工場の人手不足に悩み、対応に苦戦している現場の担当者は多いはずです。製造現場では、慢性的な人材不足や作業負担の偏りが課題となっており、省人化への関心が高まっています。特に近年は、AIやセンサー技術の進化により、以前は人手に頼らざるを得なかった工程でも自動化が実現できるようになってきました。
省人化を進めることで、人件費の抑制や品質の安定化、作業効率の向上といった多くのメリットが得られます。また、熟練作業者の退職に伴う技術継承の問題にも対応しやすくなり、将来的な生産体制の維持にもつながります。
本記事では、工場の省人化における課題と最新の解決手法について、わかりやすくご紹介します。現場の見直しを検討している方は、ぜひ参考にしてください。
また、以下ではおすすめの組み合わせはかりメーカーについて紹介しているので、ぜひ参考にしてみてください。
工場の省人化とは?

工場の省人化とは、製造現場における人手の作業を減らし、効率的な生産体制を構築する取り組みを指します。
人材不足が深刻化する中、省人化は多くの現場で注目されています。具体的には、作業の自動化や設備の導入によって、これまで人が行っていた工程を機械やシステムに置き換えることが主な手法です。
省人化の目的は、単に人手を減らすことではありません。生産性の向上、品質の安定化、作業ミスの削減、安全性の向上といった多面的なメリットを実現することにあります。
また、労働環境の改善や属人化の解消にもつながるため、長期的な競争力の強化にも寄与します。このように工場の省人化は、製造現場における喫緊の課題と言えるでしょう。
省力化・少人化との違い
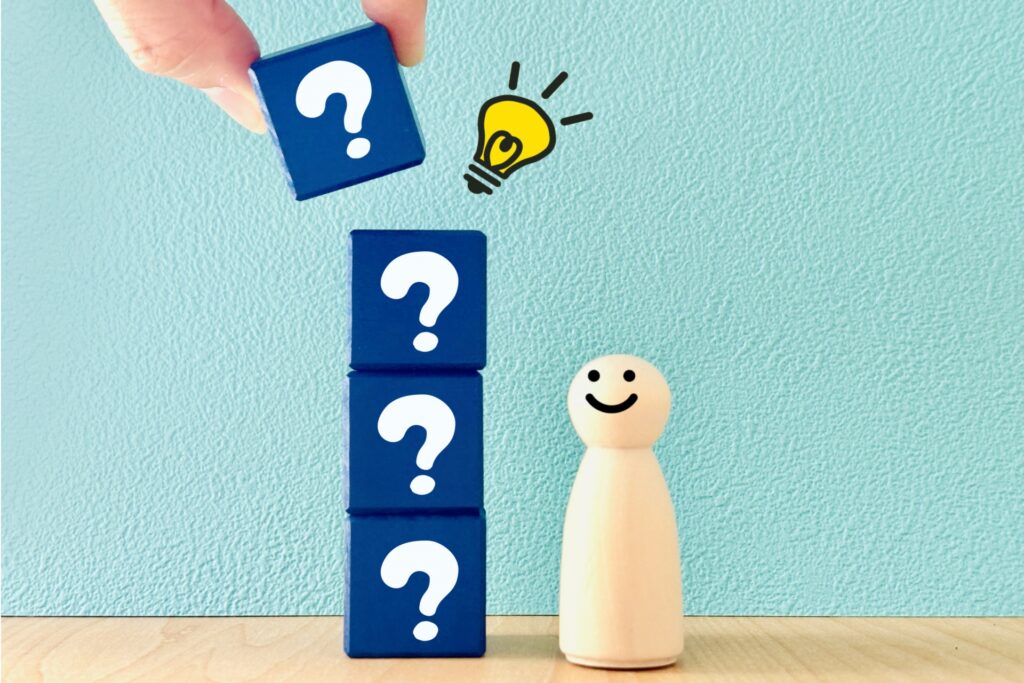
省人化と似た言葉に「省力化」や「少人化」がありますが、それぞれ意味が異なります。まず省力化は、作業に必要な労力を減らす取り組みを指します。人の数は変わらずとも、作業の質や安全性を向上させることが主な目的です。
次に少人化は、作業に必要な人数を減らすことを意味します。従来3人で行っていた工程を2人で対応できるように見直すといった例が該当します。
一方省人化は、言わば省力化や少人化の上位概念です。機械化や自動化によって、人手そのものを不要にし、最小限の人員で運用できる体制を目指します。つまり、省人化はより抜本的な変革を伴うものであり、設備投資や工程再設計を含むケースが多いのが特徴です。
工場を省人化するメリット
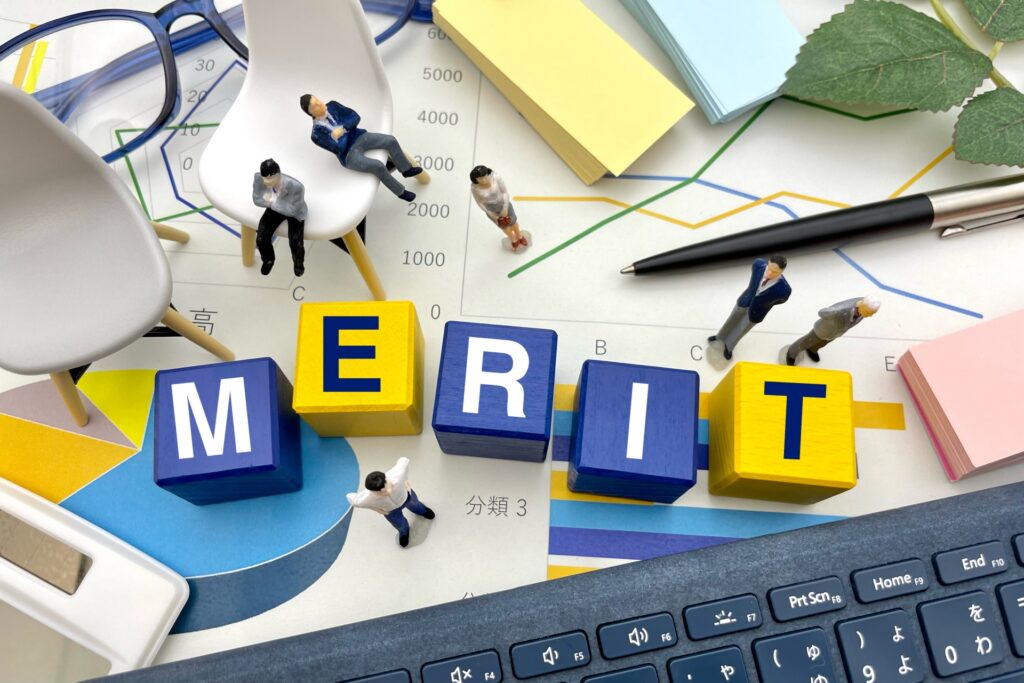
工場における省人化は、単なる人手不足対策にとどまらず、多角的な経営課題の解決にもつながります。具体的には、以下のメリットが期待できます。
それぞれのメリットについて解説していきます。
生産性・稼働率の向上

省人化により、自動化された機器やシステムが人に代わって作業を行うようになることで、生産性と設備の稼働率が向上します。従来は人の手で行われていた工程が、自動化設備によって24時間体制で稼働できるようになれば、ラインの停止時間が短縮され、生産量も安定します。
また、人による作業では休憩や交代などの時間が必要ですが、自動化設備はこれらに左右されず稼働し続けられるため、稼働率の改善にもつながります。加えて、工程のボトルネック解消にも効果があり、生産全体のスループット向上が期待できます。
特に、リードタイムの短縮や短納期対応が求められる製造業において、省人化は生産計画の柔軟性を高める手段といえるでしょう。
品質安定化とヒューマンエラーの削減
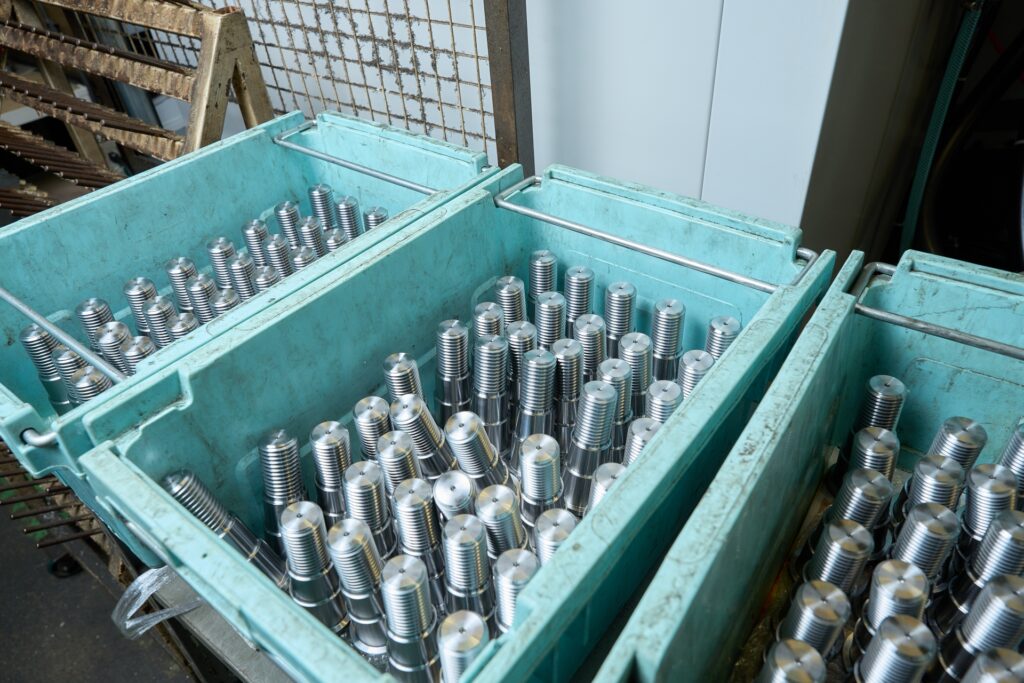
省人化は品質の安定化にも貢献します。人が関与する工程では、技量や体調、集中力などによって作業のばらつきが生じ、製品の品質にも影響を及ぼすことがありました。
しかし、自動化された設備であれば、常に同じ条件で作業が行われるため、品質のばらつきを最小限に抑えることが可能です。また、ヒューマンエラーの削減も省人化のメリットと言えます。
計量ミスや部品の取り付け間違いといった作業ミスは、人が行う限り完全には避けられません。センサーや画像認識技術を活用することで、こうしたミスを自動で検知・修正できる体制を整えられます。
結果として、不良率の低下やクレーム発生の防止にもつながり、企業の信頼性向上にも貢献します。
従業員の負担軽減
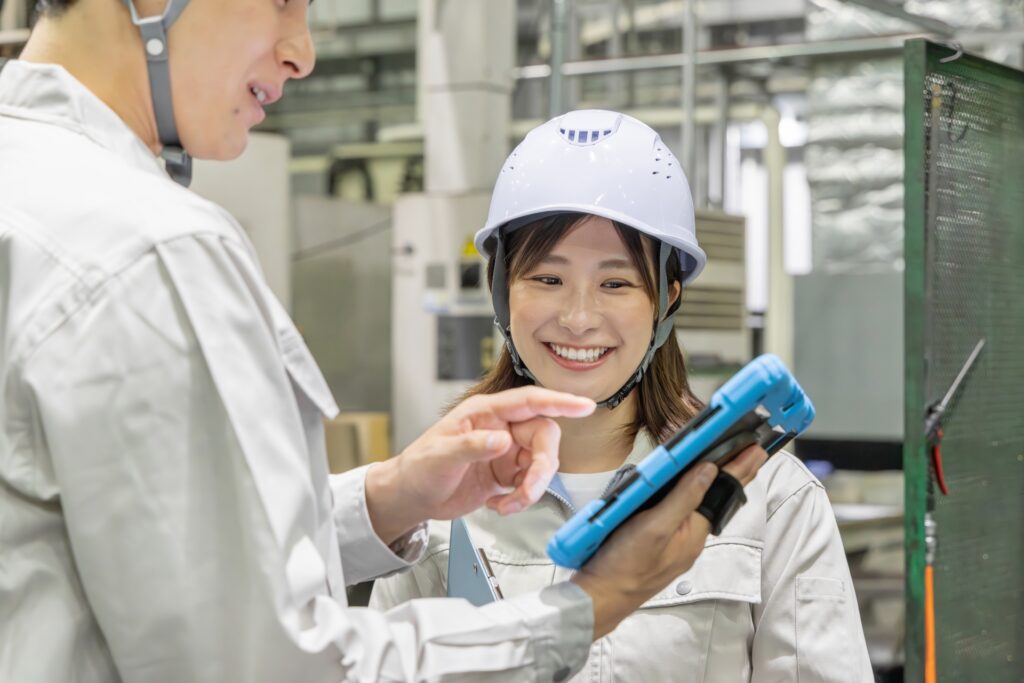
省人化によって、従業員の身体的・精神的な負担を大幅に軽減することが可能です。繰り返し作業や重量物の取り扱いなど、体への負荷が大きい工程を自動化することで、労働環境の改善につながります。
また、単調な作業や高温・粉塵環境下での作業など、敬遠されがちな業務においても、ロボットや専用装置を導入することで作業者の安全を確保できます。これにより、職場の離職率の低下や、新規人材の確保にも好影響をもたらすでしょう。
さらに、省人化によって従業員は単純作業から解放され、より付加価値の高い業務に従事できるようになります。技能継承や修正作業など、人だからこそできる業務へのシフトが可能となり、現場全体のスキルアップにもつながります。
コスト削減
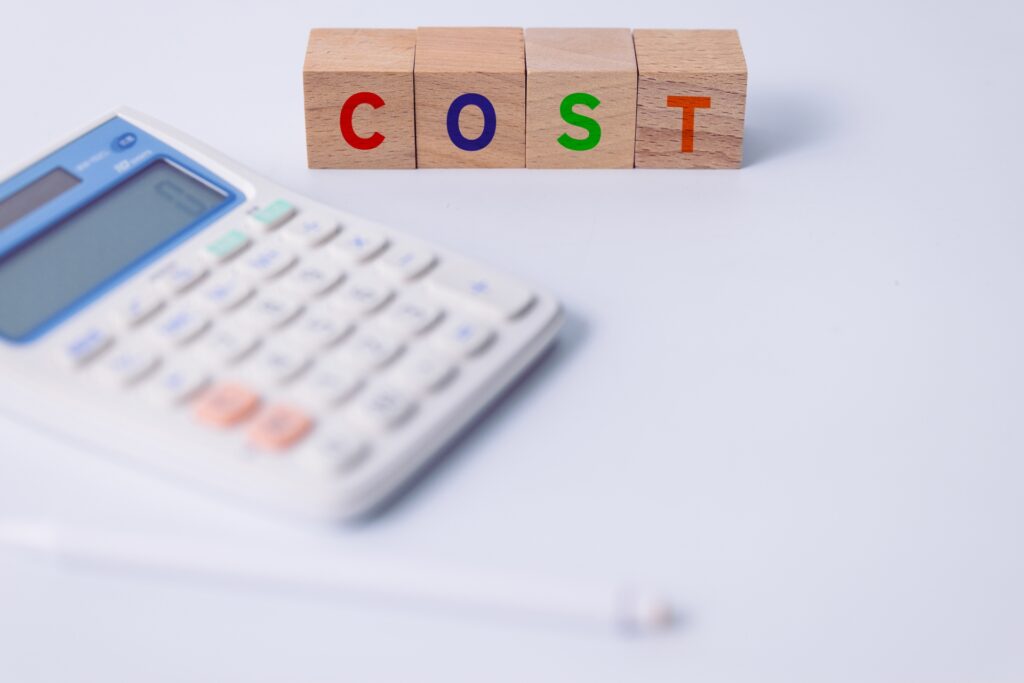
省人化の導入により、製造コストの大幅な削減が可能です。最も分かりやすい効果は、人件費の削減でしょう。自動化機器や計量システムを導入することで、作業員の数を抑えつつ同等以上の生産力を維持できるため、長期的には設備投資以上のリターンが見込めます。
また、教育や研修にかかる時間とコストも軽減可能です。新人育成に必要な熟練者のリソースを他の業務に活用でき、全体の工数も最適化されます。加えて、ヒューマンエラーが下がれば、返品対応などのコストも抑えられるでしょう。
これにより、製造現場の収益性改善が期待できます。
工場省人化が直面する課題
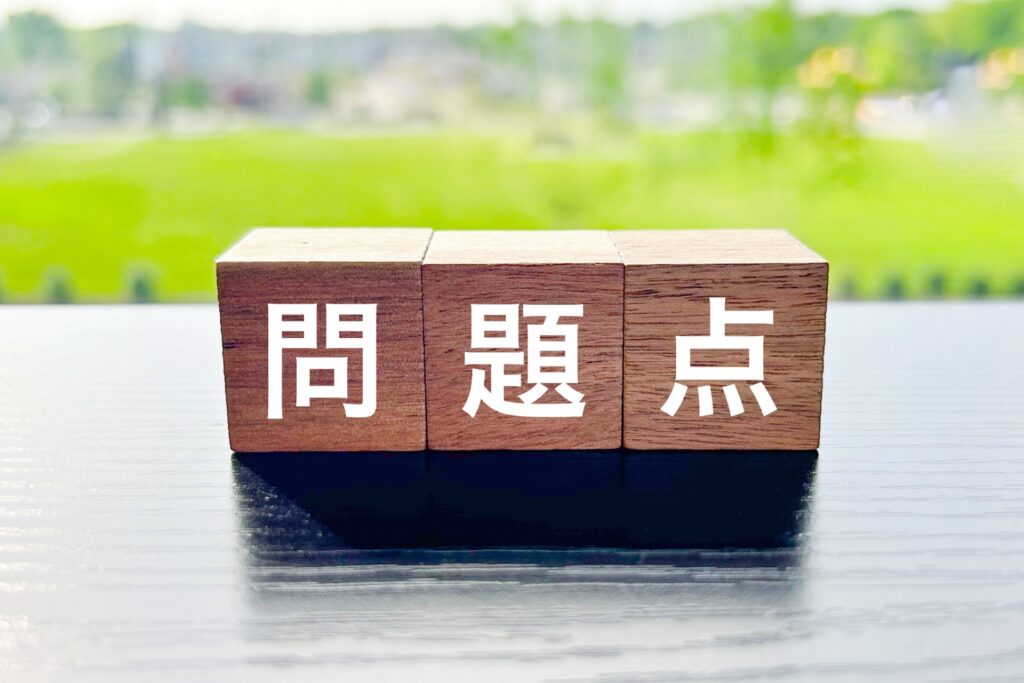
工場の省人化は多くのメリットをもたらす一方で、導入段階においてさまざまな課題に直面することも事実です。特に中小企業では、こうした課題が顕著であり、省人化が進まない要因とも言えます。主な課題は、以下の通りです。
それぞれの課題について解説していきます。
初期投資コストが高い
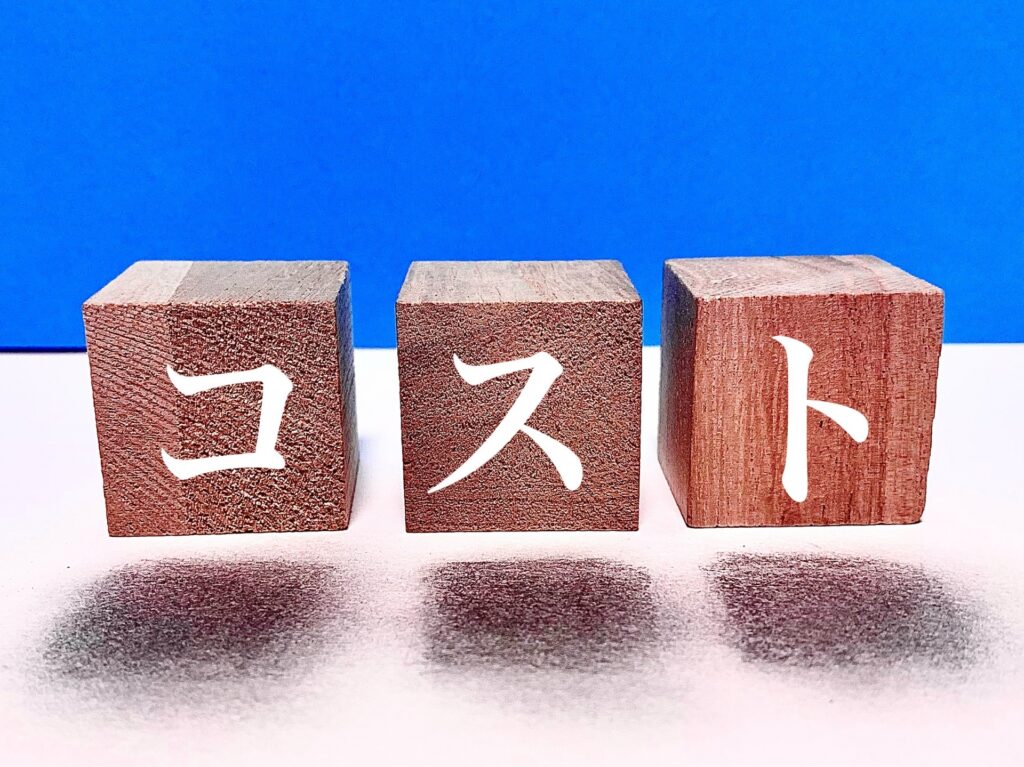
省人化に向けたハードルの一つが、初期導入時にかかる設備投資の高さです。自動搬送機や産業用ロボット、AI搭載の計量装置など、最新の技術を活用するためには数百万円から数千万円規模の費用がかかるケースもあります。
特に中小規模の製造業では、短期的な投資回収が難しく、導入をためらう原因となってしまいます。加えて、機会の設置工事やシステム構築、トレーニング費用などの付帯コストも発生すると、十分な予算の確保は困難です。
とはいえ、省人化は長期的には人件費削減や生産効率の向上による、利益確保につながる可能性が高いため、費用対効果を定量的に評価することが重要です。
現場への技術適合が難しい
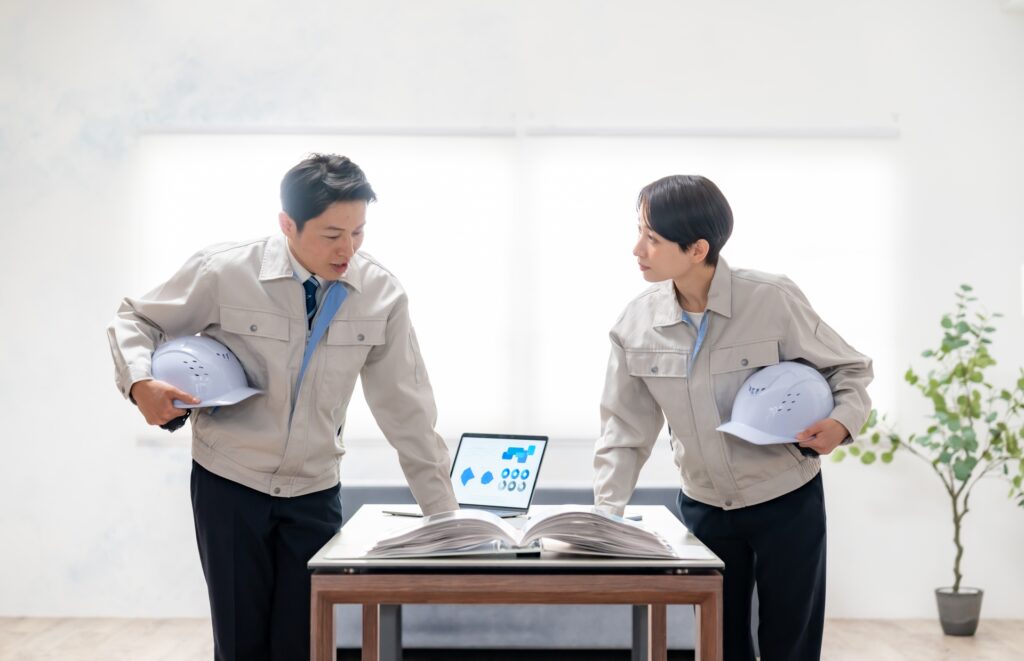
省人化設備を導入しても、現場に適合しなければ効果を発揮しません。製造現場ごとに扱う製品や工程の複雑性は異なるため、汎用的な機械では対応できない場合もあります。
例えば、製品のバラつきが大きい工程や、作業者の感覚を要する工程では、単純な自動化では対応しきれず、設備のカスタマイズや高度なセンシング技術が必要です。また、既存のレイアウトや生産スケジュールに省人化設備を組み込む際に、動線の見直しが求められることもあります。
このように、省人化は単なる装置導入ではなく、全体の業務プロセスに合わせた最適設計が必要です。しかしこうした設計には時間や人材が必要になるため、容易とは言えないでしょう。
IT・メカトロ技術に精通した人材の確保が必要
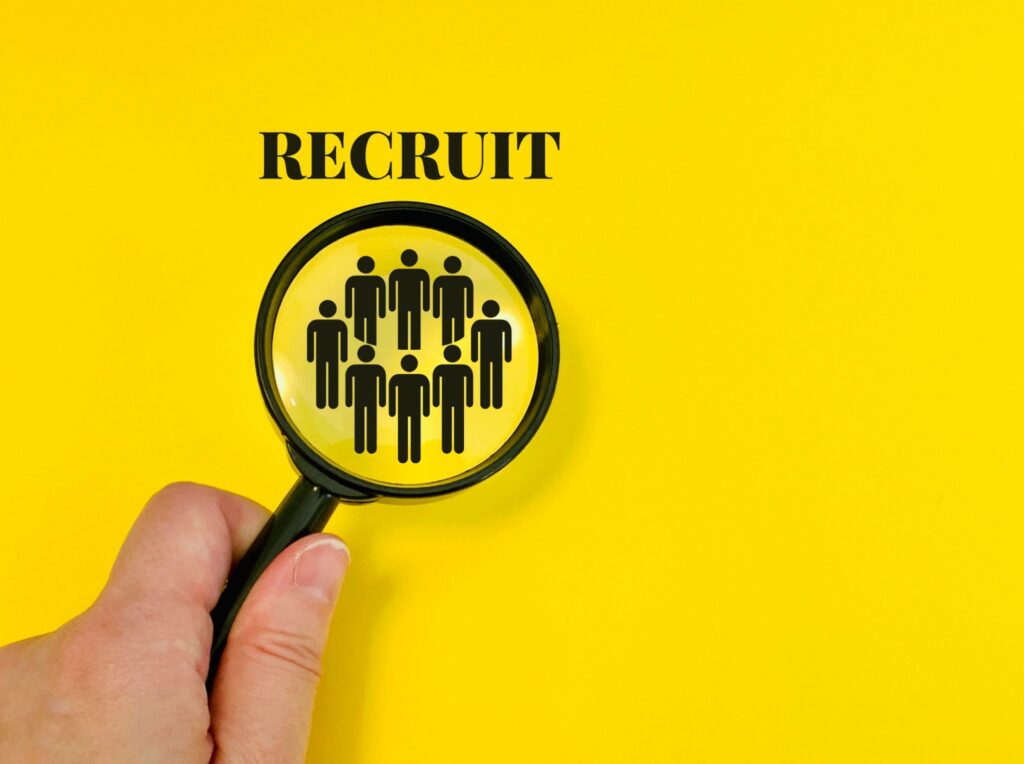
省人化の推進には、ITやメカトロニクス技術に対応できる人材の確保が欠かせません。省人化設備は、以下のような高度な技術要素を組み合わせて稼働しています。
- センサー制御
- PLC(シーケンサ)
- ネットワーク通信
- AIアルゴリズム
そのため、導入後もトラブル対応やメンテナンスを行えるスキルを持つ人材が求められます。既存の作業員にその知見が不足している場合、長期的に安定した運用は難しいでしょう。
しかし、こうした人材は市場でも需要が高く、採用や定着が難しいのが現実です。自社内で育成する体制づくりや、技術パートナー企業との連携が、省人化を安定運用する上で重要な要素となります。
安全性確保・規制整備への対応
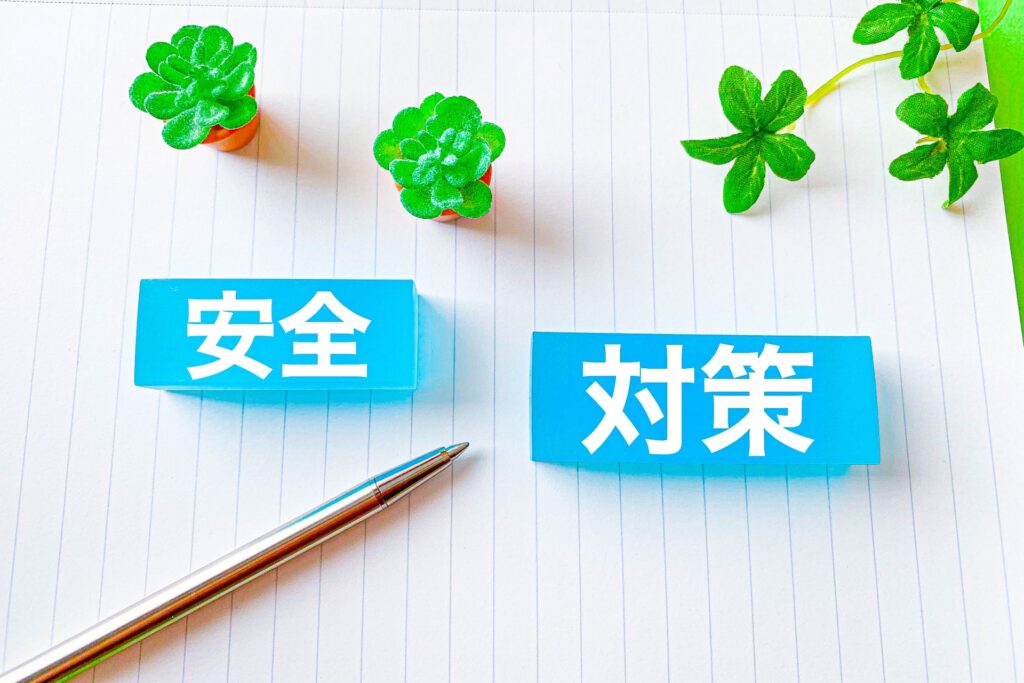
省人化設備を導入する際には、安全性の確保と関連法規への対応が不可欠です。自動搬送車やロボットアームなどは、人と接触する可能性があるため、安全柵や非常停止装置などの設置が義務付けられることがあります。
また、機械装置は労働安全衛生法に基づく安全基準を満たす必要があり、導入前にリスクアセスメントを行うことが推奨されます。省人化によって新たに発生する危険、例えば自動扉による挟まれや無人搬送車との接触にも備えた設計が必要です。
さらに、AIやIoTなど新技術を活用する場合、個人情報保護や通信セキュリティへの配慮も求められます。こうした規制整備にも時間がかかるため、導入のハードルを上げている要因と言えます。
工場省人化の最新手法と技術的アプローチ
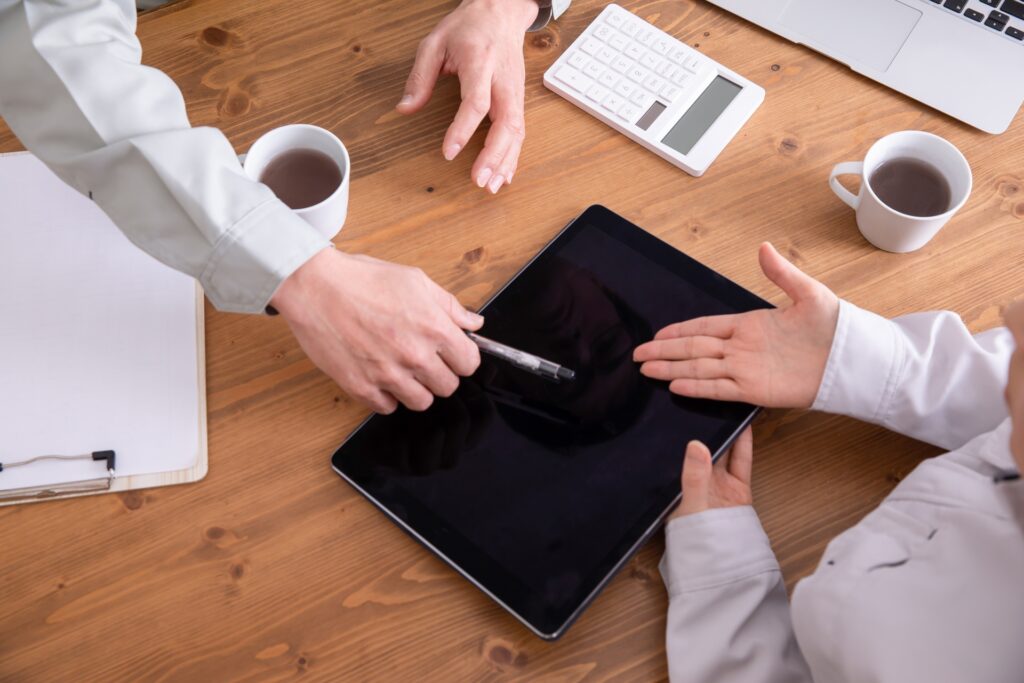
近年の製造業では、従来の自動化設備に加え、先進的な技術を活用した省人化のアプローチが注目を集めています。特にAIやソフトウェアの連携といった領域で進化が加速しており、より高精度な作業が可能となっています。
工場の省人化に貢献する技術として注目されているのが、以下の5つです。
それぞれについて解説していきます。
協働ロボット
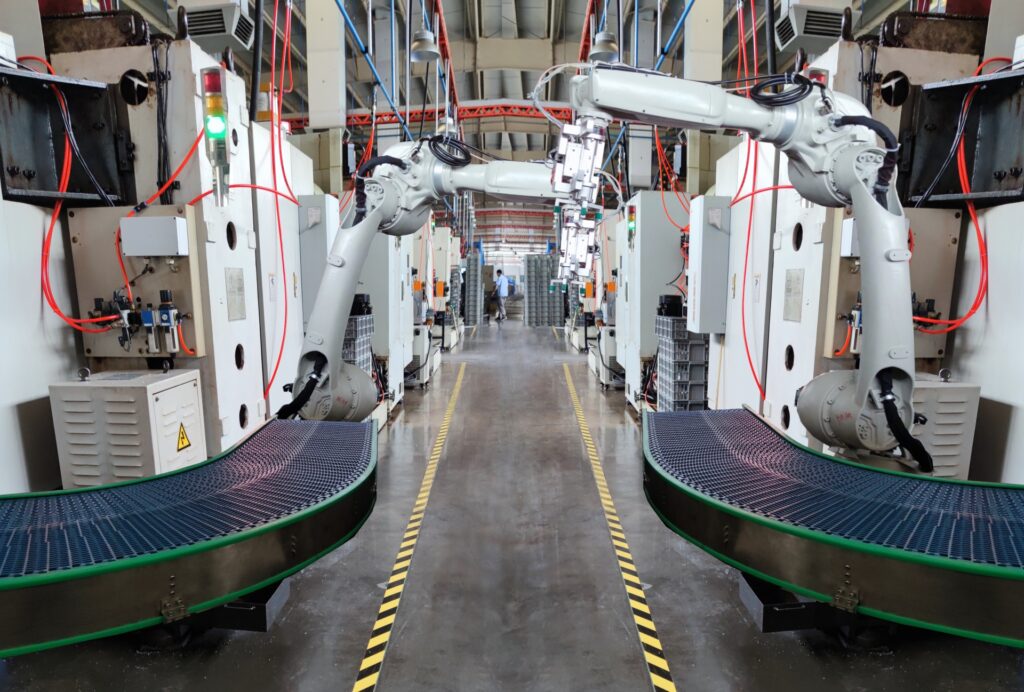
協働ロボットは、人と同じ作業空間で安全に動作できるよう設計されたロボットで、省人化の導入ハードルを下げる技術として注目されています。
従来の産業用ロボットは安全柵で囲うことが必要でしたが、協働ロボットは軽量かつ柔軟な動作が可能で、設置スペースも最小限で済みます。具体的な活用例としては、以下の通りです。
- 組立やネジ締め
- パーツの供給
- 検査補助などの繰り返し作業
特に中小工場では、ラインの一部に協働ロボットを導入することで、作業者の手を空け、生産性を高める取り組みが進んでいます。また、簡単なティーチングにより直感的な操作が可能で、専門知識がない現場でも扱いやすい点もメリットです。
柔軟性と安全性を兼ね備えた協働ロボットは、省人化を段階的に進めたい現場に最適な選択肢といえるでしょう。
画像認識AI
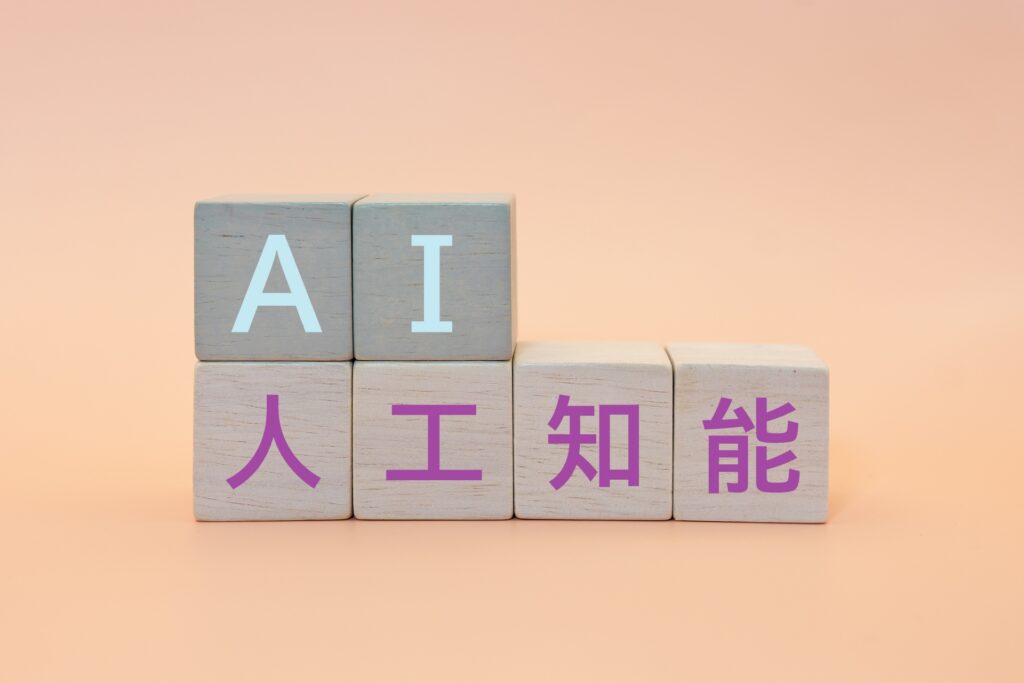
画像認識AIは、カメラとAIアルゴリズムを用いて対象物を分析・判別する技術で、以下の工程の自動化に大きく貢献しています。
- 外観検査
- 異常検知
- 数量確認
従来は熟練作業者の目視に頼っていた検査作業も、AIによって一定の基準で高速かつ安定的に実施できるようになりました。例えば、製品表面のキズ・汚れの検出、欠品の有無、パッケージのラベル判定など、精度が要求される工程で活用されています。
ディープラーニングにより、AIは経験を重ねるごとに精度を向上させていくため、より複雑な判定にも対応可能です。また、人手による検査のばらつきを排除できるため、品質の均一化やトレーサビリティの確保にもつながります。
AGV・AMR(無人搬送車・自律搬送ロボット)
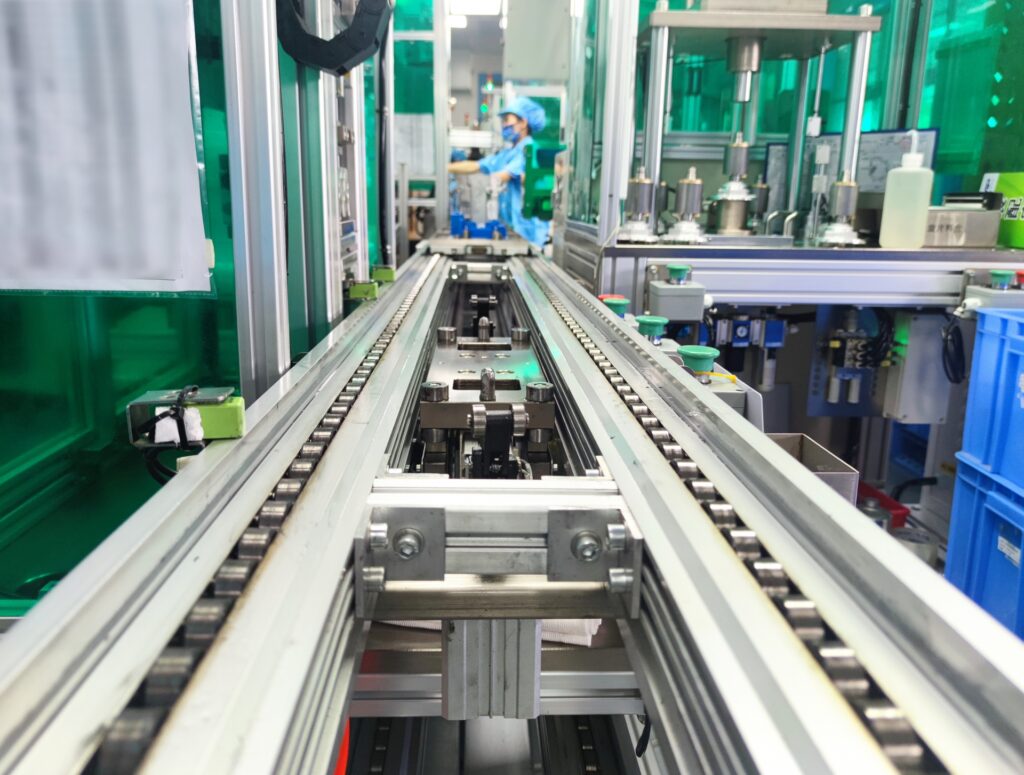
AGV(無人搬送車)やAMR(自律搬送ロボット)は、工場内の物品搬送を自動化する技術です。AGVはあらかじめ設定されたルートに沿って移動するタイプで、ライン間の部品供給や完成品の移送に広く使われています。
一方、AMRは周囲の環境をセンサーで把握し、自律的にルートを判断して動く高度な搬送ロボットです。障害物を回避しながら最適な経路で移動できるため、省スペースな現場やレイアウト変更が頻繁な現場でも対応できます。
これらの搬送ロボットを導入することで、従業員が行っていた運搬作業の負担を軽減し、人手不足の解消や稼働率向上につながります。また、搬送中の事故リスクや疲労によるトラブルも回避でき、安全性の面でも期待できるでしょう。
センサーとIoTデバイスを活用したモニタリングシステム
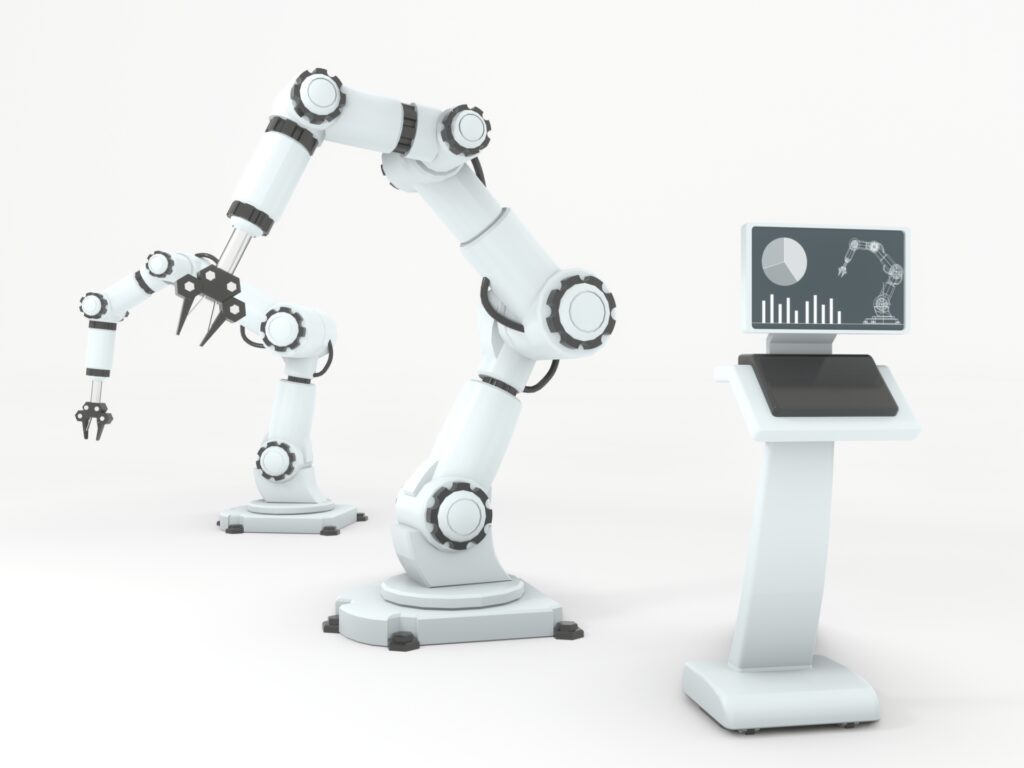
製造現場における省人化では、センサーやIoTデバイスを活用したリアルタイムのモニタリングも有効です。温度、湿度、振動、稼働状況などをセンサーで監視し、ネットワークを通じてデータを集約・可視化することで、異常の早期発見や保守対応の効率化が可能となります。
例えば、計量器や充填装置などの設備にセンサーを取り付けることで、材料の投入量や充填状態を自動的に記録・分析できます。これにより、作業者の巡回点検が不要となり、省人化に直結します。
また、モニタリングデータは分析ツールと連携することで、予兆保全や設備最適化の判断材料としても活用可能です。現場の「見える化」を実現することで、生産の安定性と効率性を高めると同時に、省人化の効果を最大化できます。
MES・ERP連携
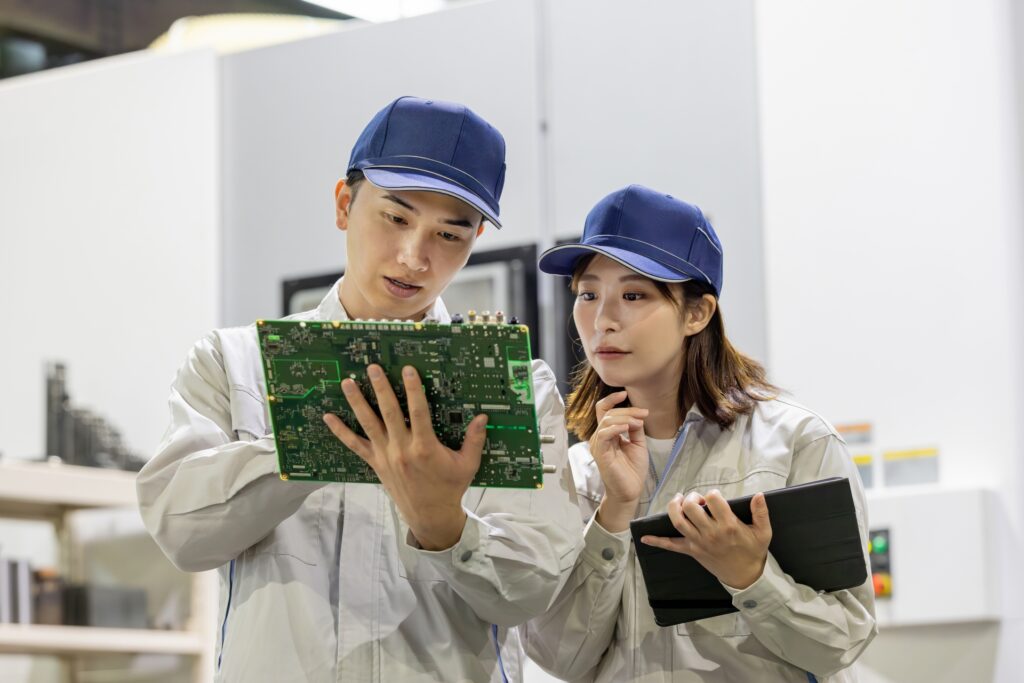
省人化の推進には、工場の各工程を一元管理するシステムの整備も欠かせません。MES(製造実行システム)やERP(基幹業務システム)との連携により、生産管理から在庫、品質、設備稼働データまでを統合的に管理できる体制が整います。
MESは製造現場のリアルタイムな状況を把握し、作業指示や工程の進捗管理を自動で行う役割を担います。これにより、紙ベースの管理や口頭での連携が不要となり、人的ミスの削減が可能です。
一方、ERPとの連携により、調達・販売・在庫管理などの上位業務と現場の動きをシームレスにつなげ、企業全体の業務効率を高めます。特に多品種少量生産の現場においては、柔軟な対応力が求められるため、MES・ERPの導入は効果的です。
情報をデジタルでつなげることで、現場の省人化と経営判断の迅速化を同時に実現できます。
工場を省人化するまでの流れ
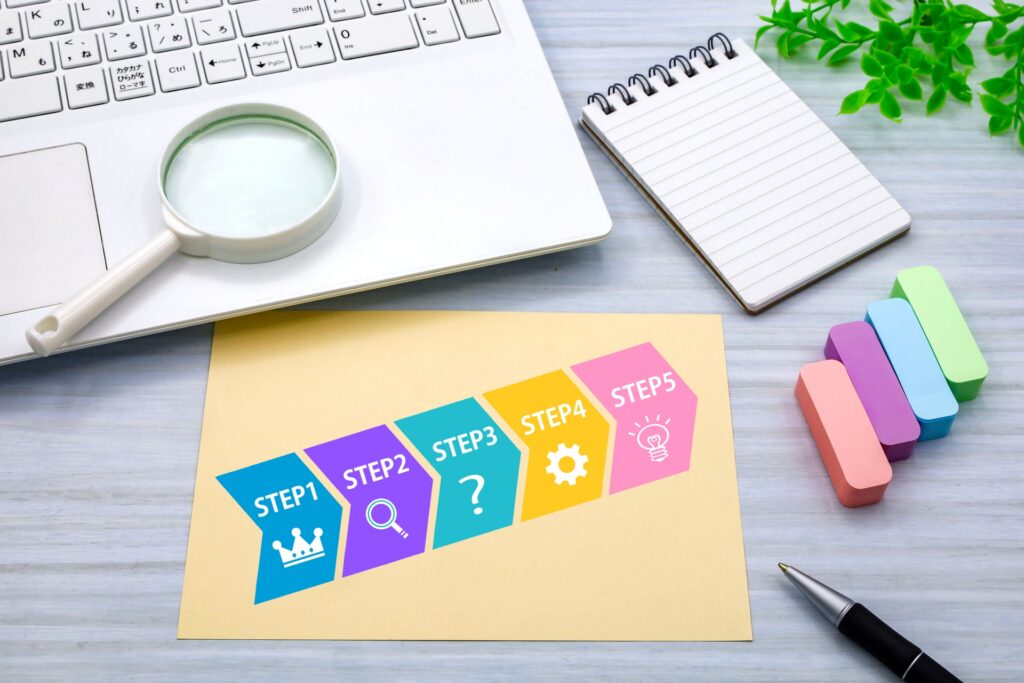
工場の省人化は、目的や予算によって異なりますが、基本的には以下の流れで進めます。
- 現状分析と課題の明確化
- KPI設定
- 適用可能な技術の選定
- 設備・レイアウトの最適化計画
- 段階的導入と試験運用
- システムを活用できる人材育成
- 効果検証と改善
まずは現場の状況を把握し、省人化の目的を明確化することから始まります。その上で、課題となっている工程を特定し、自動化・デジタル化の対象を選定します。
設備導入後は、トライアル運用を通じて現場との整合性を確認し、調整や教育を実施します。本格稼働に移行した後も、稼働状況をモニタリングしながら改善を重ねることで、省人化の効果を最大化することが可能です。
計量プロセスの省人化なら全自動組み合わせはかりがおすすめ!
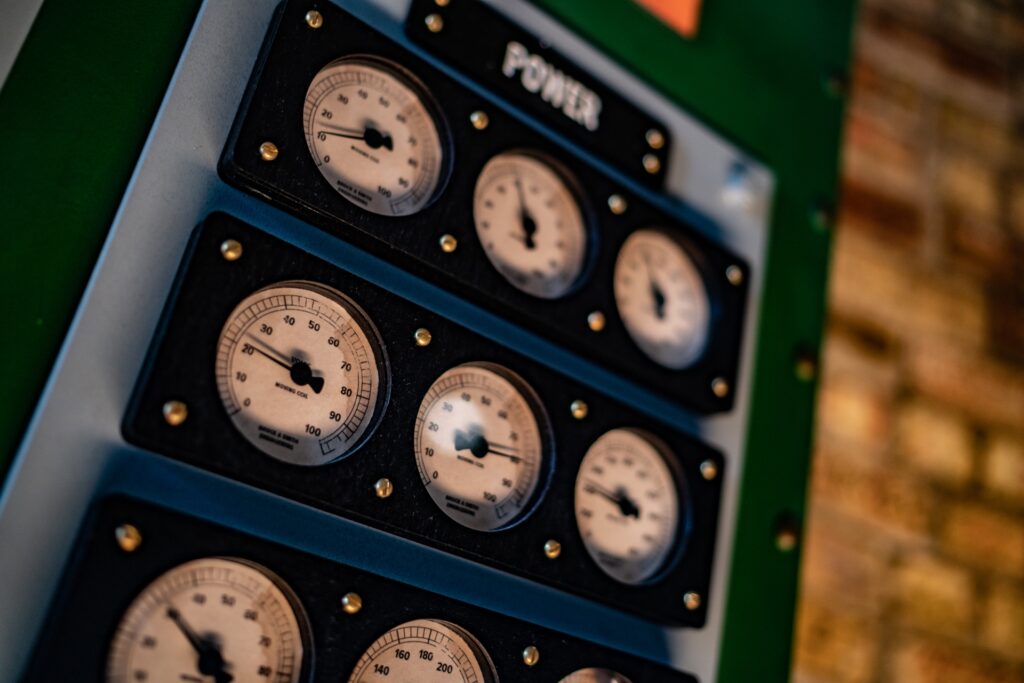
計量工程の省人化を検討している場合は、全自動組み合わせはかりの導入がおすすめです。自動の組み合わせはかりは、人手による目視やスケールを使った計量作業と比べて、スピード・精度ともに格段に向上します。
特に、包装前の食品や部品の計量工程では、一定の重量で正確に供給する必要がありますが、作業者による計量ではどうしてもばらつきやミスが発生しがちです。組み合わせはかりを活用すれば、そうしたヒューマンエラーを最小限に抑えられ、品質の安定化に直結します。
また、タッチパネルによる操作やレシピ登録機能などを備えた機種も多く、段取り替えや設定変更が簡単に行える点も魅力です。多品種少量生産の現場にも対応しやすく、柔軟な運用が可能になります。
計量作業の負担軽減と効率化を両立したい現場には、全自動組み合わせはかりの導入を検討してみてください。
おすすめの全自動組み合わせはかりメーカー3選
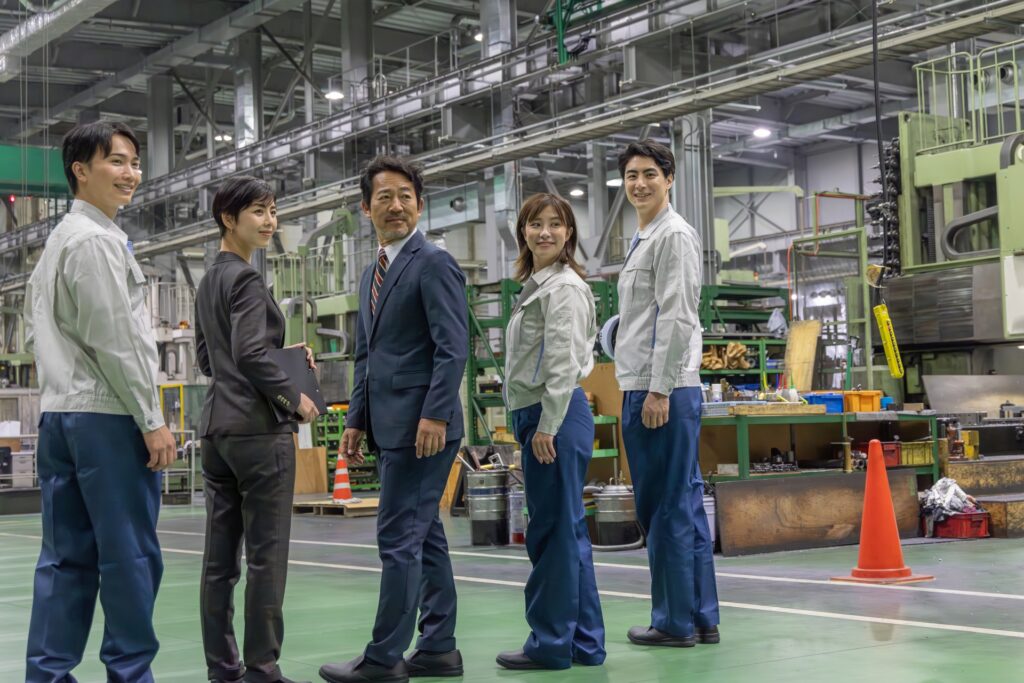
計量作業の省人化に欠かせない全自動組み合わせはかりは、信頼できるメーカーから選定することがポイントです。国内には、精度・耐久性・操作性に優れた製品を提供している実績ある企業が複数存在します。
中でも、食品や部品など幅広い製品に対応し、業界内でも高いシェアを誇るのが、以下の3社です。
それぞれのメーカーについて解説していきます。
大和製衡株式会社
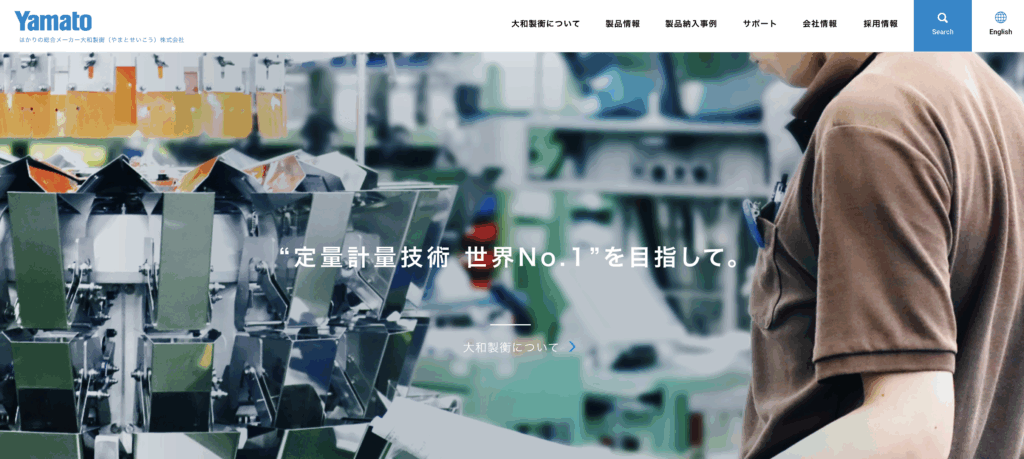
大和製衡株式会社は、はかり専門メーカーとして長年にわたり信頼を築いてきた企業で、全自動組み合わせはかりにおいても豊富なラインアップを展開しています。
項目 | 詳細 |
会社名 | 大和製衡株式会社 |
住所 | 〒673-8688(〒673-0849) 兵庫県明石市茶園場町5番22号 |
電話番号 | 078-918-5526 |
公式HP | https://www.yamato-scale.co.jp/ |
同社の組み合わせはかりは、最大で数十通り以上の組み合わせから最適なパターンを瞬時に選定し、目標重量に限りなく近い計量を実現します。これにより、歩留まりの向上と材料ロスの削減が可能となり、コスト削減にもつながります。
また、衛生面への配慮も万全で、分解・洗浄が簡単に行える構造となっており、HACCP対応の現場でも使用可能です。操作パネルも直感的に使える設計で、初めての導入でもスムーズに運用を開始できます。
全自動組み合わせはかりの導入をお考えの方は、一度の大和製衡株式会社ホームページを訪れてはいかがでしょうか。
以下の記事では、大和製衡株式会社の特徴や口コミ、導入事例などをさらに詳しく解説していますので、気になる方はぜひ一度チェックしてみてください。
株式会社イシダ
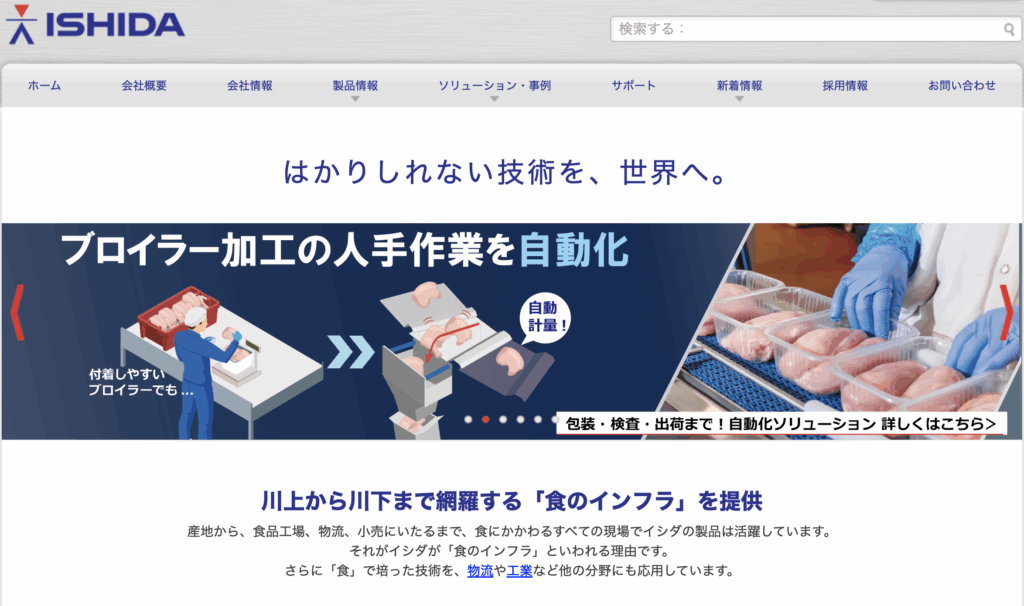
株式会社イシダは、組み合わせはかりのパイオニア的存在として、国内外の幅広い業種で導入実績を持つリーディングカンパニーです。特に同社の「CCWシリーズ」は、高速・高精度かつ多用途に対応できることで知られています。
項目 | 詳細 |
会社名 | 株式会社イシダ |
住所 | 〒606-8392 京都市左京区聖護院山王町44番地 |
電話番号 | 075-771-4141 |
公式HP | https://www.ishida.co.jp/ww/jp/ |
イシダの組み合わせはかりは、独自のデータ処理技術と安定した制御アルゴリズムにより、高速でも精度を落とさず連続計量が可能です。さらには、自動フィードバック機能によって過剰充填を防ぎ、計量誤差の最小化に寄与します。
また、IoTとの連携や遠隔監視機能も充実しており、生産ラインの可視化や品質管理の効率化にも貢献します。多言語対応の操作画面や、ユーザーレベルごとのアクセス制限など、現場での運用に配慮した設計も強みです。
以下の記事では株式会社イシダの評判や特徴について紹介しているので、ぜひ参考にしてください。
アンリツ株式会社
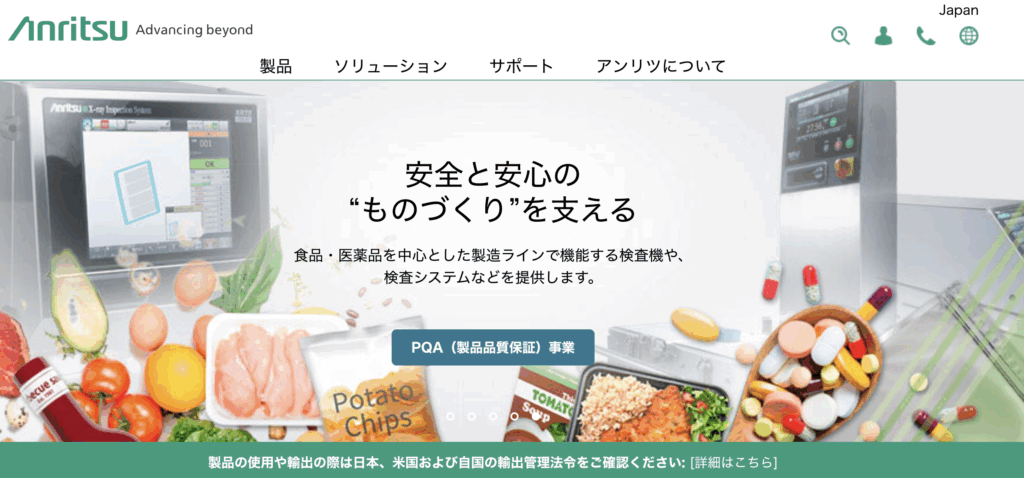
アンリツ株式会社は、もともと通信機器で知られる企業ですが、計量・検査分野でも高い技術力を持ち、全自動組み合わせはかりの分野でも確かな実績があります。
項目 | 詳細 |
会社名 | アンリツ株式会社 |
住所 | 〒243-8555 神奈川県厚木市恩名5-1-1 |
電話番号 | 046-223-1111 |
公式HP | https://www.anritsu.com/ja-jp/ |
特に、X線検査機や金属検出機と連動可能な計量ソリューションを提供しており、総合的な品質管理を実現できる点が強みです。
アンリツの組み合わせはかりは、堅牢な設計と精緻なロードセル技術により、重量誤差の少ない安定した計量を実現します。また、インラインでの異物検査や表示ラベル確認機能との連携により、計量から検査、出荷までを一括管理できるスマートな運用が可能になります。
食品製造だけでなく、電子部品や化学原料など、厳密な品質管理が求められる業界にも適したソリューションを提供しているメーカーです。
以下の記事ではアンリツ株式会社の評判や特徴について紹介しているので、ぜひ参考にしてください。
まとめ
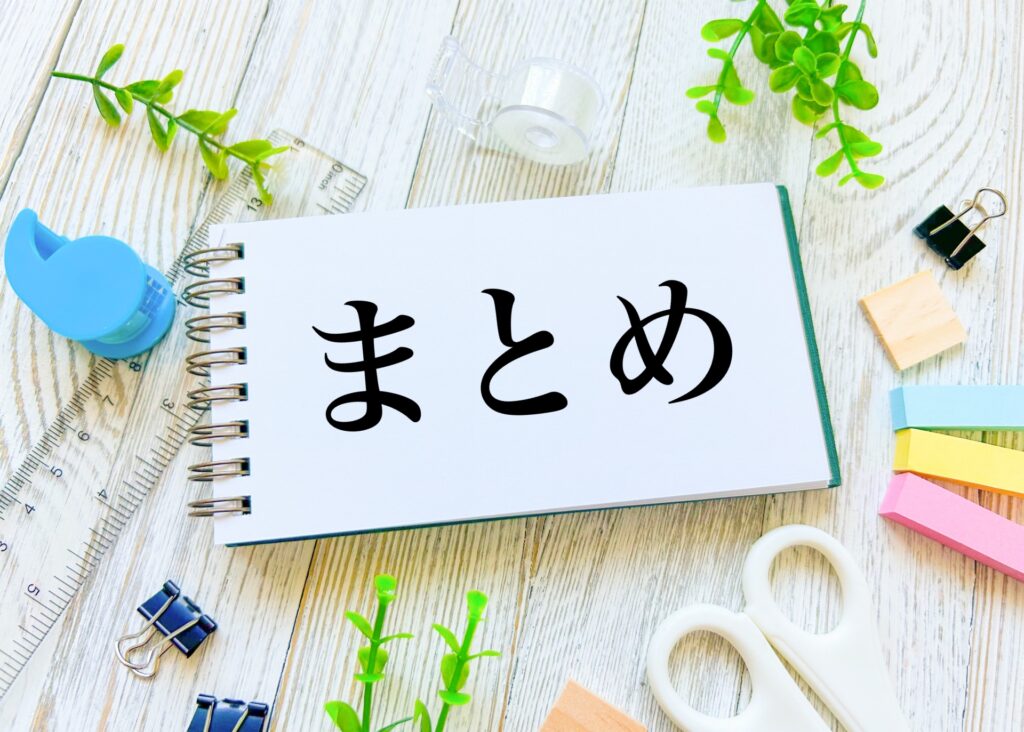
工場の省人化は、人手不足への対応だけでなく、生産性の向上や品質の安定、コスト削減にもつながる重要な施策です。しかし、初期投資や技術面のハードル、安全性の確保といった課題も多く、戦略的な対応が求められます。
その中でも、計量工程は省人化しやすい領域の一つであり、全自動組み合わせはかりを導入することで、作業の効率化と精度向上を同時に実現できます。信頼性の高いメーカー製品を選べば、導入後の運用もスムーズに進められるでしょう。
今後省人化を進める際は、自社の課題や現場を整理し、段階的に技術導入を検討することが重要です。現場の生産性を高め、持続的な成長を実現するためにも、計量をはじめとした自動化可能な工程から見直しを始めてみましょう。