式会社は、通信機器の分野で知られる一方、検査機・計量機の分野においても長年の実績を持つ総合メーカーです。
項目 | 詳細 |
会社名 | アンリツ株式会社 |
住所 | 〒243-8555神奈川県厚木市恩名5-1-1 |
電話番号 | 046-223-1111 |
公式HP | https://www.anritsu.com/ja-jp/ |
アンリツのはかりは、シンプルな構造と直感的な操作画面が特徴で、初めて導入する現場でもすぐに使いこなせる点が強みです。高速かつ安定した計量処理を実現しており、少量多品種の生産体制にも柔軟に対応します。
また、ステンレス製で衛生的な設計となっており、HACCPやFSSC22000といった衛生基準にも準拠しています。サポート面でも、全国にサービス拠点を有し、迅速なメンテナンス対応が受けられるため、万が一のトラブル時も安心です。
以下の記事ではアンリツ株式会社の評判や特徴について紹介しているので、ぜひ参考にしてください。
まとめ

製造現場の効率化は、単なる業務改善にとどまらず、コスト削減や品質の安定、さらには納期短縮キャッシュフローの改善といった経営面にも効果をもたらします。特に、計量工程における効率向上は全体最適にもつながりやすく、全自動組み合わせはかりの導入は有効です。
本記事で紹介した要因分析の指標や実践的なテクニックを踏まえ、まずは自社の現状を客観的に把握するところから始めましょう。そして、課題に合った設備の選定や運用改善を段階的に進めていくことで、持続的な生産性向上を実現することが可能です。